Fast App: Building Better Bits with Mentor Graphics
CAD-embedded CFD helps Encore Bits LLC optimize its product designs and compete with larger oilfield drill bit manufacturers.
Latest News
December 2, 2009
By Nazita Saye, Mechanical Analysis Division, Mentor Graphics Corp.
The performance of an oilfield drill bit depends heavily on the flow of the drilling mud through the bit. One of the toughest challenges is avoiding high-velocity flows in crucial areas while ensuring the proper flow for cuttings removal and cooling. Major oilfield bit producers, such as Baker Hughes and Halliburton, use highly trained experts, who perform computational fluid dynamics (CFD) simulations of drill bits to evaluate alternative designs to improve performance. Smaller drill bit manufacturers find it is not cost-effective to keep these highly paid specialists on staff, so generally, they offer a nonoptimized product at a lower cost.
![]() Figure 1. Erosion can be seen on blade 5. |
Encore Bits LLC is a relatively small drill bit manufacturer that has used advances in CFD technology to provide optimized products without the help of costly dedicated experts. The company uses a new generation of CFD software embedded in CAD software. With the software, design engineers can optimize the fluid flow characteristics of each polycrystalline diamond compact (PDC) bit prototype during the design phase. Using this approach, the time and cost required to perform CFD simulation are much lower than when conventional CFD tools are used.
For example, it took Vince Salvo, Design Engineer for Encore, only one day to optimize the design of the company’s F-5165D bit. The CFD simulation identified high-flow areas near one blade that would have reduced the life of the bit. Salvo made changes in the component’s geometry and nozzle configuration that substantially increased its life and enhanced cuttings removal.
Encore provides standard oilfield PDC drill bits from 4 to 24 inches, as well as custom diameters for less common casing diameters and special projects. The company’s designs include gumbo-drilling fishtail designs for the Gulf of Mexico and ultra-tough bits designed to drill in the abrasive sandstones and dolomites of the Middle East. Encore has an extensive R&D program to take advantage of new materials and technologies.
![]() Figure 2. FloEFD.Pro shows the areas most likely to experience erosion. |
Designs for Drilling Challenges
The rock formations in the largely depleted reservoirs of the Permian Basin have chert and pyrite nodules and sometimes require the use of high-solids content drilling muds, all of which makes for a tough working environment for both the cutters and bit body. The preferred bit for this type of drilling has historically been the roller cone bit. The advantage of its relatively low cost, however, is offset by the number of bits required to finish drilling a well section.
Encore developed the F5165D to provide a bit that can handle the drilling of an entire section and be rebuilt several times to reduce its own costs and those of the operator. Because of these advantages, this model has become one of the company’s most popular bits. Early versions, however, showed erosion after only one or two runs (Figure 1). Encore sets its rental rates based on the assumption that it will be able to rebuild the bits. Severe erosion negatively affects the company’s ability to rebuild a bit, reducing its profit margin.
The drilling process provides no way to identify the flow pattern that causes this problem. Large drill bit producers use traditional CFD codes that cost approximately $25,000 a year to lease. An even greater expense for most companies is the need to hire experts to run the codes. In the past, analytical experts were required for all CFD codes, and they are still necessary for most CFD tools because users must know how to translate the CAD model into the CFD environment and then reverse the model so that empty flow space rather than the solid product is modeled. Users must also be able to create a mesh with the correct properties, determine boundary conditions, select the right physical models, and tweak solver settings to ensure convergence, as well as other tasks.
New Software Helps Analyze Flow
In the past few years, a new generation of CFD software has been introduced that addresses all the major reasons for the relative lack of use of CFD software. Its use of native 3D CAD data, automatic gridding of the flow space, and managing flow parameters as object-based features helps eliminate the need for engineers to understand the computational part of CFD. Instead, the software enables them to focus on the fluid dynamics of the product, which is already their responsibility to understand and master. To operate the CFD software, the engineer must simply understand the CAD system and the physics of the product, which most design engineers can certainly do. Thus, the engineer can focus time and attention on optimizing the performance of the product, as opposed to operating the software.
![]() Figure 3. Flow analysis of the final design shows that the high flow velocities that caused erosion in the original design have been eliminated. |
Salvo started with a Pro/ENGINEER solid model of the 8.75 inch diameter matrix drill. He then modeled the bottom hole pattern of the bit, which is the shape the component cuts into rock, and combined the two models with interference. The resulting model depicts the open area below and around the bit, where fluid is free to flow. Salvo used Mentor Graphics’ FloEFD.Pro software, which is embedded in Pro/ENGINEER. He defined the boundary conditions right on the solid model—9 pounds per gallon of water-based drilling mud going down through five nozzles in the bit and static pressure coming up through the junk slots around the outer edges of the bit.
Simulation Identifies the Cause of Erosion
Salvo ran the flow analysis, and Pro/ENGINEER presented the results. The colored lines in Figure 2 show the flow velocity in various areas of the bit, and the scale on the lower left side of the image shows that yellow, orange, and red lines indicate the fastest flow. The simulation shows the area where the erosion occurs on blade 5, which experiences a flow rate of between 1600 and 1800 inches per second, or nearly 100 mph. The speed combined with the presence of abrasive particles in the mud is sufficient to quickly erode even a tough material like tungsten carbide. The flow is directed around the interface, between the bit and blade, where it can wear away the backing for the blade and make it impossible to rebuild.
From the simulation results, Salvo gained an understanding of the problem and almost immediately developed ideas of how to improve the flow performance of the design. He tried several ideas, singly and in combination, by first modifying the design in the familiar Pro/ENGINEER CAD environment and then by simply pushing a button to re-run the embedded CFD simulation. With each design iteration, he gained additional insight, which produced steady improvements. As he evaluated each design, Salvo was careful to avoid generating excessive velocities in other critical areas. He also worked on increasing flow velocity through the junk slots, an area where high velocity is beneficial because it removes cuttings more efficiently, making it possible to increase the penetration rate.
A Better-Performing Bit
The highly competitive nature of drill bit manufacturing makes it impossible for Salvo to detail the changes he made to achieve the final design. But he summarized the project as follows: “By altering the nozzle configuration and the blade shapes, we were able to achieve lower fluid velocities in critical positions while maintaining and somewhat increasing velocities in junk slot areas. These changes resulted in a bit that has better cleaning and cooling ability while also improving the wear characteristics (Figure 3). Decreasing erosion also helps us prolong the life of the bit, giving us better profitability over the product lifecycle. This project clearly demonstrates that FloEFD.Pro offers the potential for huge advancements to companies whose products involve fluid flow. It gives design engineers the ability to easily and accurately analyze fluid flow, which in turn frequently enables substantial improvements in product performance.”
Subscribe to our FREE magazine,
FREE email newsletters or both!Latest News
About the Author

DE’s editors contribute news and new product announcements to Digital Engineering.
Press releases may be sent to them via [email protected].
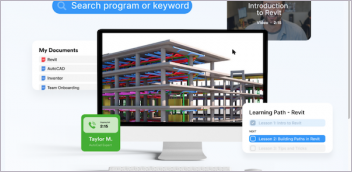

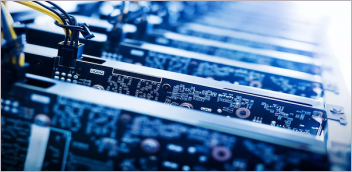
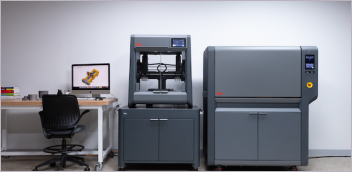