November 1, 2010
By DE Editors
![]() |
In 50 years of business, Valiant Machine & Tool Inc. has forged a reputation for out-innovating its competition. While the company traditionally has developed manufacturing products for automotive, construction, and forestry industries, Valiant began applying its creative engineering expertise to aerospace industry projects with impressive success.
In recognition of this success, Boeing recognized Valiant as a “Supplier of the Year” for 2007 in the “Non-Production/Shared Services” category.
At the core of Valiant’s innovative designs are Autodesk Inventor Professional software and Autodesk Algor Simulation software, which enable Valiant to more quickly assess whether a new idea is a dead end or a promising beginning. With help from Autodesk Inventor software and Autodesk Algor Simulation software, Valiant has been able to:
• Develop a portable cargo loader for Boeing
• Communicate ideas with animated 3D models, impressing customers
• Reduce errors and design time by conducting mechanical simulations in-house
![]() |
The Challenge
Valiant relies on Autodesk Inventor software to design a wide range of products, from powertrain manufacturing equipment for automotive original equipment manufacturers (OEMs) to aerospace tooling, assembly, and ground support equipment for aerospace manufacturers.
“Inventor is so intuitive. It lets us test different concepts very quickly,” says Tom Stein, a mechanical and simulation research and development engineer at Valiant. “It definitely gives us a competitive advantage when we’re developing something that’s never been done before.”
Valiant faced a challenge when Boeing asked the company to design ground support equipment for transporting parts required for assembly of a new aircraft.
“Boeing needed a portable cargo loader that could be put on pallets and transported by a cargo freighter,” explains Dominic Baulier, director of research and development at Valiant. “We had to make sure our design would not exceed a fixed number of pallets, the pallet’s dimensions, and aircraft load requirements.”
The Solution
Even though Valiant had to deliver files in a format other than Autodesk Inventor, the company decided to use the software to develop the cargo loader design. Valiant’s design team determined that using Inventor provided sufficient advantages to justify the need to convert the model to the format used by Boeing.
“Using Autodesk Inventor software, we developed a digital prototype very quickly,” says Baulier. “Our proposal included an animated digital model that helped us demonstrate to Boeing how we’d already thought through the entire system. Inventor played a key role in helping us win the project.”
Non-Native Data
After winning the project, Valiant simply built out and refined its concept model in Autodesk Inventor software. The team had no trouble working with non-native data, which was particularly important since Boeing uses a different CAD package.
“It’s very easy to import data sets from other common design formats into Inventor—and it saves time and reduces errors,” says Andrew Pawelski, CAD support at Valiant. “We used that Inventor functionality frequently on the Boeing project.”
Design, Test, Design
Valiant’s portable cargo loader design called for an easy-to-assemble clevis pin construction. Valiant engineers had to make sure that the clevis pin connections holding the cargo loader’s tubular truss structure together were strong enough and stresses appropriately dispersed. They also needed to minimize the structure’s weight.
For this, Valiant turned to Autodesk Algor Simulation software, which offers a suite of mechanical simulation tools.
“Our design called for eight telescopic hydraulic cylinders to lift 90,000 pounds each,” says Stein. “Using Inventor, we were able to package three-section telescopic cylinders in place of four-section cylinders, increasing load capacity while reducing cost. In an application with demanding clearance and structural requirements, we used Inventor Professional and Algor to develop a design that spreads significant loads to the upper truss structure. As a result, we had confidence at early stages of the project that our targets were achievable.”
In addition, its confidence in the Algor structural analysis allowed Valiant to reduce the wall thickness of the 6x6-in. steel tubing comprising the truss structure to 3/16 in.. Once the team put the material into Inventor, they checked the model proper- ties to calculate weight.
“We ended up below our weight requirement,” says Stein. “Thanks to the interoperability between Inventor and Algor, we could make incremental changes and quickly assess whether the design would still hold up. In general, conducting analysis in-house with Algor Simulation software helps us reduce errors and design time. We don’t have to wait for an expensive third party to test our designs for us.”
The Result
Valiant credits Autodesk Inventor software and Autodesk Algor Simulation software with helping it maintain its high levels of innovation. In fact, Valiant was the only company to define a plan to break the 114-ft. loader into two operational 50-ft. loaders, providing a competitive advantage.
Subscribe to our FREE magazine,
FREE email newsletters or both!About the Author

DE’s editors contribute news and new product announcements to Digital Engineering.
Press releases may be sent to them via [email protected].
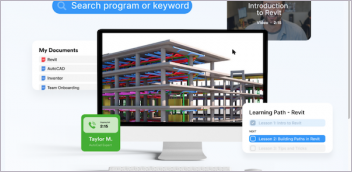

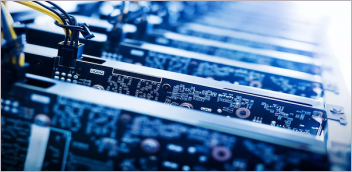
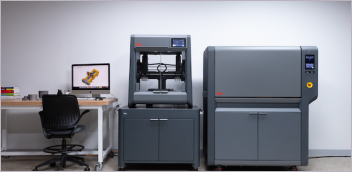