Engineering Workstations Built for Speed
Trek Bicycle uses powerful NVIDIA RTX™ technology to enable multi-application workflows.

Trek leverages NVIDIA RTX™ GPU acceleration for rendering, visualization and simulation. All images courtesy of Trek Bicycle.
Engineering Resource Center News
Engineering Resource Center Resources


Dell

Latest News
July 21, 2022
Michael Hammond is the Digital Visual Communications lead at Trek Bicycle, a Wisconsin-based manufacturer of bicycles and other cycling products. Hammond heads up visualization and rendering operations for the company, which leverages NVIDIA RTX™ technology in its Dell Precision workstations, including the new NVIDIA RTX™ A5500 GPU, as well as a machine running dual RTX™ A6000 GPUs. Hammond spoke to us about how these powerful graphics processors enable multi-application workflows that have enhanced productivity.
Can you describe the design and engineering department at Trek, and give us an idea of how the product development process works?
Michael Hammond: I head up a small team that does visualization, so a lot of what I do is at the tail end of the work we do. From a product development standpoint, I think our operation is straightforward. We go from user research to early concept generation and fleshing out a range of ideas. Then it is on to building prototypes and iterating as we go. One thing that is unique here is that industrial designers and engineers work closely together throughout the product development cycle. We never just hand things over the wall.
We have an analysis team that is reliant on computing power for CFD and FEA analysis, and we have a biomechanics team that is part of that analysis group doing motion capture and pressure mapping to understand how the body is interacting with the bicycle.
What would you say are the unique challenges in design and engineering bikes?
What is unique to bicycle design is that we have carbon (or alloy) structures and we do not have the luxury of hiding anything. Most of what you see is the structure. Industrial design intent and engineering intent have to be well balanced. We're focused on making the highest performing frame that we can with the time we have, and still making it sexy. We have to make products that stir the riders’ emotions.
We spend hundreds of hours squeezing every gram of performance from the frame, literally. Weight is always a key challenge, as are the aerodynamics on the high-end road bikes. We are always trying to improve rider performance. Bikes need to feel a certain way on the road or the trail, and we spend a lot of time with athletes to figure out where to make critical changes that include tweaks to geometry, tweaks in where the flex is in frame, and taking the edge off of bumps.
As engineering needs grow more complex, what types of multi-application workflows have emerged at Trek? What types of applications do you typically use simultaneously on the hardware? Has that changed over time?
We have a lot going on simultaneously – for CAD tools we are leveraging either SolidWorks or Onshape depending on the product, and we are leveraging either KeyShot or Cinema 4D with Redshift along with the Adobe Suite – including Substance. All are computationally demanding and graphics intensive, and we want to be able to work seamlessly between the apps. Our Trek Performance Research team also uses Abaqus for FEA and for CFD we have recently moved to STAR CCM+ to take advantage of the GPU processing capabilities.
Has this posed any challenges in the past, in terms of workstation performance?
Yes, of course! Before the NVIDIA RTX™ GPUs we didn’t have nearly the real-time capabilities we do today. It's been such a leap forward for design, engineering, and now our visualization team to be able to tap into NVIDIA RTX GPUs. We’re able to iterate quicker, we’re able to show more options. Having access to a workstation with an NVIDIA RTX™ A5500 is a gamechanger.
My personal laptop is an older unit with a Quadro RTX™ 4000 GPU, which was a massive leap compared to what I had before. Being able to do desktop rendering fast, and see things in real time has been awesome.
Having additional horsepower provides faster performance for VR work and for visualization of products. We are using Cinema 4D and Redshift to produce our digital content renderings, and to be able to visualize things as you are working in real time.
With Cinema 4D we are doing iterative rendering in real time to get a clear picture of the end result. The faster you can process the image, the faster you can make a decision. Is the color and material correct? This is similar to using GPU power for a CFD result. It comes down to iteration cycles – the more you can get out of your day the better design you have in the end.
You can try out multiple designs. Before RTX GPUs we did not have enough time because we did not have enough horsepower to do calculations quickly.
How have the NVIDIA GPUs improved multi-application use?
All that matters is processing speed. More speed equals more iteration time – and the RTX A5500 enables more iterations. On any project, you have a timeline and you only get so many turns of the crank, so to speak, and more turns of the crank yield a more refined result – whether that’s detailed CAD, a rendering/animation, or the final product. Being able to flip back and forth between apps, or leave them open and running without bogging down resources is great.
The CAD models we use to produce bikes are going to be different from what I am going to use to create a visualization. When I pull the CAD out of PDM and modify it, I am going to be adding a lot of detail that the engineers aren’t as interested in: We are doing a lot of split lines for paint, and adding in the tiniest of visual details. We often import native models directly into Keyshot or Cinema4D. We also export models and use a tool to re-mesh the CAD, or we are converting art files in Illustrator or PhotoShop – often all at the same time. So there are heavy loads on the workstations.
We have an RTX A5500 on one machine, and dual RTX™ A6000s on two workstations. The Dell Precision 7920 units with the dual RTX A6000s are for Cinema 4D use, and seeing things in real time align with rendering outputs. We want to process those quickly. We do not have a render node on a stack yet, so rendering is done on a local workstation. What is nice about that is that we can work quickly on local files on our own network. The other workstation with the RTX A5500 is running VR applications for product design.
How else is this combination of hardware and software enabling new capabilities for Trek?
The visualization team is focused on achieving parity with the product photo team. Our renderings have to be not just photorealistic, but accurate in representing the product specifications. The advantage in using digital tools is that we can render without setting up and taking down physical lights, cameras, and products. And if we are missing a (physical) part from a vendor our photo team has to hold – we are not constrained by that. We are also working on our Project One online bike configurator, and the number of options is a little daunting when it comes to doing renderings, we will be producing 1000’s of images. Without high-end GPUs this would be impossible in the amount of time we have. There is a whole pipeline to build to ensure we are getting the CAD, materials, graphics, and color visually accurate, and be able to automate to ensure speed and consistency.
More Dell Coverage
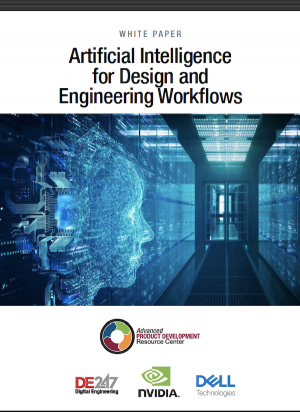
More NVIDIA Coverage
Subscribe to our FREE magazine,
FREE email newsletters or both!Latest News
Related Topics
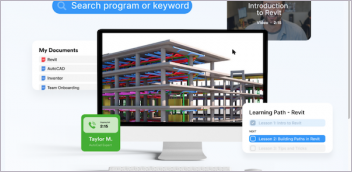

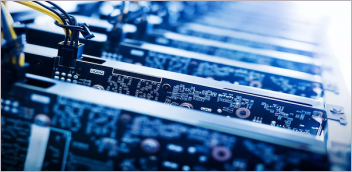
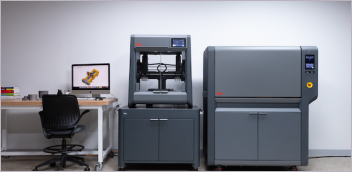