Engineering Technologies Still Require the Human Element

Siemens researchers are exploring ways to move complicated iterative simulation processes, such as this study of variables in heat sink design, into real-time design space exploration. Image courtesy of Siemens PLM Software.
Virtual Reality (VR) and Augmented Reality (AR) News
Virtual Reality (VR) and Augmented Reality (AR) Resources


Latest News
December 1, 2017
Advances in computing speeds are allowing engineering software vendors to rapidly innovate in simulation and rendering, and to integrate peripheral technologies such as virtual reality (VR) and augmented reality (AR). It is now possible to change a design and visualize the effects of those changes in real time. Simulation is moving closer to real-time display but lags behind visualization rendering due to the additional computational requirements.
Although every research advance is appreciated and applied, the idea of how to apply new technology is as important as selecting the technology to use. Reaching a better state of collaboration at all levels of the organization and the supply chain are not dependent on one specific product, but on attitudes and willingness to change. Real-time simulation or VR/AR use won’t shorten deadlines on its own.
Studying VR/AR for Real-Time Simulation
Researchers at the University of Singapore are studying the potential of both virtual and augmented reality for real-time simulation. They are especially intrigued by the idea of interactive simulation to study the behavior of materials, which they see as an important way to accelerate the product development cycle, according to researchers Li, Nee and Ong. “Interaction methods have been studied to utilize the simulation results provided in a VR environment so as to improve the efficiency of the analysis and the design process.”

But there are currently limitations that require more research. One is placement of the product being studied in situ with real-world surroundings, whether that be a larger assembly, a factory or in the field. This is mostly an access-to-data problem, not a technical limitation. Another is improving the ability for humans to interact with the virtual environment; today, most VR systems are limited to adjusting the view location, although several vendors and research facilities are working on more advanced interaction methods. There is also the larger problem of possible VR-induced nausea in sensitive people, but that is a problem for all VR applications, not engineering simulation in particular.
Deformation simulation in VR has also been studied. Software approaches under consideration include various approximation methods and the use of artificial neural networks as the processing environment. Availability of related environment data is again seen as a primary issue, along with hardware limitations and the oft-cited puke factor that seems to accompany all VR research.
Collaboration is Never as Simple as it Sounds
In 2013 a provocative essay called “A Great Idea Is Never Enough” in Inc. Magazine took the industry to task for only paying lip service to the potential of technology to enable disruptive collaboration. “The system vastly overvalues great ideas and undervalues execution,” said author Eric Paley. In our personal lives, most of us have allowed social media to transform how we socialize, work and learn. But manufacturing—and product development in particular—has been slow to allow technology to redefine key workflows that would impact every step of the value chain.”

One way to encourage collaboration is to eliminate artificial barriers keeping colleagues from working together. Startup CAD vendor Onshape says its cloud-based approach to mechanical CAD encourages collaboration at the earliest stages of design by disrupting the isolating monolith of one person/one CAD tool. When multiple designers work on a project, all share access to the same model. Any team member can work on any part of the model at any time. There is no file to check in and check out; version control is automatic and constant.
Onshape uses Web Services, a refinement of web technology that brings the “small pieces loosely joined” philosophy of the web to software development. Other vendors are exploring how to take advantage of Web Services technology to enable collaboration, encourage lean engineering processes and enable agile methodologies in product design.

