Latest News
January 1, 2016
Based at Sheppard Air Force Base in Wichita Falls, Texas, the Trainer Development Flight (TDF) is a facility that designs, develops and manufactures trainers and training aids for the Air Force and all branches of the Department of Defense (DoD) as required. These items are used in numerous training environments, including avionics, weapons and fuel systems, medical readiness, HVAC (heating, ventilation and air-conditioning) and telecommunications systems.

The trainers and training aids may be either original products or replicas of existing ones, depending on the training need. Some devices are not required to be working units, so it usually isn’t cost-efficient to purchase the actual item. For most training applications, it’s more economical to train students on replicas, instead of the often extremely expensive equipment.
The TDF uses direct digital manufacturing to fabricate a wide majority of its training products. To do so, it employs four FDM (Fused Deposition Modeling) additive fabrication machines in a centralized location with AFSO 21 (Lean) processes incorporated into the overall process.
Real Challenge
Before adding direct digital manufacturing to its processes, the TDF used conventional manufacturing methods to make its products. Conventional manufacturing typically requires longer lead times because there are often multiple steps, such as machining, lathe work, welding, sheet metal bending and cutting. A similar difficulty occurs when producing tooling to mold a part.
“Because most of our projects are either one-of-a-kind or very low volume, conventional methods become very expensive,” says Mitchell Weatherly, chief of the TDF. “Only about 10% of our work is for prototyping, and 90% is production.”
Real Solution
Before settling on FDM, the TDF considered “a multitude” of the other additive processes, says Weatherly. “With FDM, the investment is upfront, not ongoing,” he says. “The parts are durable, and they have the high level of detail we require. In addition, the process is environmentally safe and 100% ‘green’ with zero waste.”


The TDF is responsible for designing and manufacturing an exact replica of an unmanned aerial vehicle (UAV) or “drone” for training repair technicians. It has built a variety of internal and external components using its FDM machines. The components included most of the body components as well as several cowlings, propellers, and antennas. They also purchased a number of real UAV components from the OEM (original equipment manufacturer).
Real Benefits
Just for producing the UAV’s large antenna alone, using the FDM machines did the job in about one-tenth the time it would normally have taken with conventional methods, and it delivered a ROI (return on investment) of over $12,000. The savings go beyond time, though. For the antenna, it would have taken an outsourced machine shop up to 20 days to produce the part, where it took only two days using FDM — but only 15 to 20 minutes of labor. For the entire UAV project there was a total time saved of more than three years in some areas. This project, along with other trainer savings has been very impressive with an $800,000 cost avoidance over the last four years.
“Major advantages to the FDM system include its speed over other processes or alternative build methods, the versatility of FDM versus injection molding, and the ability to run multiple parts simultaneously through the system,” says Weatherly. Benefits include ease of maintenance, as well as the availability to use multiple materials for a variety of purposes. “Additional capabilities include the ability to design based on function needs instead of manufacturing constraints, and the ability to implement design changes immediately and at minimal costs. The versatility to manufacture any item coupled with zero hazardous waste is one of the greatest advantages to the Air Force,” says Weatherly. “The FDM-based machines have been used for a number of trainer projects which have tight budgets. We have also utilized the FDM process for research and development for our airmen and soldiers to be able to train like we fight.”

“For our first FDM machine purchase, we projected ROI in four years, but it took only 18 months,” Weatherly says. “For our second FDM machine purchase we saw ROI in only nine months. You will never get away from conventional methods and highly skilled technicians, but you can give them the proper tools and new technology that can make their job easier and competitive. I believe FDM is one of the technologically advanced premier manufacturing methods available. Since 2004, when we purchased our first of four machines, the FDM process has saved the government over $3.8 million to date with an expected 10-to-15-year savings of over $15 million.”
More Info
Subscribe to our FREE magazine,
FREE email newsletters or both!Latest News
About the Author

DE’s editors contribute news and new product announcements to Digital Engineering.
Press releases may be sent to them via [email protected].
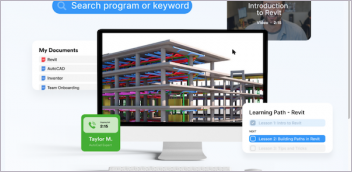

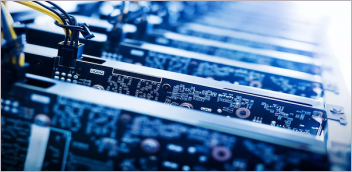
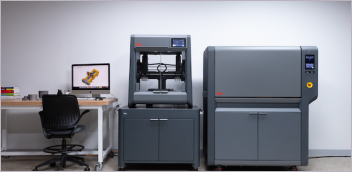