Latest News
February 14, 2013
![]() |
The type of work that Stapf targeted “advanced simulations in CAD and computational fluid dynamics (CFD) “demanded robust, cost-effective engineering tools. Fortunately, Stapf’s engineering history had exposed him to commercial analysis systems.
“I was familiar with all of the world-class FEA (finite element analysis) packages, having used them throughout my career,” Stapf recalls. “However, for my consulting company, I conducted a cost-benefit analysis. I needed analysis power and speed at the most attractive price.”
Stapf chose SolidWorks Simulation Premium software as SE Corp.’s analysis package because of its CAD integration, extensive set of capabilities, and fast solvers. “I selected SolidWorks Simulation Premium and SolidWorks Flow Simulation software because they provide structural, thermal, and computational fluid dynamics (CFD) analysis tools within the SolidWorks parametric modeling environment,” Stapf says. “It has three to four times the capabilities of other packages and can run my simulations two to three times faster, at half the price.”
Integrated CFD tools were also important. “Some of the features that stood out were the ability to work with parametric solids inside the CFD domain, tools for improving the analysis mesh through the use of smart elements, and being able to run grid-independent calculations,” Stapf explains. “These features remove the barriers between the engineer and the physics. With SolidWorks Flow Simulation, I can do within minutes what others may spend days or weeks refining.
Space Flight: The Next Chapter
SE Corp. found the type of challenge it was seeking when it undertook a flow simulation of the Vehicle Assembly Building (VAB) at NASA’s Kennedy Space Center in 2010 for Science Applications International Corp. (SAIC), on a NASA project. NASA needed to assess potential uses for the VAB, where all of the shuttles were prepped for launch. NASA specifically wanted to evaluate facility safety and emergency escape procedures in the event of a rocket fuel ignition accident to determine whether the VAB would remain viable for future projects.
SE Corp. modeled a broad array of VAB configurations, including those with the massive 480-ft.-tall vehicle doors opened and closed, and with the incident occurring in any of the VAB’s four work bays. Using SolidWorks Flow Simulation, Stapf simulated how thousands of feet of high-temperature exhaust gases from the ignition and subsequent explosion would be driven throughout the VAB at hundreds of feet per second.
![]() |
“The CFD model predicted where and when these exhaust gases would become lethal in and around the VAB,” Stapf notes. “By quantifying the time and severity of structural and personnel exposures to exhaust temperature, velocity, pressure and concentration, NASA could improve safety and emergency response planning.”
Fast Solution Aids Safe Facility Reuse
Using SolidWorks Flow Simulation, SE Corp. quickly simulated the behavior of exhaust gases and ground-level thermal radiation. The study also examined the effects of the sea breeze coming off the Atlantic Ocean. With this study, NASA was able to identify the operational bays with the greatest potential hazards, calculate personnel egress times during an incident, and establish distances from the VAB at which personnel would be safe.
![]() |
“I was able to turn the CFD solution around in 24 hours,” Stapf says. “Although the model and mesh were large “roughly 200,000 elements “I was able to accelerate solution time by using smart elements. The model would have required millions of elements and a month of solution time in another CFD package. With SolidWorks Flow Simulation software, I was able to produce grid-independent solutions and report multiple flow gradients with high fidelity and detail in a single day.”
NASA Honors
In recognition of SE Corp.’s contribution, NASA recognized the project with its Space Flight Awareness Team Award. The award specifically cites the team “for significant contributions in the implementation of a Maximum Credible Event safe siting approach, allowing NASA a cost avoidance and continued use of the John F. Kennedy Space Center Vehicle Assembly Building for future programs.”
“It was an honor to receive this award, perform this work, and know that the VAB will continue to contribute to the U.S. space program for another 50 years,” Stapf says. “I’m more than satisfied with SolidWorks simulation solutions, and glad that my customers are happy with my work.”
Info
Subscribe to our FREE magazine,
FREE email newsletters or both!Latest News
About the Author

DE’s editors contribute news and new product announcements to Digital Engineering.
Press releases may be sent to them via [email protected].
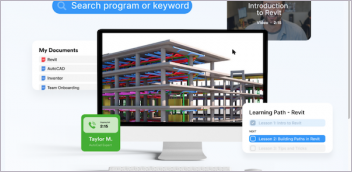

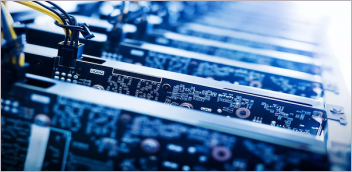
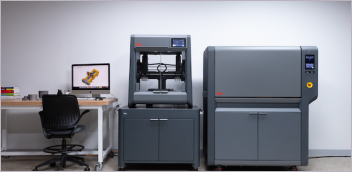