
Latest News
January 15, 2014
Ask a kid whether they like trampolines, and their eyes are sure to light up with joy. But ask some parents, and you may get an entirely different response. Despite tightened manufacturing standards, covered springs and frames, and safety net enclosures, approximately 90,000 children are still injured on traditional trampolines every year in the United States alone.
![]() Fig. 1 A Springfree trampoline is put to the test by an enthusiastic user. |
Trampolining has been part of the Olympic Games since 2000. But while professional-caliber trampolines are used to train gymnasts, divers, astronauts and ski jumpers, the backyard athlete—often a child—is no expert in the sport. Recreational trampoline equipment has traditionally been less robust than what the pros use. As a result, home versions are more susceptible to accidents and injuries than the professional ones.
How can the fun go wrong? In a number of ways, thanks to the unavoidable laws of physics. The elasticity that provides a traditional trampoline’s exciting bounce comes from metal springs that connect the mat to the frame. The springs store potential energy when the mat is compressed by the person’s weight, releasing that energy back to thrust the fabric upward and the bouncer high into the air. A jumper who lands off-center may be projected sideways and can miss the mat, hit the rim or springs, or fall through the gap between them. Even if there’s safety netting, it’s often connected to hard metal support bars or is strung too loosely to control a hurtling body. Both netting and mat stitching may be weakened by exposure to sunlight.
In the late 1980s, Keith Alexander, Ph.D., an associate professor of engineering at New Zealand’s Canterbury University, was certain there had to be a safer way to enjoy the trampoline.
“I always believed that, as an engineer, I should be doing things that benefit people,” he says. When his wife nixed his plans to buy a conventional trampoline for their daughter Katie, out of safety concerns, he decided to build a better one. He began by working in his garage and later moving his research to the university—where help from his students (plus government and private grants) kept the momentum going.
Analyzing reams of data about the classic trampoline design, which dated to the 1930s, Alexander determined that there were three main impact zones that needed to be arranged so the user wouldn’t impact them: the springs connecting the bounce mat to the frame, the metal frame itself and, of course, the ground.
Many prototypes later, Alexander arrived at his final, innovative solution: Move the frame below the jumping surface, create a soft edge to the mat, and surround the whole thing with tensioned, ultraviolet-resistant netting that would bounce users back toward the center if they went off-kilter. The result was the Springfree Trampoline (see Fig. 1), first produced in 2003 and currently selling at a rate of about 40,000 per year around the globe.
Of course, the human element applies to any sport: If trampoliners jump in groups (“not recommended,” says Alexander), they can crash into one another. Even solo enthusiasts can twist a limb if they land wrong on the mat. But the Springfree has proven itself significantly safer than traditional trampolines. Several studies have supported the goal of Alexander’s efforts, demonstrating a reduction in equipment-related injuries of between 30% and 80% on his products.
The health benefits of jumping have also been documented. Ten minutes on any trampoline is equivalent to a 30-minute run, according to the SpringfreeTrampoline.com, which notes that “NASA has determined that jumping is 68% more efficient than running in terms of aerobic benefits. It’s a moderate-to-high-level workout that’s low in impact.” The mat absorbs up to 80% of the vertical acceleration and deceleration of jumping, while still providing a landing that’s four to five times the force of gravity, which promotes muscle and bone strength.
More than Meets the Eye
If trampolines are your thing, the Springfree would certainly make a safer, healthy, eye-catching addition to the back yard. Yet it’s what you don’t see that’s so unusual. That would be the high-tech cleats under the mat’s edge—60 or more per trampoline, depending on the model. Made from fiberglass-reinforced polypropylene and shaped like a wide letter “T,” these cleats have a rounded, midline socket into which the balled top of each fiberglass support rod fits (see Fig. 2). The lower ends of the rods connect to the metal base of the trampoline.
![]() Fig. 2. This close-up of the support structure of a Springfree trampoline shows how white rods connect via cleats to the upper, soft-edged jumping surface. The lower end of the rods attach to the secure metal frame that sits on the ground. (Protective netting not shown.) |
“The plastic edge fitting of my design had always been the most complicated bit of the eight or nine different versions I came up with,” admits Alexander. The cleat, which is inserted into a reinforced pocket in the mat, harnesses the downward tension of each jump this ensures that the ball at the top of the rod stays wedged into the socket as it moves up and down.
