Fast App: Vero Software Helps Reinvent the Wheel
Lamiflex uses Vero's VISI suite of design and manufacturing tools to put a composite spin on the traditional exercise bike.
Latest News
April 12, 2011
By Marc Freebrey
![]() The outline makes the Ciclotte instantly recognizable in terms of design aesthetics. |
The Lamiflex Group, based in Bergamo, Italy, has been an industry leader in the use of composite materials for more than 30 years. It has supported various industries, including aerospace, medical, telecommunications and the sports sector.
The company began in 1976, inventing and developing rapier ribbons made from composite materials for the textile machinery industry. However, constant research and investment has allowed Lamiflex to expand into other market sectors, such as aerospace, where it uses a special “autoclave polymerization of composite materials” process, certified by AgustaWestland. The process allows the company to produce both stiff and flexible lightweight ducts for environmental control systems (ECS) installed in aircraft or high-performance vehicles and machinery used by the military.
Composite materials are, by definition, structures made up of several component materials. These typically include thermoset resins strengthened with carbon, Kevlar or glass fibers, which provide certain characteristics (usually mechanical) and a matrix that holds the fibers in position, protects them and offers other specific characteristics for particular applications. Laminated composite materials can be produced as sheets of continuous strands of fiber, layered so that each fiber lies in a specific direction. This means that reinforcement is only added where needed. This way, the amounts of material used can be optimized—and the weight of each product is kept to a minimum.
The main purpose behind the development of composite materials is, without a doubt, their high ratio between density and mechanical strength, letting one get performance levels similar to those of metal (or even higher), but at far lighter weights (50% less).
In 2009, Lamiflex was involved in the development of an innovative piece of fitness equipment designed by Italian product designer Luca Schieppati. The Ciclotte is an exercise bike with an ultra-modern carbon fiber frame, touchscreen display and reduced pedal distance to ensure the correct bio-mechanics throughout the complete leg rotational movement.
The large central wheel forms the cornerstone of the design, and is reminiscent of the classic unicycles dating back to the late 19th century. However, the Ciclotte has been designed to accurately reproduce the dynamics and performance of on-road pedaling. It’s ideal for high-intensity aerobic training such as “spinning,” which is all possible because of the innovative epicycloid crank system: a dual-satellite system that uses four gears with varying cogs in a functional space of only 58mm. By multiplying the number of flywheel rotations—about four flywheel rotations to every pedal rotation—it helps generate a high-intensity magnetic field (from the main wheel), which maximizes the resistance level and produces plenty of thigh-burning resistance.
![]() 5-axis kinematic simulation |
The Ciclotte traces its roots to the Ciclò project, an innovative prototype of a single-wheel city bike, which is now part of the permanent collection exhibited at the Triennale Design Museum in Milan, Italy.
“The concept from Luca Schieppati excited our company, and we wanted to help bring the product to life using our vast experience of modern composites,” explains Federico Carrara Castelli, R&D Director at Lamiflex and Ciclotte project leader.
At the beginning of 2009, a first aesthetic prototype was produced to test the market feedback before moving onto a fully functional prototype. To guarantee the exact requirements and size of all functional mechanical components, including the carbon-fiber handlebar and saddle, all components were designed in 3D and simulated as a virtual assembly to highlight any potential issues prior to the assembling procedure, where more than 60 separate components are finally brought together.
![]() VISI Machining 5-axis |
To coincide with the Ciclotte project, Lamiflex also took time to evaluate the software market and invest in a new integrated CADCAM system.
“Previously at Lamiflex, we used a parametric CAD system that we found difficult to use and quite restrictive when working with complex organic surface forms,” explains CAD designer Marco Perani. “After extensive benchmark testing, we decided to implement VISI from Vero Software, as we believed it offered the best balance between performance and price. We are currently running multiple licenses of VISI Modeling and VISI Analysis for Design, and VISI Machining with Compass Technology for 2D through to five-axis milling.”
Castelli says that Lamiflex has used VISI for the design and manufacture of all composite mold parts that were used to build the Ciclotte.
“With regards to the molds for the carbon fiber wheel and the handlebar, all of this was achieved in less than 100 hours of CAD work,” he says.
Once the molds were complete (and polished), the fabric and epoxy resin are applied, and then inserted into a vacuum bag and placed inside the autoclave for the curing process. Once hardened, the parts are then passed through to the CAM department for finish machining.
“We run several milling machines, including two simultaneous five-axis ]computed numerically controlled] running VISI Machining,” says Castelli. “For the finish machining of the composite products, the ‘trimming’ method is often used, where the side of the tool is driven along the surface edge. For additional control, synchronization curves can be used to control the tool movement in local areas, where the potential direction changes are at their most extreme.”
For the machining of planar holes, Castelli says, the tool is tilted perpendicular to the surface, but when product holes are difficult to reach, an extra tilting of the tool is required to avoid collision with the tool holder.
“When the toolpath is complete, the machine operator is able to virtually walk through the complete program using the kinematic simulator and prove the toolpath is collision-free,” he says.
Castelli concludes that the software helped make the project a success.
“Introducing the software has streamlined our manufacturing processes, reduced the potential for error and ultimately increased our productivity,” he says. “We are a company always looking for innovative, often revolutionary solutions—and consider Vero to be an important partner in this philosophy.”
More Info:
Lamiflex Group
Vero UK Ltd
Contact Marc Freebrey at [email protected].
Subscribe to our FREE magazine,
FREE email newsletters or both!Latest News
About the Author

DE’s editors contribute news and new product announcements to Digital Engineering.
Press releases may be sent to them via [email protected].
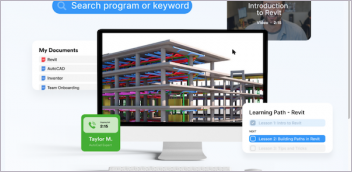

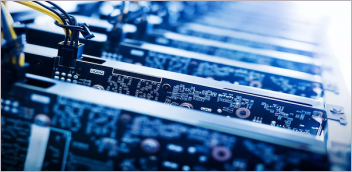
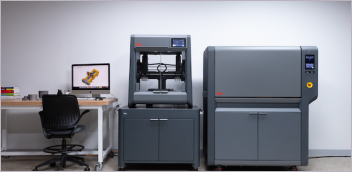