Latest News
June 13, 2018
ESTECO simulation process automation software users from around the globe gathered May 23-24 in picturesque Trieste, Italy to explore emerging trends in data management. The new frontier, it seems, is in exploring the gaps between disciplines.
“Optimization was falling between the cracks,” noted Bob Tickel, director of structural and dynamic analysis at motor and power generation manufacturer Cummins. “We had too much of a discipline-specific focus; we had to make an effort to unite the disciplines around workflow optimization.”
Throughout the 1990s, analysis at Cummins was about component-level testing. Tickel said it was a reactive rather than a proactive process. “We developed a successful history of ‘build it, test it.’” The economic downturn of 2001 was one of several factors that led Cummins on a quest to improve its analysis process. The company started an initiative called analysis-led design, focusing first on technical productivity.
It was a top-down initiative, Tickel said, which pushed for an acceleration in the use of analytics. Engineers were told to wait for analysis results before running physical tests, and then use analysis results whenever possible to reduce or minimize testing. The company increased its analysis team by creating a new unit in Pune, India. Today Pune has 500 engineers working on design computational fluid dynamics (CFD) and structural analysis. There was a new focus on measuring productivity as a way of bringing in additional measurable accountability.
Optimization-Driven Design
Today the simulation and analysis focus for Cummins is on predictive analysis and optimization-driven design. “We are still doing mostly design-led analysis, but the goal is analysis-led design,” said Tickel. Most of the work with ESTECO software as well as other CAE products is done on high-performance computing (HPC) clusters. The main cluster is called “Clessie” after the nickname of the company founder. The ability of HPC to grind the numbers at a high rate has led Cummins to explore multidisciplinary optimization in an evolutionary fashion. In 2011 analysis was done by about 10 engineers and focused primarily on applied mechanics; there was minimal use of HPC resources. By 2015 Cummins employed around 25 engineers to focus on HPC-based analysis of long-solving physics problems. The number of analysis engineers doubled in 2016 as Cummins placed resources behind increased HPC use. Today there are more than 100 HPC analysis engineers running hundreds of jobs in parallel, with as many as 50,000 design points under analysis.As the use of HPC grew, Tickel said the company realized engineering was still about small groups running advanced digital simulations but manually reporting the data. So Tickel and his team started working to incorporate multidisciplinary optimization to unite the various discipline-based analysis projects into one workflow. “It is a different way of thinking,” Tickel told conference attendees. “We needed new training, and sometimes we needed new people. In the past we were getting deeper and deeper into the physics. But it is better to understand the design space and then zero in on the physics.” Internal subject motor experts, with their years of tacit knowledge, were given increased visibility in the optimization initiative, to quantify their qualitative understanding of power generation physics and processes.
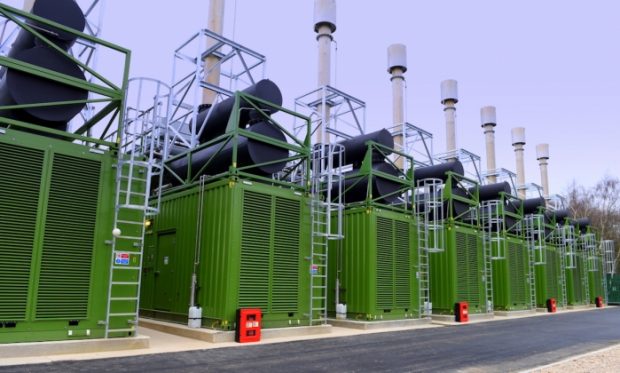
The Cummins multidisciplinary design optimization initiative would go nowhere without HPC computing. “We now routinely do 50,000 design points in a day or two,” Tickel said. Staff engineers are impressed, Tickel said, but “now we need to standardize how to make the decisions.”
Change is hard, he said. “We can now help customers think 10 levels deep, not two levels. This is transformative,” he added. To codify the process, Cummins has introduced a development cycle optimization strategy. There are four steps:
- Concept Architecture Development for selecting the right architecture.
- Stable Concept Architecture as a basis for system optimization.
- Stable System Architecture as a basis for design optimization.
- Stable System Design to execute value package information (VPI).
Updating User Experience
An improved VPI experience is at the heart of this year’s updates to the ESTECO line, led by updates to modeFRONTIER (engineering design optimization) and VOLTA (web-based platform for process automation and simulation data management).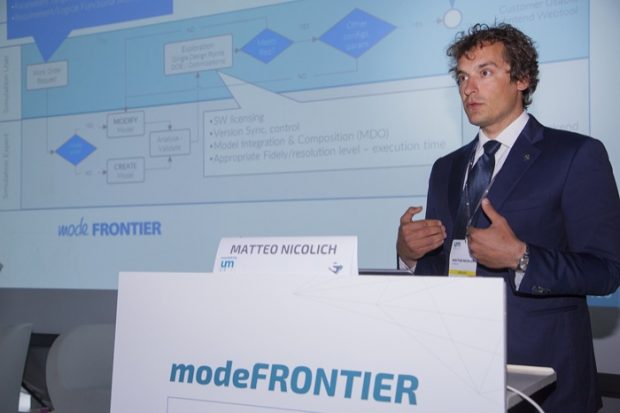
Artificial intelligence (AI) algorithms have been added to allow better predictive analysis. modeFRONTIER has been given a facelift, so to speak, with a new user interface designed to improve collaborative use. VOLTA is ESTECO’s new hub for enterprise analysis collaboration. The 2018 release offer the new My Teams data hub, where team can focus on specific design tasks.
“No single expert can do the entire simulation; this pushes engineers to work together,” said ESTECO Product Manager Matteo Nicolich. “We use collaboration to give simulation experts a way to build processes and connect with PLM apps, and to give visibility to managers and others in the process, to deliver their expertise.”
Democratization of engineering data is the key, in contrast to democratization of tools and processes. “Collaboration in general is not easy,” added Nicolich. “It can’t be free, but as you lower the cost the more users collaborate. People are in charge of sharing directly. Yet we support structure at an enterprise level so the company has its standards.”
ESTECO wants to support moving legacy behaviors to digital workflows for design optimization. These changes, Nicolich said, include shifting from the analog to the digital in several dimensions:
- from waterfall, asynchronous processes to agile, real-time collaboration;
- from vertical integration to extendable reusable processes;
- from guessing and intuition as engineering processes to digital design data driving all processes; and
- from manual workflows to AI-powered engineering experiences.
“There should be one (analysis) platform,” said Nicolich, which unite multiple existing domains such as simulation data management, execution planning, reliability management and other disciplines.
Subscribe to our FREE magazine,
FREE email newsletters or both!Latest News
About the Author

Randall S. Newton is principal analyst at Consilia Vektor, covering engineering technology. He has been part of the computer graphics industry in a variety of roles since 1985.
Follow DE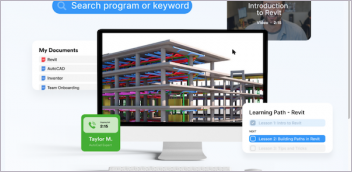

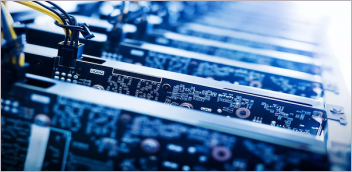
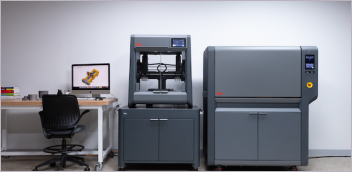