Latest News
November 1, 2010
By Peter Klein
![]() Finished fan with freeform blades. This component did not require an integrated shroud. |
Xcelaero Corporation of San Luis Obispo, CA, specializes in custom-vane axial and radial fans for the commercial and defense industries. It uses techniques and technologies adapted from the aviation and gas turbine industries to achieve fan efficiencies.
Typically, Xcelaero’s axial fan designs use complex shrouded vane sets, which present manufacturing challenges due to a lack of tool access and minimal spacing between vanes. Xcelaero is successful, in part, because it purchased 5-axis computer-aided machining (CAM) software from Concepts NREC (CN) of White River Junction, VT.
“To prototype our fans we purchased a 5-axis vertical machining center and coupled it with CN’s 5-axis CAM software family including the MAX-PAC and MAX-SI packages specifically for shrouded vane sets,” says Bill Denzel, engineering manager at Xcelaero. “Additionally, we chose to use the CN CAM family because it merged seamlessly with our impeller design software.”
Denzel added that 3D modeling is not required to generate vane toolpaths. Therefore, Xcelaero’s shrouded vane designs transfer directly from its aerodynamic design software to the CAM software without generating an intermediate 3D model. This transition helps ensures the vane design cannot be corrupted by the 3D modeling or import-export processes. However, MAX-PAC is also capable of importing 3D CAD models.
![]() This closeup shows flowline milling passes on an integrally shrouded wheel. |
The Challenge
Before purchasing the CN CAM suite, Xcelaero used another commercial CAM program to create 3+2 and 5-axis toolpaths to machine impellers and shrouded vane sets. This solution, however, required several iterations to find the optimum tool-approach angle and confinement window. Additionally, the CAM software produced a patchwork of surfaces that were difficult to blend together.
The challenge was to find CAM software that improved the efficiency of toolpath generation, while also integrating with Xcelaero’s existing fan design software and creating continuous 5-axis blade and vane surfaces.
Finding a Solution
“The CN software family was recommended to us by a consultant who specialized in programming 5-axis toolpaths,” says Denzel. “The consultant had utilized several other CAM packages and recommended CN as the predominant CAM programming supplier for serious fan manufacturers.”
Xcelaero’s machine shop manager spent three days training onsite with a CN application engineer. The first two days were spent introducing the basics of the CN software family, and the third was spent creating code specifically for Xcelaero’s fan designs.
![]() A fan positioned inside stationary shroud housing. |
CN software runs on Windows 2000, XP, NT, or Vista and does not require advanced processor or graphics hardware. Xcelaero’s computers were more than adequate, so the company did not have to purchase any additional equipment.
MAX-PAC uses a collision detection and avoidance algorithm that enables the use of larger, stronger cutting tools than are available on other CAM systems. So-called “lollipop” tools, with a cutting ball on the smaller shank, can be used to reach areas that are not visible to the eye.
The CAM software automatically calculates the optimum approach angle given the blade, tool, and tool holder geometry, which significantly reduces the length of time required to generate toolpaths. The resulting 5-axis toolpaths produce seamless vane surfaces particularly at the leading and trailing edges and vane root fillets.
“CN’s software included several toolpath routines written specifically for blades. We prefer to use the flow line option that generates toolpaths to follow flow lines around the blades,” says Denzel. “The flow line toolpaths allow us to use a larger step-over between tool passes and reduce the overall manufacturing time while not sacrificing surface roughness in the direction of the flow.”
![]() Fan on 5‐axis machine in a semi‐finished state. |
Return on Investment
By implementing the CN MAX-PAC CAM software family, Xcelaero reduced the time required to create 5-axis programs for shrouded vane sets from one week to two days. Additionally, the toolpaths generated reduced manufacturing time by 40% by eliminating the need to flip the shrouded vane set over. And, Xcelaero virtually eliminated the production of scrap parts during the initial prototyping process.
Peter Klein is the associate director of CAM Software at Concepts NREC. Send comments on this article to [email protected].
Subscribe to our FREE magazine,
FREE email newsletters or both!Latest News
About the Author

DE’s editors contribute news and new product announcements to Digital Engineering.
Press releases may be sent to them via [email protected].
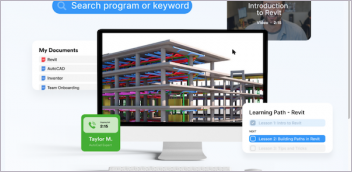

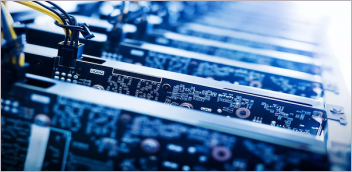
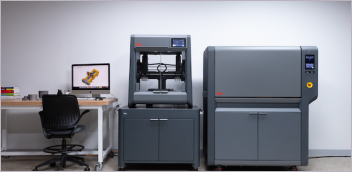