Once the Springfree was commercialized, word about its benefits began to spread. Parent- and safety-association awards followed. Sales bounced upward, and production swung into high gear. The company’s New Zealand-based injection molding supplier, Action Plastics, was kept busy manufacturing cleats at a rate that has now reached approximately 2.5 million units per year.
As the molding tool used to manufacture the cleat drew near the end of its lifetime in 2013, “we had some pretty significant inducements to build a new tool, and we realized it was a great time to look at optimizing and improving the cleat component,” says Hamish McIntyre, engineering manager at Springfree New Zealand Ltd. “Because the cleat was so complex in terms of loading and mechanical properties, we decided we needed an engineering consultant to help us out. We located Matrix Applied Computing, through a Ministry of Science and Innovation expert search program, and selected them based on their advanced capabilities.”
Of particular interest to McIntyre was Matrix’s familiarity with realistic simulation using Abaqus finite element analysis (FEA) software from SIMULIA, the Dassault Systemes’ 3DEXPERIENCE application. “I had worked closely with FEA teams at Airbus in the U.K. and knew how powerful Abaqus was,” he recalls. “The fact that Matrix used Abaqus was one of the things that drew me to them because I’d seen the software in action on advanced aircraft design.”
As Guido Quesada, CAE Design Engineer at Matrix, explains, “We were already familiar with Springfree trampolines and knew it was a very technical product. Sometimes a potential customer calls with some funny toy or crazy idea that’s hard to take seriously. This was definitely not the case with Springfree. From the start, we knew we had a significant challenge with this cleat design project.”
No Agony in the Cleat
There were two main drivers of the challenge, according to McIntyre: “We wanted to improve the strength, the ultimate load capability, of the cleat. And we didn’t want to introduce significant additional cost into the component. The quantity we buy each year is expanding along with our sales growth. Just a couple cents less for materials per cleat ends up as a significant cost savings. We saw this as an opportunity to tweak the component and get the most out of it.”
![]() |
![]() |
Fig. 3. Laboratory testing measured the forces resulting from the interaction of rod ball, left, and cleat, right. |
And so the tweaking began, starting with some good old-fashioned field research. Both Matrix principal engineering analyst Don Campbell and Quesada took informal walks around their neighborhoods, watching people jumping on Springfree trampolines in order to visualize what was happening to the cleats as the mats went up and down and the rods bent in tandem.
Then it was back into the physical testing lab, where a device was built to apply the load from a rod to the center of a cleat, supporting it at the sides like the socket would (see Fig. 3). SolidWorks (also from Dassault Systemes) CAD models were made of the rod and cleat components, set up in the testing apparatus. The CAD models were meshed with Abaqus FEA, and data captured through the physical tests served as input for the computer simulations (see Fig. 4) that predicted how changes in cleat geometry would affect strength and durability.
![]() Fig. 4. Abaqus FEA analysis of rod ball movement within cleat socket. |
“Right from the outset, we worked closely with our moldmaker to ensure that what we came up with was manufacturable,” says McIntyre, referring to Sean Dryer of Action Plastics. Matrix imported Moldflow software results into its Abaqus models to incorporate the effects of the orientation of the glass fibers in the cleat. The material is stronger in the direction that most fibers lie, so the fibers need to be aligned as much as possible with the most critical stresses. Also important was to take into account the residual stress from the manufacturing process itself—mainly, the result of the surface of the cleat part cooling faster than the core.
As subsequent design options were proposed and evaluated, “one of the most significant challenges was not what Springfree was asking of us, but the manufacturing constraints we had on what changes we could make to the part,” says Quesada.
Matrix focused on identifying the optimal geometry for the new cleat design, and it considered a variety of analytical pathways before arriving at a workflow that would move things more quickly through the optimization process. Using Abaqus to help understand the nonlinear interplay among structure, material, loading and stress, the team was ultimately able to create simplified analogies that established an accurate relationship among geometric changes, stiffness and strength through fundamental deformation modes such as bending and twisting.
