Elements of Finite Element Analysis
Proper methods of meshing structures and models is key to accurate analysis.Thisis the first installment of a series exploring where real-world, hands-on FEAis headed.
Latest News
December 1, 2004
By Tony Abbey
When I joined the UK aircraft industry in the mid 1970’s the standard methodof interacting with a computer was rudimentary. We used punch cards, each containinga line of data. We assembled the cards into a deck, forming the FE (finite element)analysis data and analysis job control definition. The deck was fed into the jawsof the mighty IBM mainframe.
My first major analysis, a composite taileron with a titanium shaft under staticloading, had an element budget of around 1000 elements using beams, bars, shells,and solids. The budget was based on the available memory of the IBM mainframeand keeping the job turnaround to 2 or 3 days.
Noran Engineering’s NEiWorks meshed this crankshaft model with TET10 elementsfor more than 1 million degrees of freedom. Its fine mesh density works well forcomplex shapes, offering accurate results.
Today, many of my clients are using 2 to 3 million elements to model a singlecomponent. FE analysis has become simpler to set up and execute, but FEA techniqueshave become more sophisticated and more powerful. Sophistication has brought awide range of specialized techniques such as nonlinear contact, rotor dynamics,random analysis, etc. More power means bigger models.
Figure 1: This simple stiffening plate is shown in NeiWorks and needs to be meshedfor analysis. The user of the embedded SolidWorks FEA program has a choice betweenusing fast TETmeshing, or the moreaccurate, but time consuming, plate meshing technique.
So, with all the increasing power and sophistication, let’s pause and ask ourselves,where is FEA heading? To begin our investigation, we’ll start our series lookingat some common meshing techniques and the merits of the elements they produce.
Big Models Mean Giga DOF
Bigger is better is a well-known cliché. In FEA this equates to the number ofelements in the model. This is sometimes a valid approach, but can also be anunnecessary drain on resources. In a worst case, it can give bad answers.
So, how can a model with many elements give worse answers than one with fewerelements? The answer lies in the approach to representing the actual physicalmodel with finite elementsthe process known as idealization.
Figure 2: This TET mesh of the stiffening plate already has an element countup around 100,000. With a thin structure like this object, plate element meshingwould probably make more senseto achieve betteraccuracy.
Consider a simple plate-like structure (see Figure 1, above). The fastest waywe canmesh this is with a tetrahedral (or TET) element mesher. A TET element is a pyramidshape that lends itself well to meshing awkward shapes. Assuming we use a higher-orderTET, one with mid-side nodes, then the results will be, in general, adequate forsolid body type regions.
On the other hand, remember engineers’ theory of bending from college? With thinplate structures, we really need a linear stress variation through the depth ofthe plate. A TET mesh may give a stress distribution very different from a smoothlinear variation.
A TET mesh is often very irregular in pattern with big variations in elementshape. A pure equal-angled TET gives the most accurate answers. As we distortfrom this, then numerical integration problems creep in and we start to get inaccuracies.To compensate for limitations of the element we would want at least 3 elementsthrough thickness.
Figure 3a: Here’s a region of the plate shown in NEiModeler meshed withplate elements, giving excellent overall accuracy.
An alternative to TET meshing is to use a dedicated plate element, designed torepresent thin shell behavior exactly. This will give excellent results and thenumber of elements necessary will drop dramatically (see Figures 3a above and 3b, below).Figure3a shows a detail of the part meshed using plate elements, Figure 3b shows thesame region using TET elements. In both cases, NEiModeler was used.
Figure 3b: TET meshing of the part means overall accuracy will suffer due tofew elements through its thickness, but detail can be assessed in complex regions.
The net result is that we may throw a lot of TET elements at the problem, butthey are not always appropriate for the physics of the structural case. A simplerand much cheaper plate mesh will give good answers in this case. The downsideof the simple mesh is that it may not be simple to set up. To extract one surfaceof the structural geometry may take some work in the preprocessor or the CAD program.In the part shown, 13 surfaces are used.
Tets, Bricks, and a Holy Grail
The earliest types of solid elements were simple brick-like shapes (see Figure4, below). In the FE world this is often referred to as a hexahedral (or HEX)element.
A basic HEX element has a node at each corner and can have a linear variationin stress in any of its principle directions. If we add mid-side nodes, then itbecomes a “higher-order” element. This means the stress variations it can modelincrease to quadratic or even higher orders. The advantage is that where we havehigh stress gradientsdue to local stress raisers in the structure shape, highlocal loading such as a jacking point, or very localized constraints such as boltsthenwe can do a better job of representing this stress distribution in the FE model.
