Latest News
January 1, 2015
Molding or shaping plastics into usable forms is not new technology, however, the way plastics are being produced and brought to us is becoming faster every day. The injection molding process begins with an idea that is conveyed into sketches, then into 3D CAD models. During the planning stages, this is the moment where bottlenecks can occur because getting quotes from manufacturers can take up valuable time. The Instant Online Quoting & Project Management System developed by ICOMold presents injection molding and CNC manufactured parts customers with instant quotes to streamline the quoting and budgeting step in your project.
Unlearning What You Have Learned
The days are over of sending your file to a third party, waiting several days (or weeks) then repeating that process when your design needs to be tweaked. Three-dimensional computer aided design models, as you know, are more complex than just computer drawings or hand-drawn sketches. They contain mathematical (vector-based) information regarding angles, curves, weight, and material thickness. Within the paradigm of computer-aided technology, calculating a quote for a even a simple CAD model isn’t as easy as throwing a number off of the top of one’s head, and it’s compounded exponentially for large or complex injection molds, parts and CNC milled parts.
ICOMold’s Instant Quoting System analyzes your .STP CAD file once uploaded and processed by ICO’s servers. Then, as you change part quantities, materials, colors, number of mold cavities, family mold and shipping options, the quote on your screen updates instantly. CNC machined parts can also be quoted instantly in the new system. The Instant Online Quoting System also has the capability to allow you to view your uploaded parts in real time. ICO Viewer™ displays your part and allows you to manipulate it in three-dimensional space, zoom in and out, display the dimensions of the part, and calculate approximate measurements between chosen points to mention some of the features.
CAD Engineers and project managers now have the ability to better manage their project’s budget and minimize the impact of lost time by having the cost of their project instantly, rather than waiting for days for a quote. Once your unconfirmed quote is submitted, your project is a step closer to deployment.
Nothing Beats the Human Touch
An instant quote is usually pretty accurate with the cost of your project, but the one thing that any automated system lacks is the human touch. That’s where ICOMold’s project management engineers analyze your project for moldability and other technical nuances that even the most advanced computer logic and algorithms simply cannot catch. Most times, a project is green-lighted immediately after moldability analysis because the part design is moldable or millable. However, there are some designs that may not be viable due to the aforementioned technical nuances. This is when your project management engineer will reach out to inform you of a design flaw or a minor change that can get your project back on track or possibly alter the cost of the project. Once the project managers have confirmed your quote, they will send a firm quote back to you for your approval.
Simple Project Management
If your project has mulitple pieces for an assembly, you may opt to choose a family mold for production of those parts. If you have multiple projects, all of your uploaded projects appear on your personal online project management site. All of your confirmed, unconfirmed, and launched projects remain in the Instant Quoting and Project Management System for you to access at any time. Also, notes about projects and email communication between you and project managers are also handled inside the system, and are kept organized by project.
To learn more about ICOMold’s Instant Online Quoting and Project Management System, go to www.icomold.com/icoquote.
Subscribe to our FREE magazine,
FREE email newsletters or both!Latest News
About the Author

DE’s editors contribute news and new product announcements to Digital Engineering.
Press releases may be sent to them via [email protected].
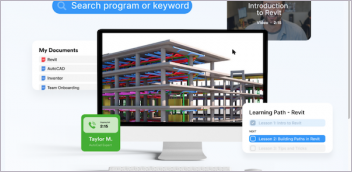

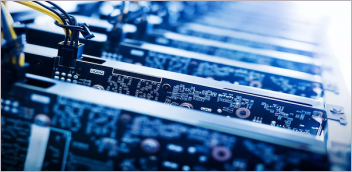
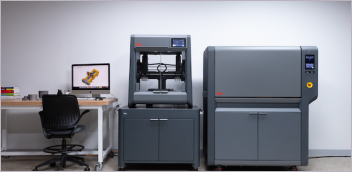