
These parts were produced on the M1 and are undergoing testing for end-use by Delphi. Courtesy of Carbon.
Latest News
June 2, 2016
3D printing entered onto the manufacturing scene with a whisper, rather than a bang. The technology slowly made its way into research facilities, quietly transforming the design cycle thanks to its rapid prototyping capabilities. Additive manufacturing’s (AM) slow burn continued until about 2012, when it began to finally attract attention from outside the lab as it began to transform into a valuable tool for end-use parts, while still retaining its value as a prototyping solution.
Along with increased attention, AM received increased funding for improvements to the technology, allowing a number of new players to bring new methods of 3D printing to the market. One of those players was Carbon, which relied as much on chemistry as mechanical precision to objects. Carbon claims its process is faster and more accurate than competitors, which Delphi, a Tier 1 manufacturer of automotive parts, is seeing for itself.

Delphi describes itself as company based on green ideas and connectivity for the automotive industry. It works with high-tech components on a daily basis, so it seems somewhat logical it should seek out high-tech solutions to its design needs. High-tech or no, people can be surprisingly low-tech with their decisions.
When Delphi began working with Carbon’s M1 printer, it primarily acted as a rapid prototyping system. Used in this manner, Delphi’s designers had the freedom to fail early and often. AM is amazingly fast when compared to the small run capabilities of traditional manufacturing methods, such as injection molding. Design iterations were completed in days, rather than weeks, and at a much lower cost than would have previously been possible.
Once the engineers examined the prototypes they were making, they discovered just how accurate these one-off designs really were, and began to explore the possibility of using them as functional prototypes.
”We’re excited to expand our work with the M1 to functional prototyping — something we haven’t been able to do until now — and to explore new manufacturing opportunities as a whole,” said Jerry Rhinehart, Delphi’s manager of additive manufacturing development. “It’s all about the materials and mechanical properties that we can achieve with Carbon’s technology. Traditional materials only provided about 50 percent of the mechanical properties we need to produce functional and final parts. We’re currently using the M1 on a project to install a batch of connectors and other electrical components into a 25-car fleet this June for road and validation tests.”
Delphi is now exploring the value of AM for low-volume batch runs, designed to appeal to small or medium-sized companies that might not be willing or able to fund the full cost of manufacturing similar parts using injection molding. Additionally, the company has begun testing 3D printed grommets, parts shields and electronic connectors as end-use parts.
Below you’ll find a video about the material options for Carbon’s M1.
Source: Carbon
Subscribe to our FREE magazine,
FREE email newsletters or both!Latest News
About the Author
John NewmanJohn Newman is a Digital Engineering contributor who focuses on 3D printing. Contact him via [email protected] and read his posts on Rapid Ready Technology.
Follow DERelated Topics
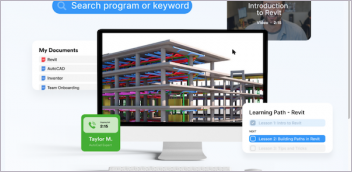

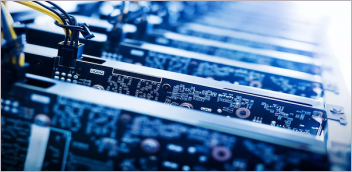
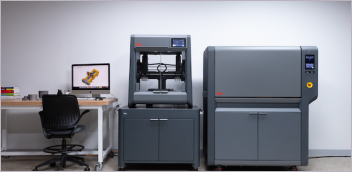