Fabrisonic Produces Industrial 3D Printing Systems

Fabrisonic’s SonicLayer 7200 AM system. Courtesy of Fabrisonic.
Latest News
June 27, 2012
The additive manufacturing (AM) landscape is chock full of different systems and processes for the creation of 3D printed objects. Some of these systems lend themselves more readily to direct industrial usage than others. This can be a result of the potential size of the build envelope available or materials used. Even large-scale rapid prototyping can only be accomplished by a handful of systems, unless the operator is willing and able to assemble smaller parts into a larger whole.
Fabrisonic is creating AM systems that are capable of operating on a large scale. The company was founded in 2011 as a joint venture between EWI and Solidica as a means of moving forward with the ultrasonic additive manufacturing (UAM) process — originally dubbed ultrasonic consolidation — developed by Solidica.
UAM is a sheet lamination process that builds objects using ultrasonically welded metallic tape, combined with more standard machining. Unlike other metal AM systems, ultrasonic welding doesn’t melt the metal used in the process. The following description of the technology appears on Fabrisonic’s website:
The process of ultrasonic metal welding is one in which ultrasonic vibrations create a friction like relative motion between two surfaces that are held together under pressure. This action, in turn, causes shearing and plastic deformation between asperities of the opposing surfaces, which disperses surface oxides and contaminants. As the asperities collapse, metal-to-metal contact is increased creating solid state bonding between the parts through heat and pressure.
According to the company, this solid state AM process allows for welding of dissimilar metals. Along with the usual benefits of AM (objects with complex internal geometries), the process allows for dissimilar metal cladding, the creation of custom metal matrix composites and the potential to embed objects (including sensors) in a metal substrate.
Fabrisonic currently offers three different UAM systems. The SonicLayer R200 has been developed for use by universities, R&D departments and small businesses, and offers a build envelope of 20 x 12 x 6 in. (508 x 304.8 x 152.4 mm). The “mid-sized” industrial SonicLayer 4000 offers a build envelope of 40 x 40 x 24 in. (1016 x 1016 x 609.6 mm). The final (and largest) available industrial system offered by the company is the SonicLayer 7200 with a build envelope of 72 x 72 x 36 in. (1828.8 x 1828.8 x 914.4 mm).
Both the 4000 and the 7200 include integrated 3-axis CNC machining, and, according to Fabrisonic, the 7200 can build at the rate of up to 60 in3/hour. Both of the above systems have automated tape feeding systems, while the R200 requires manual feeding. Applications for the technology include EDM replacement, conformal cooling, die casting tools, mold for vacuum forming and investment casting tooling.
Below you’ll find a video demonstrating the UAM technology.
Source: Fabrisonic
Subscribe to our FREE magazine,
FREE email newsletters or both!Latest News
About the Author
John NewmanJohn Newman is a Digital Engineering contributor who focuses on 3D printing. Contact him via [email protected] and read his posts on Rapid Ready Technology.
Follow DE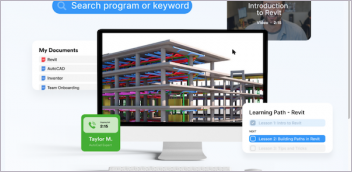

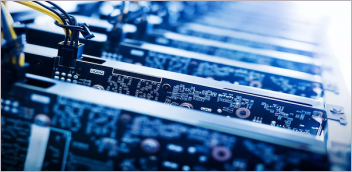
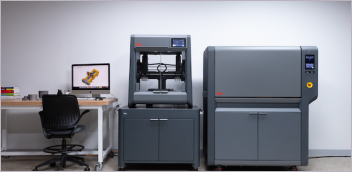