Editor’s Pick: Sustainable Designs for Manufacture and Assembly
DFMA 2009 helps engineers assess a product's environmental impact while simplifying design and holding down costs.
Latest News
April 1, 2009
By Anthony J. Lockwood
Dear Desktop Engineering Reader:
![]() |
“Green,” for lack of an actual quotation, “is good.” Designing and making stuff with an eye on its environmental impact is the new color of money. But making a green product that is cost-effective from concept through manufacture to the end of its lifecycle and that people will buy because it is a superior product that happens to be green is a big-time engineering challenge. DFMA 2009 with Design for Environment (DFE) functionality from Boothroyd Dewhurst helps you meet the challenge.
It’s common knowledge that most of your product costs are built in during design and that most companies focus on manufacturing and labor costs to control expenses and increase gross profits. DFMA – Design for Manufacture and Assembly – focuses on both ends of this reality with particular emphasis on reducing those costs you build into your design early in the process. Built-in costs include materials or parts, of course, but DFMA views built-in costs as that and more. That is why DFMA also focuses on helping you make designs that are less costly to manufacture and assemble. Now with DFE, it also focuses on helping you design cost-effective products that comply with government-enforced environmental mandates. More on that in a moment.
The DFMA software suite complements your CAD/CAM/CAE systems, and can be used at any stage of product development. Designers and engineers use it to analyze and gain insight into the costs of manufacturing and assembling products—part counts, materials, labor, and their expenses. But it’s not just a COGS calculator, handy as that is. The real genius in DFMA is that you can use it in the early concept development phases to reduce the number of parts you need to achieve your product’s functional specifications, yet has all the elegance and robustness to meet or exceed your initial expectations. Not only does fewer parts mean less to buy, it can make themanufacturing and assembly processes more cost-efficient.
Back to green. DFMA with DFE extends this capacity by giving you the tools to analyze the environmental impact of your material choices from the concept stage on up. You can determine a product’s end-of-life scenario (reuse, recycle, landfill, or incineration), select or avoid materials so that you can meet environmental compliance regulations such as RoHS or WEE, and you can even determine the most cost-effective manufacturing method for the material you want to use. In other words, DFMA with DFE means that you can simultaneously reduce unnecessary component costs, make products robust, achieve environmental compliance, and optimize your manufacturing and assembly processes from the get go. That is the right way to go green and to make more green, in my opinion.
One last thing. I had the pleasure of being an invited guest at last year’s DFMA conference. This year’s conference is in June. If you can get yourself to Providence for it, go and learn from the people who leverage DFMA for their competitive advantage.
You can read full details on DFMA 2009 with Design for Environment in today’s Pick of the Week write-up. A link to the conference information is there as well. Sign-up and download some of the webinars or articles on DFMA while you’re there. DFMA 2009 with Design for Environment is really one you do not want to miss
Thanks, pal.—Lockwood
Anthony J. Lockwood
Editor at Large, Desktop Engineering Magazine
Subscribe to our FREE magazine,
FREE email newsletters or both!Latest News
About the Author

Anthony J. Lockwood is Digital Engineering’s founding editor. He is now retired. Contact him via [email protected].
Follow DE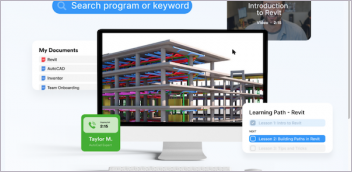

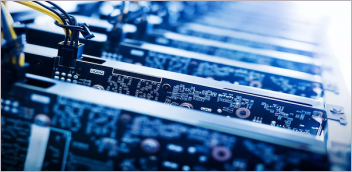
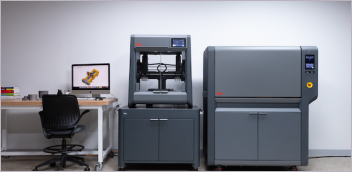