ExOne Expands Material Options

ExOne has added bonded tungsten to the materials available for the M-Flex metal AM system. Courtesy of ExOne.
Latest News
August 13, 2013
Success in business is rarely achieved by sitting back and relying on a single product to succeed. Even companies the likes of Coca-Cola have attempted to shake up the status quo with new products (admittedly with mixed results). In the additive manufacturing (AM) industry, systems are only half the equation, the other half is continuing development of new materials.
ExOne is moving ahead to provide a greater variety of materials for its customers with ongoing research in its Material Applications Laboratory. Alongside tried-and-true 316 and 420 stainless steel infiltrated with bronze, the company is now offering bonded tungsten, and iron infiltrated with bronze. On the sand casting side of the business, ExOne will be offering phenolic and sodium silicate to its suite of binders.
“We are excited to add iron infiltrated with bronze to our product offerings,” said Rick Lucas, ExOne’s CTO. “We continue to focus on the development of our other metals and materials. We remain committed to releasing at least one new material every six months. Our priorities are defined by the needs of our current customers and as we uncover new opportunities with prospective customers.”
The ExOne process varies slightly depending on material, but, in general, powdered material is treated with a bonding agent from a print head to create an object. Metal objects are taken from the build box and placed into a furnace for sintering, which burns out the binder and fuses the metal molecules into a solid part. The process can leave small internal gaps, which are filled using infiltration (generally a bronze infiltrant) and a second thermal process, resulting in a fully dense object.
ExOne collaborated with rp+m to develop bonded tungsten for use in shielding products designed to protect people and the environment from ionizing radiation. Used in the company’s M-Flex AM system, this new material can replace lead shielding and is a Restriction of Use of Hazardous Substances-compliant solution.
“3D printed bonded tungsten is a great solution for radiation shielding because the M-Flex can create complex shapes for these applications that would be difficult to create with conventional methods of manufacturing,” said Lucas. “Our collaboration with rp+m demonstrates the power of ExOne’s strategy in engaging customers in the early stages of the materials development process, yielding direct applications in new markets.”
For sand casting, ExOne says its new phenolic binder offers the potential for casting higher heat alloys, creating a higher strength mold or core, and improving the quality of the casting due to reduced expansion of the mold or core. These new possibilities are meant to address potential concerns with sand casting for the automotive, aviation, hydraulic/heavy equipment and pump industries.
Additionally, the sodium silicate binder is meant to reduce or eliminate the release of fumes and gas in the casting process, helping to reduce costs associated with air ventilation, and electrical and maintenance equipment.
Below you’ll find a video about ExOne’s metal printing process.
Source: ExOne
Subscribe to our FREE magazine,
FREE email newsletters or both!Latest News
About the Author
John NewmanJohn Newman is a Digital Engineering contributor who focuses on 3D printing. Contact him via [email protected] and read his posts on Rapid Ready Technology.
Follow DE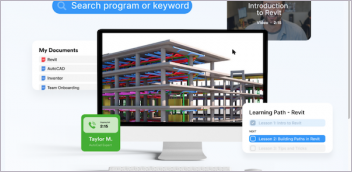

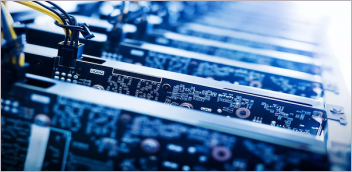
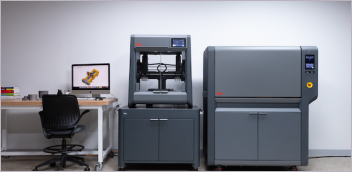