Latest News
January 1, 2010
By DE Editors
After three decades of dormancy, nuclear power plant design and construction is undergoing a resurgence in the U.S. The renaissance has been marked by a wave of companies looking to use the latest engineering IT systems to create a new generation of nuclear reactors that will be easier to build and more efficient to operate (Figure 1).
![]() Figure 1. With the resurgence of nuclear power plant design and construction in the U.S., AREVA needed to develop an IT foundation that would enable it to play a leading role in future projects. With the help of AVEVA and its Plant suite of integrated engineering applications, AREVA was able to design, fabricate, and revamp facilities of any size or complexity, with reduced development cycles and lower costs. (Courtesy of AVEVA.) |
“Nuclear power promises to energize electricity generation worldwide and help address concerns about greenhouse gas emissions,” offers James A. Lake, Associate Laboratory Director for the nuclear program at the Idaho National Laboratory and former president of the American Nuclear Society. “In the long term, nuclear energy could become… more economical, proliferation resistant, and sustainable.”
Such attitudes among industry insiders have burgeoned since the U.S. National Energy Policy of 2001 proposed initiatives to make nuclear power more competitive. Indeed, according to The New York Times, 21 companies have approached the Nuclear Regulatory Commission (NRC), seeking permission to build 34 power plants, from New York to Texas.
Among the companies involved in the new plant construction is AREVA, one of the world’s largest builders of nuclear power plants, with manufacturing facilities in 43 countries and a sales network in more than 100. For many years, the company has been offering customers reliable technological solutions for carbon dioxide–free electricity generation across the world and is perhaps the only company to cover all industrial activities in the nuclear industry. AREVA is undoubtedly a world leader in nuclear power, and having set a goal of strengthening its international presence, the company—just as the industry itself—is in the midst of a rapid expansion.
AREVA submitted its EPR reactor design to the NRC for certification. The EPR is a generation III+ evolutionary pressurized water reactor. One of the first EPR reactors in the U.S. is likely to be the Calvert Cliffs 3 plant, which is scheduled to be constructed adjacent to the Calvert Cliffs Nuclear Power Plant Units 1 and 2, in Lusby, MD. Calvert Cliffs 3 is one of four combined construction and operation applications currently under review by the NRC that would have AREVA and its partners constructing new nuclear power reactors at sites across the U.S.
The Challenge
Despite the renaissance in nuclear power in the U.S., a key industry challenge remains. After two decades of inactivity, the ramp-up to planning and building new nuclear power plants is incredibly steep. AREVA needed partners to help it navigate this challenge, and in the area of engineering IT, that partner is AVEVA. With AVEVA’s customizable toolkit, AREVA will maximize the productivity of limited resources and make the most of this opportunity in a timely manner.
Rapid expansion into a new market required AREVA to overhaul its engineering IT systems, in essence reinventing them for its accelerated growth. AREVA looked to AVEVA to help build a sound IT foundation for future projects. AVEVA has a long history of leadership in the worldwide energy industry, and the two companies had already enjoyed a close and fruitful relationship in Europe, making the decision to use the AVEVA toolkit for AREVA’s planned American operations all the more easy. AVEVA stands ready to assist with technical products that span all phases of the plant lifecycle, from design to operation. As AREVA builds nuclear facilities across the country in the years to come, AVEVA will be there with ongoing support, expertise, and experience.
The Solution
To rapidly implement the myriad systems for the EPR projects, AVEVA leveraged its long history in engineering IT, across the worldwide energy industry. The company turned to its comprehensive toolkit of IT systems, helping AREVA ramp up its American engineering operation in record time.
AVEVA helped AREVA adapt its European design to meet U.S. requirements. Beyond this initial step, AVEVA engineers will support AREVA personnel and the company’s project partners on an ongoing basis, as new nuclear power plants move from design to construction across the U.S.
“AREVA was impressed with our vision for the future of nuclear plant design,” says Bob Duncan, Strategic Accounts Director at AVEVA. “They engaged us because they believe in both our suite of products and our product technology roadmap for the future. This includes engineering design, materials management, and construction.”
AREVA now uses products from AVEVA’s Plant suite, a set of integrated applications that enable the engineering, design, fabrication, and revamping of plants of any size and complexity. These software tools promote efficient project workflows, consistent change management, error-free results, and reduced development cycles and costs.
AREVA primarily relies on seven of the suite’s applications. Each provides a wide range of functionality, as described below.
![]() Figure 2. AVEVA VPE P&ID stores engineering data onto graphical entities in AutoCAD drawings. The application has a standard AutoCAD interface that ensures ease of use. (Courtesy of AVEVA.) |
• AVEVA VPE P&ID. This design system stores engineering data onto graphical entities in AutoCAD drawings while the designer draws and annotates the piping and instrumentation diagrams (P&IDs). The P&IDs contain tagged items, quantities, and connectivity data, which can be loaded into an AVEVA schematic model via AVEVA P&ID Manager or synchronized with an AVEVA VPE database for the production of project reports and datasheets (Figure 2).
• AVEVA VPE. This scalable Oracle database application holds and manages the evolving engineering definitions and interconnections of all tagged items in a plant design, such as lines, valves, vessels, instruments, equipment, electric motors, junction boxes, and MCCs. Engineering data and properties are maintained and handled within a completely integrated database schema.