In the geometrically simple element, the TET shape can also have nodes at cornersonly, or have mid-side nodes in addition. However, mathematically and in termsof performance, TET is an inferior element to the HEX. The simple TET with onlycorner nodes is notoriously bad. In effect, it is a constant stress element. Thismakes it a very poor approximation to any stress gradient locally, but also makesthe model overstiff, reducing deflections below correct values.
Why use such a TET element? The answer is that it is straightforward to developmeshing algorithms with the ability to model any shape, and current meshing technologyshould give high-quality TET meshes.
Figure 4: The three basic meshing element shapes are shown: (clockwise from right)TET, plate, and, one of the earliest, the HEX.
Amazingly, there is no solution yet to the search for a truly automatic HEX mesher,although many researchers have tried to achieve this over the last 25 years. Severalclaim to have found this holy grail, but all include workarounds, such as localHEX-to-TET transition zones, or do not work for all arbitrary shapes.
Some regulatory authorities in the nuclear and other industries require thatan FE model be exclusively HEX mesh. For very accurate results, such as requiredfor fatigue or fracture mechanics solutions, it may be necessary to use a HEXmesh. In this case, the timescale involved increases dramaticallytypically, severalweeks to mesh a complex solid versus just a few hours to achieve a TET mesh.
A very useful alternative is to use a 2D meshing approach (see Figure 5, below)If thevariations in the third dimension are simple lofting or sweeping shapes, thenwe can use a 2D surface mesh and extrude that into a 3D shape. The downside isthat the structure is possibly degraded in shape and there is no longer an associationbetween CAD geometry and mesh.
Figure 5: A honeycomb aircraft fuselage skin panel with facing skins meshed inplates and the core meshed with TETs using NEiModeler’s extrusion methods.
Real-World Modeling Is Tough
Verification manuals and introductory textbooks often use classical solutionsto demonstrate the principles and accuracy of FEA. This is an important part ofthe QA process of any FEA code, but it can be misleading if you think there willalways be a correct answer. Over the course of this series we will see many caseswhere modeling the real world with FEA can be tough. As in any form of engineering,approximations, interpretations, and judgments have to be made as to how the realstructure will be fabricated, held, and loaded.
The basic rule is to always question the validity of your model. Are the deflectionsand stresses simulated of the order that were expected? If I switch off the contoursmoothing, do I see the effect of bad meshing? Does the total load summation balancethe net pressure loading that I applied?
These are a few of the topics we will explore in future articles. In the meantime,remember the bottom line of analysis: Your analysis is guilty until proved innocent.
Technical Manager Tony Abbey works for Noran Engineering where he demystifies FEA for current users and buildssolutions for the future. Send him your thoughts on this article via e-mail c/o[email protected].
A Brief History of FEA
By the time the first practical semblance of modern computing methods arrivedin the 1950’s, the aircraft industry already had a long tradition of solving structuralproblems using simultaneous equations. So, it’s no surprise that methods of solvingby computer quickly emerged.
However, the drive to automate this process by being able to describe the equationsso that general structural problems could be solved was much slower in coming.An early false start came out of a very logical approach: Stress engineers aremost interested in stresses. Stresses are derived from forces. So, it seemed sensibleto solve the structural equations for forces using flexibility matrices. However,it proved impossible to set up a general problem definition and solution methodwith forces as the unknown.
There was a big step forward when it was realized that solving for displacementsusing stiffness matrices was very practical. Soon after, the idea of definingthe structural equations via the concept of elements connecting nodal degreesof freedom evolved. This provided a convenient way of visualizing equations. Insteadof pages of math, we have a nice physical analogy.
Opinions on who first coined the term “finite elements” differ on both sidesof the Atlantic, and mathematicians claim, as ever, that they invented the ideamany years earlier. However, the terminology and the basic idea has remained withus ever since. TA
Company Information
Noran Engineering
Westminster, CA
nenastran.com
Subscribe to our FREE magazine,
FREE email newsletters or both!Latest News
About the Author

Tony Abbey is a consultant analyst with his own company, FETraining. He also works as training manager for NAFEMS, responsible for developing and implementing training classes, including e-learning classes. Send e-mail about this article to [email protected].
Follow DE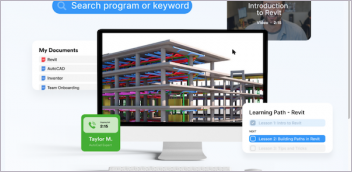

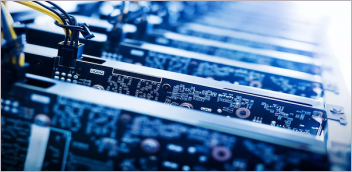
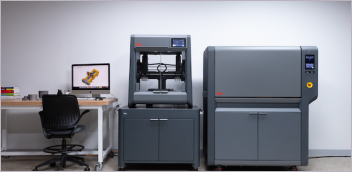