e-Xstream Engineering Launches Simulation, Virtual Manufacturing Offerings
The latest Digimat software enables businesses to simulate the 3D printing process and calculate total cost of producing each part.

Manufacturers can now CT scan a part and import the 3D RAW image to build a finite element model of its two-phase microstructure (e.g., carbon fiber-reinforced polymer) in Digimat and model its behavior. Image courtesy of e-Xstream Engineering.
Latest News
January 25, 2021
e-Xstream engineering, part of Hexagon’s Manufacturing Intelligence division, has introduced simulation and virtual manufacturing capabilities that enable users to analyze the production cost of polymer-based additive manufacturing parts against conventional processes, and continuously improve virtual engineering processes by validating the composite’s microstructure with computing tomography scans of manufactured parts.
The latest Digimat software enables businesses to simulate the 3D printing process and calculate the total cost of producing each part including the material use, employee time, energy and required post-processing steps.
Using this new tool, an engineer can take a holistic view of part production and finishing processes to determine the best process chain for production. It can also be used to perform batch optimizations to print as many parts as possible in parallel, increasing production capacity and reducing lead time.
It also can be used in production planning, to consider the total cost of ownership of machines and amortize those costs over the projected production volumes. This information is visualized for the user through plots and pie charts, so the cost breakdown can be easily analyzed for different scenarios.
Manufacturers can now CT scan a part and import the 3D RAW image to build a finite element model of its two-phase microstructure (e.g., carbon fiber-reinforced polymer) in Digimat and model its behavior. By embedding this validated material model in its computer-aided engineering (CAE) tools, a design engineer can perform analyses that account for variations within a manufactured part to reduce material use or avoid points of failure.
Connecting physical measurement with virtual testing also improves the accuracy of Integrated Computational Materials Engineering (ICME) processes when a new material system is introduced. The part performance can be compared to the simulated process to validate and certify the material model. CT scan validation also supports helps materials professionals refine the microstructure models they have built manually to improve the accuracy of future simulations.
When refining new manufacturing processes, users can capture information about the part, material, 3D printer or process used and their physical tests as they work using material lifecycle management. e-Xstream engineering’s MaterialCenter software captures a traceable, validated database of trusted material properties so that they can be used in the design phase of a product. Using material lifecycle management, information can be easily documented within multidisciplinary teams and shared throughout an organization capturing knowledge for reuse by authorized users.
Predicting the material behavior of a CT-scanned microstructure is a computationally intensive process, for example, it could take several days to analyze complex behavior such as creep using CPU computing only. By optimizing these processes for graphics processing units (GPUs), some tasks can now be performed interactively by the engineer because results are produced in minutes.
Benchmarks show the time required to analyze the stiffness of a material is reduced by 98%. This rapid solve time, combined with the introduction of a command line interface, also enables the use of Digimat finite element models within automated cloud-based optimization workflows on high-performance computing platforms.
When producing high performance structures such as aerospace components from composites, the progressive failure analysis (PFA) model makes it possible to define safety margins for a structure and make optimal use of expensive materials and processes. The latest version of Digimat performs these complex Camanho model analyses twice as fast, making it possible to perform a parametric study to define defect tolerances and maximize production yields.
Sources: Press materials received from the company and additional information gleaned from the company’s website.
Subscribe to our FREE magazine,
FREE email newsletters or both!Latest News
About the Author

DE’s editors contribute news and new product announcements to Digital Engineering.
Press releases may be sent to them via [email protected].
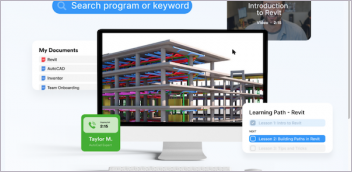

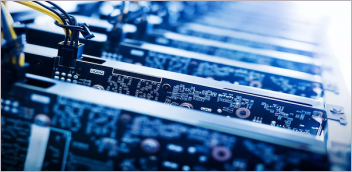
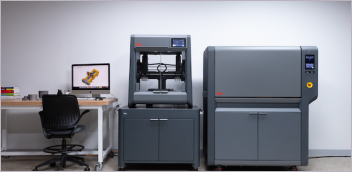