Latest News
September 17, 2010
By DE Editors
The latest release of EZ-CAM, version 18, delivers a new curve machining wizard, high-speed machining strategies and new features, such as pencil milling, added to the 3D machining wizard.
The new curve machining wizard automates the machining of common part features by applying multiple predefined worksteps to an active curve. Users can define their own feature categories, for example holes, pockets, or profiles, and corresponding machining methods to machine specific configurations.
A new Smooth HSM option, available in the Constant Z, Pocket and Zigzag cycles, generates a smooth roughing toolpath. Offset Pocket patterns are created with inside corner fillets and “S-link” connections to the adjacent offset passes. Bi-directional Zigzag patterns connect each pass using filleted connections. These new smooth patterns allow higher feedrates to be used while minimizing shock to the machine and cut-ting tool.
The 3D machining wizard now contains a new pencil milling method, which generates a toolpath to machine all concave surface intersections where the specified tool makes dual contact. This capability is useful for removing material remaining in corners and along fillets in both finishing and semi-finishing applications. Multiple pencil milling worksteps using progressively smaller tools can be used to trace along part features, gradually removing remaining material.
The 3D machining wizard equidistant finishing method now allows the machining to be restricted to only flat areas, by specifying a Surface Angle of 0. This feature can be used to remove remaining stock from island tops and shelves after roughing using the new Ignore Flats option.
The 3D machining wizard re-roughing method now allows previous re-roughing worksteps to be used as input for subsequent roughing of remaining material. This feature allows a more optimal re-roughing strategy to be employed, where progressively smaller tools are used in order to maintain the highest possible rigidity during each re-roughing phase.
The curve motion record now includes a new Open Edge attribute, which allows closed curve boundaries to include segments marked as open. When curves containing open edges are used by Pocketing or Zigzag cycles, the open edge segments are offset outward, allowing the boundary to be treated as an open pocket. This feature allows boundary curves to be used directly from the model, without the need to manually create additional offset geometry and modify the curve.
The contour cycle has been enhanced to provide options to automatically insert rapid breaks along the curve profile. The rapid breaks are defined by specifying a number of tabs and a tab width in the workstep Cycle Data dialog box.
New Curve Boolean Operations allow the active curve to be modified by referencing a second curve, and performing the specified Boolean operation. Union, Intersect, and Subtract operations are supported. This new capability allows complex curve boundaries or paths to be formed directly from slice or boundary curves, without the need to manually create and edit wire frame geometry.
New Inner to Outer and Outer to Inner Curve ordering commands automatically sort nested curve loops, ordering them from the inside out, or outside in.
The post processor is now capable of supporting Fanuc style G98 return to Initial plane, or G99 return to Retract plane behaviors. The SAX Basic format language provides new conditional logic statements that can be used to output the required G98/G99 codes based on the Rapid or Linear link types of the curve used by drilling work step.
The Retract “To Clear” option, located in the Z Data section of the machining dialogs, can be used when contouring open profiles with multiple Z steps. Instead of retracting to Z-rapid plane the new option retracts to the clearance level above previous steps Z plane before moving back in X and Y.
For more information, visit EZ-CAM.
Sources: Press materials received from the company and additional information gleaned from the company’s website.
Subscribe to our FREE magazine,
FREE email newsletters or both!Latest News
About the Author

DE’s editors contribute news and new product announcements to Digital Engineering.
Press releases may be sent to them via [email protected].
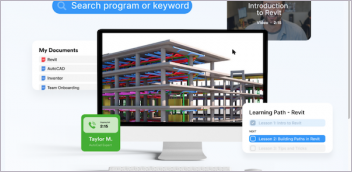

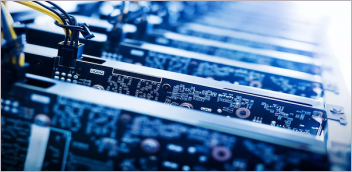
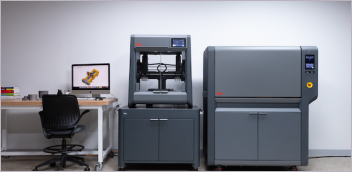