Latest News
November 1, 2009
By Christian Deville-Cavellin
In any industrial process, a key goal is to optimize speed. For Ugitech S.A., a manufacturer of stainless steel in France, that means running its continuous casting (concast) machines as fast as possible while maintaining quality. Yet, if you prematurely cut off pieces of the square bloom coming out of the casts, the inside of the steel section will not be completely solid, and a molten metal well, with as much as 1.5 tons of liquid steel, can empty into the bottom sections of the vertical concast machine, causing major damage. Through modeling, Ugitech is optimizing the temperatures and process speeds for each of the 150 grades of steel the company produces.
![]() Figure 1. In the casting process, liquid metal enters a water-cooled mold, where solidification occurs through convection and conduction. Once a solid shell (the skin) has developed, temperatures in the steel are initially reduced by a series of water sprays, and then further cooling is allowed to occur naturally through radiation. The length of the liquid well is critical to the point where the cast can be torch-cut. The temperature profile is also shown. | ![]() Figure 2. The model is used to examine the development of the air gap (left), the heat flux inside the bloom (middle), and the temperature in the bloom (right). The air gap not only affects the heat flux and cooling of the cast, which is to be expected, but also has a significant effect on the product surface quality. |
A Solidified Shell Forms First
In the company’s casting process, molten steel is poured into a tapered copper mold, and the steel is cooled by water circulating around the mold. During this stage, the steel develops a solid shell that can withstand the ferrostatic pressure of the molten metal well inside the strand. After it is removed from the mold, the steel is sprayed with water from three sources to increase the strength of the shell, and rollers prevent the steel from bulging. The strand is finally cooled through radiation (Figure 1).
Ugitech used modeling to examine early solidification, a phase when cracks, segregations near the product’s skin, depressions, and oscillation marks (the mold oscillates vertically to help the mold effect lubrication) can occur. As the shell cools, it shrinks, and an air gap forms at certain points (Figure 2). The gap’s location has a big impact on the final product, and controlling the gap’s formation is a delicate process. If the gap opens too early, insufficient heat is removed from the shell. The solid skin remains thin, and internal defects appear in the product. If the air gap is too thin, the mold becomes too conical, and friction occurs between the strand and the copper mold, which can cause the shell to break below the mold as a result of excessive friction during the extraction process.
Simulation is required to measure various mechanical components—such as the coil and magnet in the driver—and examine their condition. Because the components produce unidirectional movement, the panel on the other side of the gel can produce a complicated waveform, especially at high frequencies, consisting of movement that can lead to sound distortion and modal shapes that change with frequency.
Only through COMSOL Multiphysics modeling is it possible to understand what is happening inside the steel bloom as it passes through the concast machine. Using COMSOL’s Heat Transfer and Structural Mechanics Modules to compute the skin deformation during the solidification process, it took Ugitech engineers roughly 6 months to develop a model and verify it against experimental data.
Contact Conditions and Phase Changes
The model consists of two parts: a pure heat-transfer model that can predict temperatures and phases within the bloom and a thermomechanical model that helped the engineers better understand the mold/steel interface and gain more knowledge about defects on the bloom surface so that they could correct them (Figure 2).
Part of the challenge in setting up the model was the strong nonlinearity of the contact condition between the steel and the mold. In addition, because steel undergoes phase changes, the engineers had to obtain thermo-physical data about each grade of steel and include it in the models. For example, they could add a description of thermal conductivity to the modeling process, using a 3rd-order polynomial, based on years of experimental data. There was, however, one critical temperature range, where the engineers had to include a table of 40 to 100 data points and let COMSOL extrapolate between them.
Ugitech spent a great deal of time with the model, studying various cooling aspects, again to increase process speed without impacting product quality or to change the properties of the end product. This is a delicate matter, and the company didn’t want to experiment with its customers’ materials. In some markets, such as the automotive and nuclear industries, end users run their own trials and certifications on the steel. Thus, making a process change takes considerable thought and planning, and the model gave Ugitech a better understanding of the process and revealed possible outcomes.
With the model, the company was also able to assess modifications to the machinery. At one point, the production engineers asked the company to study the secondary cooling section, which they wanted to move a few centimeters to improve accessibility and facilitate maintenance. Even a small change can have a major impact on the process, and it’s not something you want to experiment with on such expensive equipment. With the model, the engineers were able to confirm that the process team could move the cooling section without incurring serious consequences.
In another case, the model helped avert a major problem. The production staff wanted to make a torch cut after they thought the 1 m security limit for solidification had been reached. The model showed this would actually result in a premature cut and open a molten metal well, with the catastrophic consequences. The engineers ran the simulation with COMSOL, and they were now able to readjust the security limits much more accurately (Figure 3).
![]() Figure 3. Torch cutting of the strand can take place only after the metal in the center of the bloom has solidified. |
Choosing COMSOL Multiphysics
Ugitech selected COMSOL Multiphysics after reviewing other simulation products and found that the software provides leading performance for a third of the price. The company already had specialized software for mechanical engineering, so proponents of COMSOL’s software had to convince management that the product would be a good investment for a multiphysics tool. The engineers wanted a general-purpose package that they could apply to a variety of problems. The initial project involved defining the temperature profile of a moving wire inside a heated tube. Using COMSOL Multiphysics, they created the profile and were able to convince management that they could perform this type of modeling easily and quickly.
In the mean time, the engineers have found new ways of implementing and solving problems with the package, primarily because of its ability to add any physics to the models. With this approach, the engineers have become more productive than they would be with any other simulation software. The first results have given the company’s process engineers new ideas, and at the same time, they have raised new questions. In the end, COMSOL Multiphysics has encouraged the engineers to imagine new ways of solving problems.
More and more people at Ugitech are considering the benefits of increasing their simulation effort. People have stopped asking: “Can you calculate that?” Instead, the want to know: “What happens when… or if…?” Ugitech has also found COMSOL Multiphysics useful in communicating ideas and concepts to its customers.
Subscribe to our FREE magazine,
FREE email newsletters or both!Latest News
About the Author

DE’s editors contribute news and new product announcements to Digital Engineering.
Press releases may be sent to them via [email protected].
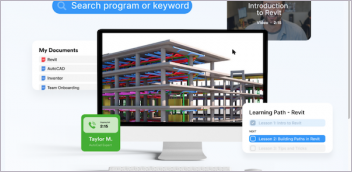

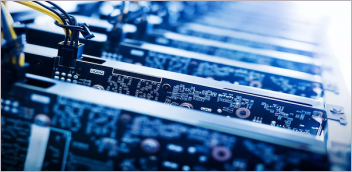
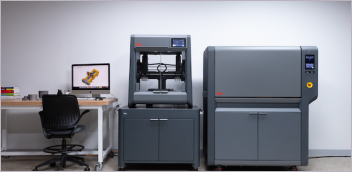