Latest News
February 1, 2011
By Michelle Boucher
With pressure to achieve profitable growth, yet fewer resources to achieve that growth, it is critical that companies find ways to work smarter. In a November 2010 Aberdeen study, Using Product Analytics to Keep Engineering on Schedule and on Budget, this topic was explored further.
![]() Top business pressure driving better decision-making in product development. |
The Business Need for Better Insight
To improve decision-making, it is important to understand what is important to the company in the first place. The figure below shows the top business pressures driving companies to have better insight into decision-making during product development.
The conclusion is clear. Quality, time, and cost are all critical, while at the same time, it is essential that the product requirements that will drive customer demand—and consequently revenue—make it into the final product. To weigh all of these factors, engineers and management must have access to the right information.
What is hardest about collecting this information? Interestingly, it all boils down to one thing: time. Engineers are so busy with their day-to-day work that stopping to provide status updates or put together needed metrics is just a distraction, preventing them from getting their design and development work done. In addition, it takes too long to go to all of the individual developers and engineers to obtain the needed information. In fact, those who participated in the Aberdeen study reported spending 18% of their time just providing status updates and preparing for design reviews.
Identifying What Works Best
To understand successful approaches to reduce that time, while still improving decision-making during product development and the business impact it has upon companies, Aberdeen conducted a study and benchmarked the performance of participants. Study participants were categorized as either Best-in-Class (top 20% of performers), Industry Average (mid 50%), or Laggard (bottom 30%). Given that the top pressures on product development are about quality, time, cost and revenue, five key performance measures that indicate success with addressing those pressures were used to distinguish the Best-in-Class from Industry Average and Laggard organizations.
![]() Best-in-Class strategies to improve decision-making. |
One of the top pressures on product development is to lower product cost. The Best-in-Class are successfully doing this by making better decisions to keep product cost down. As a result, they are 39% more likely than the Industry Average to meet product cost targets. In addition, the Best-in-Class have also seen a 7% decrease in their product costs over the last two years. By comparison, the Industry Average saw only a 1% decrease—and the Laggards actually saw an increase in product cost, putting them at a significant competitive disadvantage.
While it is impressive that the Best-in-Class have been able to take cost out, they are not doing this at the expense of quality. They are 23% more likely than the Industry Average to meet quality targets. This means they have visibility to balance what could often be conflicting criteria to arrive at an optimal solution that not only lowers cost, but also meets customer expectations in terms of quality.
Even as the Best-in-Class are able to obtain the needed information to balance cost and quality, they are simultaneously addressing the challenge of time. They are 52% more likely than the Industry Average to release products on time. This means they are collecting the information they need, without adding to development time. They also have the ability to identify bottlenecks in the process, so they can make adjustments as needed so that products are still released on time.
![]() Performance advantages of the best-in-class category, resulting from better decisions. |
Because the Best-in-Class do such a good job of managing their process, they launch their products on time. This means they optimize their window of opportunity to bring in revenue for the product. Consequently, they are 44% more likely than the Industry Average to meet revenue targets. This also means they are successfully implementing the requirements that customers want, which drives demand for the product to bring in the expected revenue.
Study Findings at a Glance As seen from the strategies executed by the Best-in-Class, better decision-making comes with better visibility and transparency to critical product development information. This means getting the right information, at the right time, to the right person. However, lack of time is a big obstacle to collecting required metrics. By putting the right process, knowledge management, organizational and performance management capabilities in place, as well as supporting technology to automate the processes, much of the pain of time-consuming tasks to prepare status updates can be avoided. Keeping this in mind will help successful execution of the Best-in-Class strategies. The full Aberdeen study is available at no cost until Feb. 28, 2011. |
Best-in-Class Strategies
The strategies followed by the Best-in-Class are very focused on getting the right information to the right people at the right time. This ensures that both engineering and management are more empowered to make the right decisions.
To address the pressure of needing to meet customer expectations for lower-priced products, the Best-in-Class are 60% more likely than their competitors to provide engineering with visibility into cost drivers. Forty-one percent (41%) of survey respondents report that products costing more than budgeted to produce is one of the top issues to have a negative impact on the success of a product. With a better understanding into what will drive up product cost, engineers can make better informed design decisions to keep product cost down.
They also ensure cross-functional stakeholders have visibility to cost drivers. This enterprise-wide approach to increase visibility to cost means everyone can do their part in contributing to keeping costs in check, which results in a boost in profitability.
The Best-in-Class are able to address time to market pressures by tracking schedule and performance across the entire product portfolio. They can recognize bottlenecks and take corrective action when needed. They also have better insight into how shifts in resources will affect other projects, helping them to better prioritize where efforts should be focused.
To meet demands for higher quality and reliability, the Best-in-Class are 32% more likely than competitors to provide engineering with visibility to field failures. This helps them learn from previous mistakes so that they can avoid similar failures in the future. They can also incorporate additional scenarios in future test plans to ensure a future failure is not repeated, improving the quality assurance process overall.
Finally, the Best-in-Class ensure management has access to critical information so that they can better manage their teams. To ensure conflicting criteria such as time, cost, quality and performance are balanced, the Best-in-Class are 25% more likely to provide management with visibility into key trade-off decisions. They are also 48% more likely than their competitors to make sure that management has visibility into critical metrics. Not only does this empower them to provide critical oversight to ensure key design criteria and requirements are met, but this also makes it possible to have early visibility into problems such as not meeting regulatory compliance. Early visibility means they can take corrective action and avoid problems that will have a negative business impact, such as stop shipments.
Michelle Boucher is a research analyst in the Product Innovation and Engineering practice at Aberdeen Group, where she focuses on identifying product development best practices. She has published more than 50 studies on the use of CAD, CAE, PLM and other topics, including manufacturing planning, systems engineering and mass customization.
Subscribe to our FREE magazine,
FREE email newsletters or both!Latest News
About the Author

DE’s editors contribute news and new product announcements to Digital Engineering.
Press releases may be sent to them via [email protected].
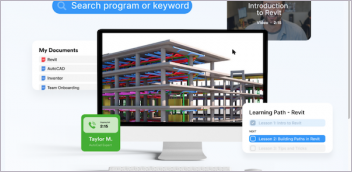

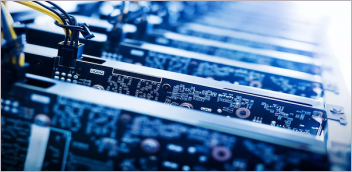
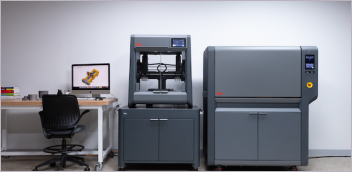