Direct Metal Comes on Strong
Metal parts and tooling take the spotlight in the additive processing world.
Latest News
August 1, 2005
By Pamela J. Waterman
Titanium. Tool steel. Inconel. If metal is your material of choice, now is the time to investigate direct metal manufacturing (DMM). Considered by some the holy grail of additive manufacturing technologies (aka rapid prototyping), DMM capabilities are now within reach.
Though no one sees DMM as a complete replacement for traditional processes, there are many cases where it does make sense:
• When the number of parts required is low or the design changes with each part
• When the geometry cannot be machined from one piece or at all
• When the process combines multiple parts into one
• When lead times with traditional processes are unacceptably long
• When the cost of wasted material (e.g., machining titanium) is extreme.
|
Solidica’s new Formation CT machine uses ultrasonic consolidation to bond ribbons of aluminum foil stock together to create molding tools and prototypes. |
DE recently spoke to six DMM vendors about addressing these needs.
Real Parts, Real Tools
Optomec in Albuquerque, NM, has commercialized the laser-engineered net-shaping (LENS) process developed at the US Sandia National Laboratories. LENS systems use a high-power Nd:YAG laser focused on a metal substrate to create a localized melt pool into which powdered metal is injected. Rapid cooling solidifies the deposit while the part is rastered back and forth according to a 3D CAD pattern. Features as small as 0.030 inches are possible.
LENS systems are marketed for both part manufacturing and tool repair with near net shape results. Company data shows material properties of LENS-processed metals are comparable to or better than those of forged materials, including 316 steel, Inconel 625, and Ti-6Al-4V. These properties allow designers to use thinner wall designs, reducing part weight.
|
The POM Group uses direct metal deposition for tools of different alloys. Pictured here is a mold and end product for automotive safety belt buckles. |
Other LENS applications include creating hybrid parts by building fine details on standard ingots or bar forms; adding anti-corrosion and wear coatings for industrial and medical applications; and even combining different materials for optimum temperature and strength combinations in a single part. The latter case has already been proven in a series of stem-valves subjected to extreme conditions in racing motorcycles.
Another company with a laser/powder deposition approach called direct metal deposition (DMD) is the POM Group in Auburn Hills, MI. This process employs a 3000W CO2 laser and three powder feeders to melt and deposit one or more metals on a pre-existing part, pre-form, or build-base.
“We get a true metallurgical bond,” says POM Sales Director Jerry Janson. “This isn’t just a plating or spray, and we produce 98 percent dense parts.” Uses include repairing worn tools and reconfiguring molds, as well as building entirely new parts.
Tim Gornet, manager of RPC Operations at the University of Louisville Rapid Prototyping Center, has used a POM system for more than three years. He says that one of the most interesting aspects of this process is that it allows “on-the-fly” alloy production, since each of the three powder-feed nozzles can supply a different material. “You can put a tool-steel coating on copper for excellent heat conductivity,” he notes, “or even mix metals and ceramics that are not usually machinable. It’s not a welding process, so there’s no distinct line that could lead to breaks.”
Different Approaches, More True Metals
Three other DMM methods solidify thin layers or beds of metal powder guided by a 3D CAD file, with each approach using a different binding process. EOS in Munich, Germany, uses direct metal laser sintering (DMLS) to fuse powder layers with a laser. 3D Systems in Valencia, CA, offers selective laser sintering (SLS) systems, which also use a laser, but in a two-step process. Lastly, ProMetal of Irwin, PA, now a division of Ex One, markets powder-bed systems based on MIT’s 3DP ink-jet technology. All powder-bed systems have the advantage of allowing parts to be built with overhangs, since the unused powder acts as a temporary support throughout the build.
|
Image courtesy EOS GmbH. |
The EOSINT M (for metal) series has two models, the 250 Xtended that uses a CO2 laser and the 270 with an ytterbium fiber laser. Morris Technologies, a service bureau in Cincinnati, OH, has been operating the first US-installed M 250 Xtended machine since 2003. The company builds both rapid metal parts and rapid injection mold inserts with this system. Depending on material, it achieves layer thicknesses as small as 0.0008 inch.
Greg Morris, President of Morris Technologies, describes the benefit. “When we design tools,” he says, “we take those inserts and make the complex part of the insert only, building on a thick piece of steel (stock). The ability to create complex metal parts in a very short time is of great interest.”
RP industry consultant Terry Wohlers, of Wohlers Associates in Fort Collins, CO, cites another recent EOS application: manufacturing hundreds of ski boot buckles for Tecnologia & Design, an Italian company. “The parts passed fatigue and impact testing and were indistinguishable from conventionally produced buckles. The company found that they could manufacture 600 sets of buckles faster and less expensively than with injection molding.”
3D Systems’ SLS machines use lasers to sinter a polymer binder on the metal particles and create a “green” part. That part is later infiltrated with bronze and heated again to achieve full density. Currently available materials are LaserForm ST-100 and ST-200 (420 stainless steels) and LaserForm A6, a mild tool steel. The newest SLS machine is the Sinterstation Pro with a build volume of 14,500 cubic inches. Features that both speed up the process and improve quality include closed-loop thermal control, a removable build chamber, a break-out station for removing parts from loose powder and an offline thermal station for preheating the build chamber. 3D Systems also markets the smaller (2,800 c.i.) Sinterstation HiQ (high quality) system in a base model or the HS version with a more powerful laser.
