
Fig. 6: The wake vortex structure and the pressure distribution on the blade at the forward velocity of 11.5 m/s and the azimuth angles of 180° and 270°. Image courtesy of TsAGI.
Latest News
October 1, 2015
By P.N. Subbotina, T.V. Trebunskikh, Mentor Graphics; B.S. Kritsky, Sc.D., M.S. Makhnev, R.M. Mirgazov, Ph.D. , TsAGI, Zhukovsky
The Central Aerohydrodynamic Institute (TsAGI) was founded on Dec. 1, 1918, under the initiative and leadership of N.E. Zhukovsky, the father of Russian aviation. It was the first scientific institution to combine basic studies, applied research, structural design, pilot production and testing. Over its distinguished history, TsAGI has developed new aerodynamic configurations, aircraft stability/controllability criteria and strength requirements. It was a pioneer in the theory of flutter, along with many other theories, applications and experimental studies.
Today TsAGI is one of the largest scientific research centers in the world. Over the last few years, it has established contacts with a majority of research and development centers and aircraft manufacturers in Europe, the United States and Asia and has participated in a large number of joint research programs including the development of next-generation aircraft.
One of the main areas of TsAGI activity is investigating new configurations of helicopters in general, and helicopter rotors in particular. The new sliding technology of rotation brings FloEFD into the world of challenging problems in aerodynamics such as the modeling of a helicopter rotor. This has allowed the validation of the single blade rotor model in cooperation with TsAGI. This technology became available in the latest release of FloEFD, a 3D computational fluid dynamics (CFD) analysis solution from Mentor Graphics, which provides extended capabilities for simulations of rotating equipment such as pumps, fans and blowers. With its new sliding technology the software extends the boundaries of simulating turbomachinery equipment to the cases where fluid quantity is highly non-uniform around a rotating part.
The FloEFD code validation is performed against the experimental data obtained by L.S. Pavlov in 1979 and the numerical data obtained by a traditional computational fluid dynamics (CFD) code and by the TsAGI specialized software product.
The model rotor consists of one rectangular, untwisted NACA0012 rigid blade mounted on a hub containing a drive shaft with a balance weight (Fig. 3). The model rotor is defined by the geometrical parameters given in Table 1.
Pressure distributions have been measured at 10 cross-sections of the blade r¯=r/R=0.2; 0.3; 0.4; 0.5; 0.6; 0.7; 0.8; 0.9; 0.95; 0.99. In the simulation the following forward velocities were considered: hover mode (V∞= 0) and horizontal flight (V∞=11.5 m/c).
The ambient temperature is 15 °C at an atmospheric pressure of 101325 Pa. The blade rotates with an angular velocity of 36.5 rad/s. All presented parameters as well as experimental data were taken from the T-105 wind tunnel experiments of L.S. Pavlov.
The mesh settings within FloEFD were set to a uniform mesh with a high mesh density in the vicinity of the rotor and extended to the boundaries of the computational domain. Two local meshes, one around the rotor and one on the blade surface, were applied to resolve the tip of the leading edge of the blade. This resulted in an initial mesh of about 2,700,000 cells (Fig. 4) that was meshed in about five minutes. The mesh with the traditional CFD was made of tetrahedral cells and resulted in a mesh of about 8,500,000 cells.

The FloEFD calculations were performed as transient (unsteady) analysis in three stages with different time steps decreasing from the azimuth angle of 9° per one iteration to the azimuth angle of 1° per one iteration for the last revolution on which the presented results were obtained. It took about 36 hours to simulate each case on Intel Xeon 2.7GHz processors, 8 CPUs, 32GB RAM and about 30 minutes to specify the project.
The traditional CFD calculations were performed on a cluster of 24 computers with Intel Xeon 2.8GHz processors, 12 CPUs, 100GB RAM (the total number of CPUs used was 288). It took about 48 hours to simulate each case and about seven days to specify the project and the calculation mesh.
The simulation was also performed by using the TsAGI specialized software RC-VTOL based on a nonlinear vortex theory (S.M. Belotserkovsky’s school). The calculations were performed on Intel 3GHz processors, 4 CPUs, 8GB RAM and took about 20 minutes per each case. The wake vortex structures calculated by FloEFD (left) and traditional CFD (right) are demonstrated in Fig. 6.

This study demonstrates that all software tools have successfully validated the problem of predicting the helicopter rotor blade characteristics. FloEFD is less demanding of computer resources than the traditional CFD approach: It takes about 30 minutes to prepare a project for calculation including the mesh creation; the calculation mesh required to obtain the acceptable results was three times less than the traditional CFD tool.
Subscribe to our FREE magazine,
FREE email newsletters or both!Latest News
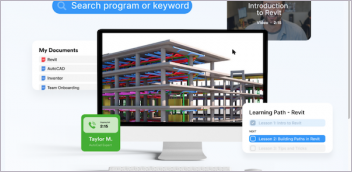

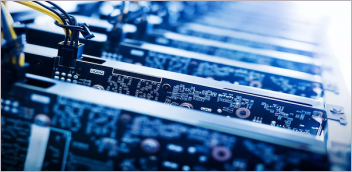
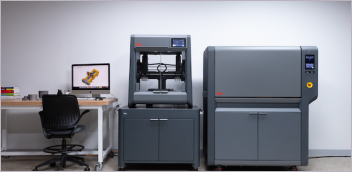