Collaboration in engineering occurs on a continuum, says Systems Engineering Researcher A.M. Madni. There are four aspects:
1. intradisciplinary collaboration occurs among colleagues within a discipline;
2. multidisciplinary collaboration brings together colleagues from different disciplines;
3. interdisciplinary collaboration occurs among the disciplines; and
4. transdisciplinary collaboration happens when there is knowledge unification across disciplines.
To enable full collaboration, Madni argues that engineering must become more transdisciplinary in practice throughout the organization and with all allied vendors. The rise of mechatronics in recent years is an example, as is the more recent trend of CAD and mechanical simulation companies acquiring electronics-oriented simulation products. But it takes more than tools to move to transdisciplinary collaboration. New best practices and new relationships with suppliers need to be established.
Bringing Simulation into Real Time
Today’s simulation software products are increasingly being used to investigate a variety of high-dimensional design spaces beyond what human imagination can conceive. Complicated assemblies can now be presented as a unit in CAD and CAE software at high fidelity. Topology optimization methods are creating new ways to create designs not previously capable of manufacture. Products to be created by additive manufacturing are using generative design algorithms to create hollow chambers in objects that were previously carved from solid metal. A new generation of mold-design software products are used to create innovative, complex designs for conformal cooling molds. Such spaces can require calculating more than 1 million degrees of freedom.
Until recently it was taken for granted that all CAE software would be running on CPUs, which approach computation primarily as a serial process. But now that high-performance GPUs are common in engineering environments—which use parallel processing to calculate graphics—vendors and institutional researchers are looking at how to redefine the problems to take advantage of parallel processing. Researchers at Siemens are looking at several methods involving new approaches to grids and voxel-based cell analysis. The goal is to make analysis of complex high-dimensional design spaces available to engineers in real time. Such results will be presented either on the screen or through VR.
The Siemens research team of Stefan Gavranovic, Dirk Hartmann and Phillip Stelzig believe the future of real-time solvers in high-dimensional design spaces will be “purpose-built exploration solvers,” which will generate both the design and the code for analysis, used in real time for the creative processes. The first step will be interactive cause-effect simulations for non-experts that would bring the simulation process into initial design stages, but still require referral to high-end solvers and analysts for final verification.
Earlier this year CAE vendor ANSYS introduced Discovery Live, a new tool for what they call pervasive simulation. The goal is to create CAE software that makes sense for use by the large percentage of engineers who currently never run analysis software, to point them in the right direction. “The what-if questions are important,” says S. Subbiah, vice president of global product operations at ANSYS. “Accuracy [during design] is the wrong approach. You need directional accuracy.”
Discovery Live, currently available as a technology preview online, runs on workstations equipped with newer NVIDIA GPUs. The software supports fluid, structural and thermal simulation applications. Users can run an analysis-first approach to interactively explore and iterate with models. Automotive manufacturer Cummins is an early tester. “[Discovery Live] allows us to use multiple physics and the results are practically instantaneous, so we can get answers to the quick ‘what-if’ studies very quickly,” says Bob Tickel, director of structural and dynamic analysis at Cummins.
What Engineers are Thinking About VR/AR
There is much discussion about what the role of VR and AR in product design and manufacturing. Digital Engineering recently conducted a survey of readers on a variety of topics. One question was on the anticipated use of either VR or AR. Responses consistently pointed to interactive uses of the technology as opposed to review visualization. “It will help most when we have a human interfacing with the product,” said an engineer at a compressed air products manufacturer. “Where there are no humans interacting, it is of little use.”

“Preview systems prior to their implementation,” suggested an electronics engineer with experience as a software developer. “Also potential to use in field service applications.”
“‘Live work instructions and assistants,” are one way to use AR, said an engineer at maker of specialty forging equipment. “Easier communication with front line workers regarding new process and equipment installation and implementation.”
More Info
Subscribe to our FREE magazine,
FREE email newsletters or both!Latest News
About the Author

Randall S. Newton is principal analyst at Consilia Vektor, covering engineering technology. He has been part of the computer graphics industry in a variety of roles since 1985.
Follow DE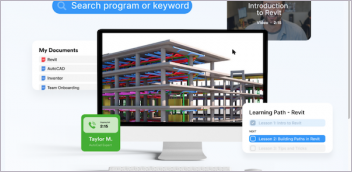

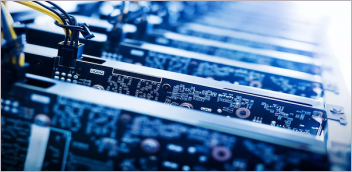
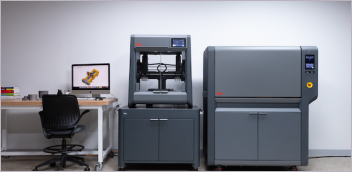