![]() Figure 3. The AVEVA Model Management application streamlines data preparation, control, and management of 3D objects found in complex plant models. It allows designers to manage work allocation of all plant items throughout the project lifecycle. (Courtesy of AVEVA.) |
The software manages not only the quality and consistency of engineering information, but also its interdisciplinary flow within the application and its availability to external systems. Powerful workflow management controls data through each stage of the project’s development. A flexible, item-based lifecycle controls the visibility of released information among departments and can be customized for specific project needs. Data changes between versions are highlighted.
• AVEVA VPRM. This integrated resource management software helps manage risk, reduce costs, and provide project control throughout the life of a project. The application helps manage projects by providing full visibility of progress and controlling access to project data. It manages change through reports that track modifications and email that automatically notifies the appropriate people of developments.
VPRM also helps to manage materials throughout the supply chain with controlled releases that ensure correct procurement and accurate material take-off forecasts that allow early order placement and quantity adjustments as projects progress. The software continuously tracks deliveries, putting site managers in full control of the day-by-day construction process. The application helps users achieve significant cost savings by minimizing surplus materials and subcontractor claims.
• AVEVA PDMS. This Plant Design Management System is a multidisciplinary design environment for 3D modeling of plants. The software includes modules that enable the design of equipment, piping, HVAC, structure, and cable trays. The modeling is carried out in a 3D environment, with tools that ensure a fully connected, intelligent, data-centric, change-managed, and error- and clash-free design. A full range of drawings and pipe isometrics can be produced automatically from models created in this system.
• AVEVA Global. This application allows users at multiple sites to work together online on the same project. It controls the release of data to each site and ensures that all sites and users have access to the latest approved data, right down to attribute detail. Global operates across low bandwidths and is tolerant of communication faults. The software enables distributed design teams to share controlled design information among offices, subcontractors, vendors, and partners. It combines concurrent 3D design with central administration and control, flexibility, and high performance.
• AVEVA Model Management. These powerful model management tools help design teams maximize the productivity of all members and achieve a high level of quality in their work (Figure 3). The application streamlines data preparation, control, and management of 3D plant objects and deliverables. The tool set allows the team to manage work allocation of all plant items throughout the project lifecycle, maintain consistency among P&ID and 3D plant models, and report on the progress, status, and attributes of plant objects in PDMS. It also enables designers to populate 3D PDMS models directly from P&ID data and achieve comprehensive clash management and resolution.
Perhaps the greatest benefit derived from using this application is the time it saves at many levels of the design process. Overall, the model management tools reduce the amount of rework that must be done. Manual design checking is replaced with strict workflows and verification processes, minimizing sources of error. The software reduces design time by providing an environment that highlights and manages inconsistencies among P&ID and 3D model data. Because the tools ensure the quality of the design data, they increase the scope of parallel work processes and thus reduce design time.
• AVEVA Multi-Discipline Supports (MDS). This application enables the detailed design, material take off, and automated drawing of all kinds of supports for piping, ducting, and cable trays, from a complicated framework to a simple u-bolt. Design rules ensure that only appropriate supports are applied to pipes. Because MDS is catalog-driven, it automatically models supports and creates the necessary components. The software supplies a wide range of predefined supports, and specials can easily be created when necessary. Each support is created as a fully detailed part of the 3D model, visible to all disciplines. It can be included in layout drawings, visualizations, and weight calculations. MDS includes a comprehensive range of standards (Figure 4).
![]() Figure 4. The Mulit-Discipline Supports application enables automated drawing of all types of supports for piping, ducting, and cable trays. The software’s design rules ensure that only appropriate supports are applied to pipes. (Courtesy of AVEVA.) |
“AVEVA’s comprehensive toolkit gives us a breadth of offerings unique to the marketplace,” says Jim Newman, Supervisor of Design Engineering at AREVA. “Our ability to implement all facets of plant design and engineering within a single, integrated technology environment means there’s less chance of errors. Plus, the fact that AVEVA’s software engineering IT tools are highly interoperable simplifies our efforts to bring other companies to the table as our design and construction operations progress.”
The Result
AVEVA helped AREVA establish a new IT infrastructure, which is now being expanded globally into a next-generation toolkit for the nuclear industry. “When AREVA asked for assistance from AVEVA, we were there to help them meet what other companies would have found to be challenging deadlines,” says Duncan.
As recently as October 2008, AREVA and its AEC partner in the U.S. were awarded a major contract from UniStar Nuclear that moved the Calvert Cliffs 3 EPR reactor nearer to construction. AVEVA has been instrumental in assisting AREVA with the NRC’s design certification process, which will allow AREVA and its partners to build nuclear power plants at sites across the country. With its strategic relationship with AVEVA, AREVA is well on its way to playing a lead role in America’s nuclear renaissance.
Subscribe to our FREE magazine,
FREE email newsletters or both!Latest News
About the Author

DE’s editors contribute news and new product announcements to Digital Engineering.
Press releases may be sent to them via [email protected].
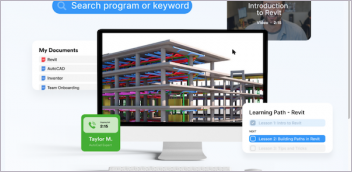

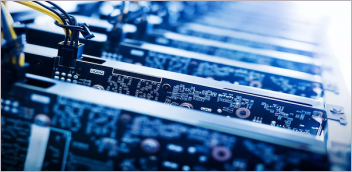
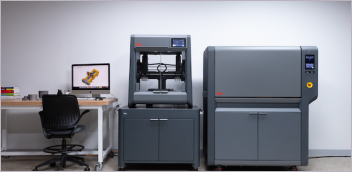