
Latest News
February 1, 2015
Great British Sports Cars, a specialist sports car manufacturer, recently acquired a Hardinge Bridgeport 4-axis machining center, and is programming it with Edgecam to produce complex, high-quality components as part of its expansion and development plans.
The company manufactures up to 85 vehicles a year in kit form, and a number of factory builds, to order.
Around 2,000 components go into each car, and GBSC’s development plans include manufacturing the majority of those parts on-site. “It became clear that we couldn’t develop the car in the way we wanted to in terms of improving design and speed of production by continuing to buy some parts off-the-shelf, and sub-contracting others out,” says Richard Hall, director.
Producing More Complex Parts
GBSC consulted Engineering Technology Group, who recommended the Hardinge Bridgeport GX 1000 programmed with Edgecam. “Edgecam is the best CNC (computer numerically controlled) software for the complexity of the parts we want to produce as we take the company forward. We need to be able to do everything ourselves so we can rapidly develop prototypes,” says Hall.
He says the combination of the Hardinge and Edgecam is now moving the company in a new direction, with the goal of making virtually every component. They have started with shock absorbers, throttle bodies and inlet manifolds, and intend to program their new Hardinge GS 51 lathe with Edgecam as well.
“We’d made numerous improvements to the chassis, but the dampers that were on the market weren’t up to what we needed, so we invested in the Bridgeport and Edgecam to create our own damper,” says Hall. “It’s not only transformed the car, but we now supply that damper to other car manufacturers – they’re used on the Lotus Elise European Championship car which has been on the podium every round this season.”
And he says the throttle bodies would be impossible to make without Edgecam. “Some of the porting on the throttle goes from round to oval ... around a corner almost ... and it’s quite a sophisticated, complex shape.”
As they now design their components around the tooling and equipment, it reduces costs and improves quality, giving them economical manufacturing. “It’s made us more credible as customers and the motoring media see that we undertake all our own design and machining, making us a true British car manufacturer,” he says.
Each GBSC Zero model is built to individual specifications, with starter kits for Mazda and Ford engines. While there are a number of generic body parts, the manifold is engine specific, and Hall says using Edgecam means they manufacture the components using the same fixturing. “We can easily create parts using just one set of fixturing and tooling, by simply altering the machining face in Edgecam. It would be impossible to achieve these results without Edgecam.”
While most of their lathe parts are relatively simple 2D, he says it will still be quicker to program them in Edgecam. “As the company grows and we invest in additional CNC machines, Edgecam’s ability to program both milling and turning across a range of manufacturers will become increasingly more important.”
The company finds many of Edgecam’s features particularly useful, especially the speed of getting from the CAD drawing to a machine-ready program with toolpaths that ensure the correct tooling for the job, and preserve tool life. Design is undertaken with Dassault Systèmes’ SolidWorks, then the 3D model is imported into Edgecam, which creates the billet size, selects the tooling, finds the edges and holes and sets up the relevant machining strategy.
No Restrictions
“Edgecam means we have absolutely no restrictions on our manufacturing now, so we can expand our designs and build on the quality of our products, and make them look even better. It’s an absolutely integral part of our manufacturing operation and will help us expand into new products. Some of the complex components we’re intending to make would be impossible without it.”
GBSC ’s Marketing Director Ruth Hall says their investment in CNC machines and Edgecam gives them control over the manufacturing operation. “We have firm ideas about how we want to develop the company, and we and skilled staff,” she says.
Customers include colleges for use as student projects, and retired people, along with racing enthusiasts opting for the race option with full roll cage. A number of ‘track days’ are held at racing circuits around the country, where GBSC Zero owners compete against other.
“Our cars attract a lot of attention,” she says. “If you park one next to a Ferrari more people will gather round to look at it rather than the Ferrari.”
The company also runs the Kit Spares parts division, with over 700 products online, to suit the GBS Zero and many other makes, from kit cars to rally cars.
More Info
Subscribe to our FREE magazine,
FREE email newsletters or both!Latest News
About the Author

DE’s editors contribute news and new product announcements to Digital Engineering.
Press releases may be sent to them via [email protected].
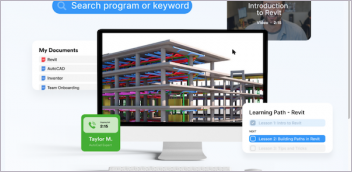

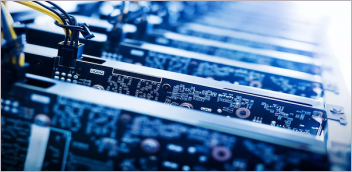
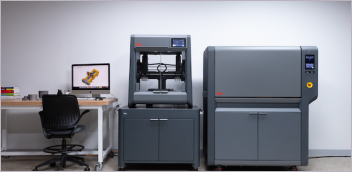