Latest News
November 1, 2010
By DE Editors
Infusion is a process widely used to manufacture large components such as wind blades or wing boxes. However, determining vent locations and injection strategy is a challenge for large, complex parts made of different composite materials and inserts, and for which the resin flow through the thickness is not uniform. Accurately managing these large or complex components has required volumic modeling, costing companies the time and expense of trials to reach a working manufacturing process.
PAM-RTM 2010 is part of ESI Group’s Composites Simulation Suite of industrial software for the design, performance and manufacturing simulation of composite components. The 2010 release of PAM-RTM includes a solver enabling distributed memory processing (DMP) computations for liquid composites molding (LCM) process simulation. It covers a range of manufacturing processes based on LCM, helping process engineers and designers to evaluate manufacturing strategies and optimize process parameters regardless of component size.
Components using millions of elements (shells as well as solids) are now treated, and simulations can be completed in a matter of hours, according to the company. PAM-RTM 2010 enables LCM simulation for very large parts, for complex geometries requiring a detailed mesh, and for thick parts in which the non-uniformity of the resin flow through the thickness cannot be neglected.
PAM-RTM 2010 offers additional enhancements and consolidations of 2009 functionalities, such as the automatic injection flow rate control to reduce porosity in the parts and the “one shot” simulation to rapidly estimate the last area to be filled and filling time, the conditional opening and closing of the gates, the influence on permeability of fiber shearing during draping. All these enhancements provide users with a more rapid decision-making solution for process, part quality and mold optimization, according to the company.
For more information, visit ESI.
Sources: Press materials received from the company and additional information gleaned from the company’s website.
Subscribe to our FREE magazine,
FREE email newsletters or both!Latest News
About the Author

DE’s editors contribute news and new product announcements to Digital Engineering.
Press releases may be sent to them via [email protected].
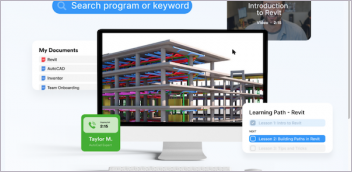

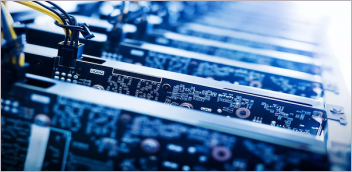
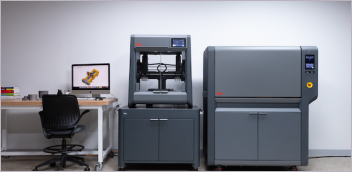