Time-savings and durability convinced U.K. pneumatic device manufacturer KV Ltd. to use an SLS system to make both injection-molded tooling inserts and final parts. In one example, KV designed and produced an injection tool in seven days, instead of the usual eight weeks required by traditional tooling. The company also took just three days to develop a metal part that required high strength performance, and produced them in batches of 360 for about $100 each. Traditional tooling would have cost $80,000 for the first eight pieces.
|
ProMetal offers three direct metal systems. This die started as a metal powder, but binders were sprayed from an inkjet print-head directed by a sliced MCAD file. Finally, it was sintered. |
ProMetal offers three direct metal systems. Its approach also starts with a powder-bed layer, but operates by spraying binder from an inkjet print-head to form parts based on the sliced MCAD file. Depending on the exact metal, the objects then undergo either a higher temperature sintering process or a light sintering plus bronze infiltration, creating fully dense final parts.
Typical layer thickness for the ProMetal systems is 0.004 to 0.007 in., with capabilities for printing at 0.002 in. resolution. The R2 model features an 8 in. x 8 in. x 6 in. build chamber and produces parts out of Inconel, true M4 tool steel, and three different stainless steel/bronze alloys. The RX-D is aimed at the dental industry and in beta-testing at several dental laboratories; technicians can produce half a dozen custom gold copings (part of a dental crown) per hour. ProMetal is currently working on securing FDA certification for the process. A similar, smaller R1 machine sells to the research and educational market.
|
These Solidica molds, produced via ultrasonic consolidation of aluminum ribbons, are for a retractable aerospace hinge. |
Solidica in Ann Arbor, MI, takes a very different but also direct approach to metal part manufacturing. The Formation 2030 uses Ultrasonic Consolidation to bond ribbons of aluminum stock to each other, while an integrated CNC machine cuts each layer’s edge to the MCAD file’s shape. Many customers, including the Department of Defense, are making sample aluminum parts as well as developing metal matrix composites particularly for thermal management purposes. Raytheon in McKinney, TX, has studied four methods for making parts that are traditionally done with QuickCast, and found that for more than 15 parts, it is less expensive to create Solidica aluminum tools and subsequent wax master patterns for each part.
Still a Tough Sell
Convincing people of the benefits of DMM may require looking at the entire design cycle. Gornet points out that although a tool produced by a particular DMM process may cost more than a traditionally machined tool, it can reduce overall manufacturing time or part cost or, in the case of custom medical parts, probably can cut down on operating room and patient recovery times. He adds, “We need to show people the cost benefits over the full product cycle; education is still very important.”
Contributing editor Pamela J. Waterman is an electrical engineer and freelance technical writer based in Arizona. Send Pamela your feedback on this article through e-mail by clicking here. Please reference Direct Metal September 2005 in your message.
SME Offers New DVD on Direct Metal Manufacturing
In June 2005 the Society of Manufacturing Engineers produced a 30-minute DVD called “Direct Metal Manufacturing,” scripted by RP industry expert Todd Grimm. Talking with representatives of the four featured companies, Grimm said they convinced him that DMM is now a real process, though widespread adoption is still years away. One example shows Morris Technologies producing eight unique parts within one week for a customer’s trade show deadline. With an EOSINT M 250 Xtended system, the parts came out in a little more than two days, compared to an estimated 10 days for CNC machining.
Another example cited describes how POM’s DMD process improved the performance of an injection-mold tool at its customer, the Hoerbiger Corporation. Oil leaks in a welded cooling jacket required them to pull a particular mold offline every two weeks for three days of repair. By contrast, a single core DMD replacement part has now been in operation for two-and-a-half years without requiring service, increasing on-time valve delivery from 10 to 90 percent.
Engineers at Synergeering Group in Farmington Hills, MI, and D-M-E’s MoldFusion Division in Madison Heights, MI, also discuss their successes using an ARCAM EBM machine with titanium and a ProMetal system with a stainless steel/bronze alloy, respectively. To order a video or DVD copy, visit the SME’s website. —PM
A Sampling of Direct Metal Companies and Methods
3D Systems Selective Laser Sintering
Accufusion Laser Consolidation
AeroMet Laser Additive Manufacturing
Arcam AB Electron Beam Melting
Concept Laser Laser Melting
EOS GmbH Direct Metal Laser Sintering
MCP HEK Selective Laser Melting
Optomec Inc. Laser Engineered Net Shaping
Phenix Systems Fiber Laser Technology/Laser Sintering
POM Group Direct Metal Deposition
ProMetal Ex One 3DP Printing
Solidica Inc. Ultrasonic Consolidation
Product Information
3D Systems, Inc.
Valencia, CA
Arcam AB
Gothenburg, Sweden
D-M-E Company
Madison Heights, MI
EOS GmbH
Munich, Germany
Morris Technologies, Inc.
Cincinnati, OH
Optomec, Inc.
Albuquerque, NM
POM Group
Auburn Hills, MI
ProMetal Ex One Co.
Irwin, PA
Solidica, Inc.
Ann Arbor, MI
Synergeering Group
Farmington Hills, MI
T.A Grimm & Associates, Inc.
Edgewood, KY
Wohlers Associates, Inc.
Fort Collins, CO
Subscribe to our FREE magazine,
FREE email newsletters or both!Latest News
About the Author

Pamela Waterman worked as Digital Engineering’s contributing editor for two decades. Contact her via .(JavaScript must be enabled to view this email address).
Follow DE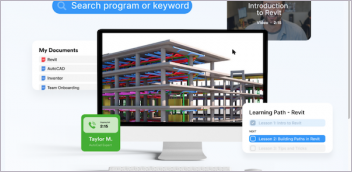

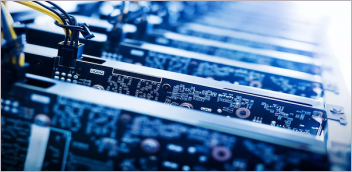
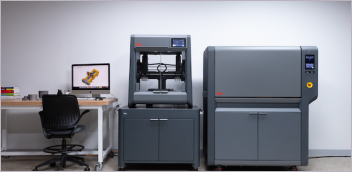