Finalists of Design for Additive Manufacturing 2020 Named
From a record number of 151 contestants, professionals and students, three finalists were selected per category.
Design for Additive News
Design for Additive Resources


Additive Industries

Latest News
February 21, 2020
In late, February 2020, Additive Industries announced the finalists of the Additive World Design for Additive Manufacturing Challenge 2020. From a record number of 151 contestants, professionals and students, three finalists were selected per category.
“We are pleased to notice that amount of contestants from all around the world increased, compared to last year, by 25%,” says Daan Kersten, CEO of Additive Industries. “The designs are submitted from all over the world and across different applications fields including automotive, aerospace, medical, tooling and high tech. They all demonstrated how product designs can be improved when the freedom of additive manufacturing is applied. This year again many interesting potential business cases were spotted, where within both categories we saw major focus on the elimination of conventional manufacturing difficulties, minimization of assembly and lowering logistical costs.”
This year, the professional category consisted again of many innovative designs, according to organizers.
Professional Category Finalists
Nina Uppenkamp from SMS Group (Germany) demonstrated how media blocks, used as fluid-conducting components, can be designed for optimum flow, where both the space and size can be reduced because of additive manufacturing. Compared to a conventionally manufactured hydraulic valve block, her design brings efficiency gains because there is no need for plug screws also reducing the number of potential leaks. As a result of this, and by changing the material from cast steel to the AlSi10Mg aluminium alloy, a reduction of weight by 90% has been achieved.
Another professional, Donatien Campion from 3DMedLab (France) shows how the expandable intervertebral cages, when metal 3D printed, can be advantageously used in the medical field. The motivation for this project was to overcome a strong limitation of material, but still imagining an innovative design, that might be beneficial for both patients and surgeons. 3D printing an expandable intervertebral cage as a single part, could minimize several risks during the medical procedure by reducing the part count and insertion of the device. Since this design is still a concept of an inspirational medical application, it will need more research before it can be used on patients.
The third finalist of the professional category is last year's winner of the Design Challenge, K3D from the Netherlands, together with Hitech Bihca, submitting a joint redesign of a laser welding head. By 3D printing the laser welding head, multiple issues in the production environment were solved. This results in lower downtime, better welds, no damage to the laser or products and a higher productivity.
Other Finalists
In the student category this year is a medical application by Younes Chahid from BiomimeticAM with the Hip Implant Stem Design, from the University of Huddersfield (UK). With this redesign of the hip implant stem, issues with implant revision surgeries and bone resorption could be greatly improved. The new design of the hip implant stem has many such features including density and thickness distribution optimization to reduce the stress shielding and increase osseointegration.
The team SCUT Robotlab from South China University of Technology (China) improved the stabilizer mount on the robot for the RoboMaster competition, a key component which connects the mobile system with the upper projectile system. The original assembly consisted of 27 parts and weighed 295 grams.
Samir Mulgaonkar from Sunriser (California) made the Brake Caliper Design with an idea to improve the sustainability and emissions produced by cars through light weighting components. Extra energy is required to accelerate or decelerate excess mass of a car. Mulgaonkar is looking to save energy by a generative design of the caliper where the weight of the caliper can be reduced by half.
This year there is an honorable mention in the professional category. This mention is for the Ducting Bracket from Aravinth Kamaraj, SPAREPARTS 3D (France). This ducting bracket is one of the most commonly used rail components across all the levels of ducting system, what makes the case study of Aravinth Kamaraj relevant. The result of the case study shows that design freedom from additive manufacturing coupled with topology optimisation tool can make a big difference in the design and economics of product development phase compared to traditional manufacturing.
Sources: Press materials received from the company and additional information gleaned from the company’s website.
More Additive Industries Coverage
Subscribe to our FREE magazine,
FREE email newsletters or both!Latest News
About the Author

DE’s editors contribute news and new product announcements to Digital Engineering.
Press releases may be sent to them via [email protected].
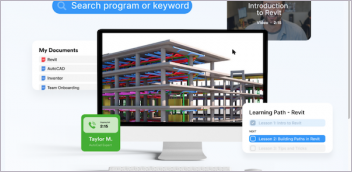

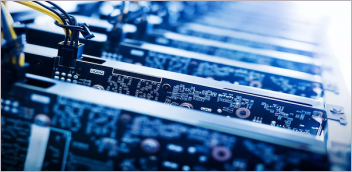
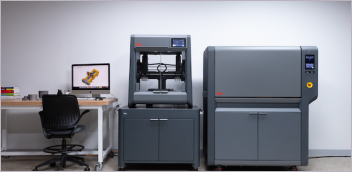