Latest News
December 21, 2012
By DE Editors
DP Technology is now shipping ESPRIT 2013, the latest version of its flagship software, designed to program multi-spindle, multi-turret mill-turn and Swiss-turn machine tools.
This latest version focuses on providing new and enhanced machining technology that ensures more efficient toolpaths and new strategies for greater overall productivity, the company says.
New to ESPRIT 2013, the patent-pending ProfitMilling strategy for 2-, 3- and 5-axis roughing cycles allows customers to remove more material in a shorter period of time. The ProfitMilling strategy optimizes engagement angle, chip load, material removal rate (MRR), lateral cutter force and machine acceleration to achieve optimal results. It utilizes trochoidal tool motion and a traditional offset of the toolpath, allowing usage of the full tool flute length.
Other upgrades include a new plunge setting added to the plunge turning (zigzag) cycle. Using a pre-plunge along walls reduces the tool load against walls and cuts wide grooves faster. A lateral feed-rate setting provides customers with more control and an option to perform extra-plunge along a profile to deliver fewer scallops for the finish pass. Also new are two new strategies for the “Diagonal Zigzag” groove type: “Thin-to-Thick Chip” for a progressive engagement of the tool, and “Thick-to-Thin Chip” that is suited to ceramic inserts. It generates rapid metal removal without vibration, as well as improved finish and prolonged tool life.
A new 5-Axis Roughing Cycle has been designed to quickly and easily rough a 5-axis part using the same familiar technology used to rough a 3-axis part, including the new ProfitMilling pattern. The 5-Axis roughing cycle automatically adjusts the orientation of any tool shape (end mill, ball mill, bull-nose mill) to keep the tool perpendicular to the underlying surface, thereby eliminating undercuts.
Also new to ESPRIT 2013 is a 5-Axis Port Machining Cycle dedicated to machining cylindrical apertures, and devised to cut as deeply as possible into a port while containing tool swings. This cycle is aided by an automatic recalculation of tool points along a spine curve.
The Impeller Machining Cycle now includes built-in re-machining, which allows for the complete machining of an impeller without concern for tool dimensions. The impeller cycle allows customers to machine as far as possible using the current tool before automatically stopping at the first unreachable level.
New collision-detection strategies have been added to all 3-axis and 5-axis milling operations, which detect collisions while toolpath is being calculated instead of during the simulation process. ESPRIT can be instructed to recommend the minimal tool length to avoid collision, or to automatically trim away the colliding toolpath and reconnect with appropriate links.
The new “Mid Surface” function can be used for blade machining, where it allows for the calculation of toolpath from a single source instead of multiple faces on the model, and controls the orientation of the tool axis throughout the cut, rather than on individual surfaces of the blade.
For more information, visit DP Technology.
Sources: Press materials received from the company and additional information gleaned from the company’s website.
Subscribe to our FREE magazine,
FREE email newsletters or both!Latest News
About the Author

DE’s editors contribute news and new product announcements to Digital Engineering.
Press releases may be sent to them via [email protected].
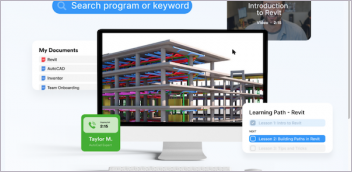

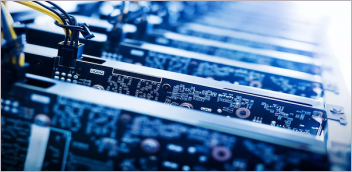
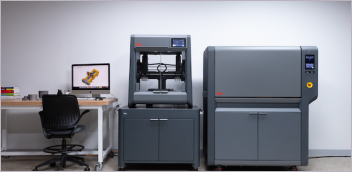