“Of course, different sizes and abilities of trampoline users would produce different load levels,” says Quesada. “SIMULIA’s solutions were particularly helpful in providing us with a nonlinear simulation framework so we could create a very realistic representation of the most important load conditions. Abaqus/CAE just made things better by providing an excellent graphical environment for all our needs, enabling edits and tweaks to the input files whenever necessary. This builds a lot of confidence when using the tool. It helped us come up with the most cost-efficient way to provide the best possible answer to our customer in terms of a good design.”
“Before we worked with Matrix to use realistic simulation, it was very much a trial-and-error process based almost solely on geometry, manufacturability and physical prototyping, which involved a huge turnaround time,” says McIntyre. “Compared to what we did before, I would say we are now light years ahead of where we were.”
![]() |
Fig. 5. Abaqus FEA model of cleat optimized “by hand” shows the two ribs that were regarded as most effective. This version is now in production on new Springfree trampolines.
The final cleat design the team arrived at uses slightly less material overall and has two ribs added on one side, to provide extra support where needed and to distribute stresses more evenly (see Fig. 5). It’s now appearing in new Springfree trampolines worldwide.
A Closer Look
After the redesign project was complete, Quesada took a further look at the final cleat geometry using SIMULIA’s Abaqus Topology Optimization Modeling (ATOM) tool, which automatically finds the optimum configuration (weight as well as shape) of a component while confirming performance with FEA to ensure strength and durability targets are met.
![]() Fig. 6. Abaqus FEA model of a cleat optimized using Abaqus Topology Optimization Module (ATOM) identified a third possible rib that could provide optimum support to the component. |
“Our previous workflow—involving detailed CAD modeling, mold simulations, nonlinear simulation and simplified modal analysis—was ultimately highly successful,” he says. “But when we applied ATOM to the same design, the process became much faster and effective, with automatic exploration of the optimal geometry. I was very surprised to see that ATOM helped spot features I didn’t think of, including a third rib. It also saved us a lot of CAD work, since the ATOM procedure uses the same reference geometry during each optimization round.”
He shared his new insights with Springfree; with the two-rib version already in production, a new, four-rib design, which enhances the automated optimization by putting in additional engineering and design judgment, is being considered for the next generation of trampolines (see Fig. 6).
A “next generation” is probably inevitable, given that Springfree inventor Alexander still has a few trampolines sitting in his back yard, “possibly waiting for grandchildren.” All three of his kids are out of the house and his daughter Katie, for whom he designed the original, is now married.
![]() |
Fig. 7. Abaqus FEA model of a final cleat design featuring a fourth rib introduces more symmetry and improved robustness in twisting and sideways bending modes, in addition to the main bending mode.
The main patent on the Springfree was owned by the university and sold to Springfree in 2002. Although Alexander has no ownership at this point, he maintains a close working relationship with the company.
“I love my job at University, and the ongoing involvement with Springfree has had spinoffs all round—research papers, student projects and a great story to tell,” he concludes.
More Info
For more information on this topic, visit deskeng.com.
Subscribe to our FREE magazine,
FREE email newsletters or both!Latest News
About the Author

DE’s editors contribute news and new product announcements to Digital Engineering.
Press releases may be sent to them via [email protected].
Related Topics
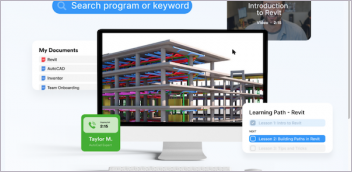

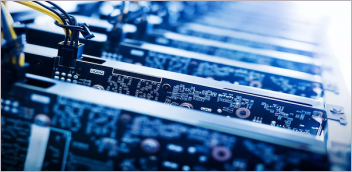
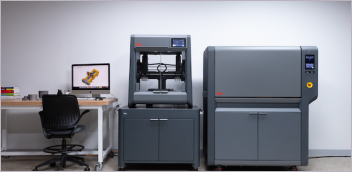