EOS Unveils Two New Additive Manufacturing Systems: the EOS P 396 and the EOS M 400

The EOS P 396 offers industrial manufacturing in plastic. Courtesy of EOS.
Latest News
December 4, 2013
The news just keeps rolling out from Euromold. Additive manufacturing (AM) systems are on the rise, and EOS is adding to the possibilities offered by the technology with the announcement of two new industrial 3D printers. The EOS P 396 works with plastic material, and the EOS M 400 builds in metal.
According to the company, the EOS P 396 offers improvements over older AM systems by increasing material efficiency by up to 30%. Secondary processing times have been reduced thanks to a new point pyrometer and a low wearing, high speed recoater. The new point pyrometer measures the temperature of the powder surface with the intention of improving coating precision. Primary processing times have also been reduced with the introduction of a new, CO2, 70 W laser.

The build envelope of the EOS P 396 measures 340 x 340 x 600 mm (13.4 x 13.4 x 23.6 in.). The new AM system has a build speed of up to 48 mm/h (1.9 in/h), and a top layer thickness of 0.06 mm (0.00236 in). At launch, the materials available for the EOS P 396 will be the plastic materials PA 2200 and PrimePart PLUS (PA 2221), with other materials to follow.
“With the presentation of the EOS P 396 at Euromold we are sustaining a leading role in plastics-based additive manufacturing, a position that stands alongside our metals technology,” said Adrian Keppler, managing director at EOS. “The EOS P 396 seamlessly supersedes our highly successful EOSINT P 395 model in the mid-frame segment. We have made a number of improvements that allow our customers to produce both plastic prototypes and serial parts with an even higher quality and cost efficiency.”
Moving on to the metal side, the EOS M 400 offers a modular AM solution with both set-up and process stations, and an automated unpacking station to be launched later next year. The modular concept incorporates an exchangeable frame, including components and residual powder, that may be moved, following the build process, from the process station to the unpacking station.

The EOS M 400 also introduces new monitoring equipment, including a camera integrated into the build chamber to monitor the powder bed, and other instruments to keep track of the position of z axis, laser power, scanner position, humidity, temperature and pressure. As an industrial AM system, the build envelope allows for prints as large as 400 x 400 x 400 mm (15.8 x 15.8 x 15.8 in.), and prints are built with a 1kW Yb-fibre laser.
“EOS is pursuing a platform-based strategy for the metal technology and is able to support its customers from the research and development phase, through to series production,” said Keppler. “The EOS M 400 represents the key to the industrial series utilization of additive manufacturing. The new system supports users not only in the context of its qualification for production, but also in actual manufacturing applications. We won’t be drawing the line at a single solution. We will be expanding the platform with successive performance modules.”
Below you’ll find a video concept study from EOS.
Source: EOS
Subscribe to our FREE magazine,
FREE email newsletters or both!Latest News
About the Author
John NewmanJohn Newman is a Digital Engineering contributor who focuses on 3D printing. Contact him via [email protected] and read his posts on Rapid Ready Technology.
Follow DERelated Topics
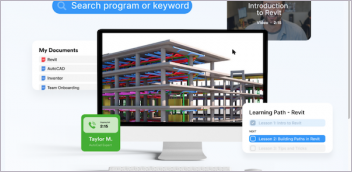

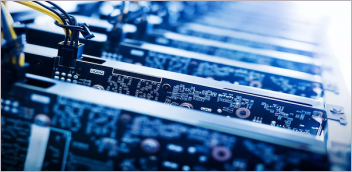
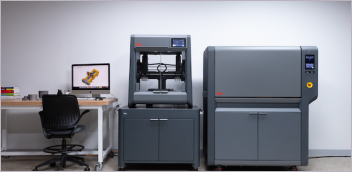