Latest News
December 24, 2013
Delcam’s PartMaker Division has released PartMaker 2014, which marks the introduction of Delcam’s Vortex high-efficiency strategy for area clearance into the PartMaker CAM suite. Other enhancements in the 2014 version include improved back-turning and 2D pocketing functionality, support for additional tool types and faster programming of lead-in and lead-out moves, and a new NC program viewer.
Vortex is Delcam’s newest proprietary high-speed roughing technology. It controls the maximum engagement angle of the cutter in the material, such that the angle calculated for the programmed stepover is never exceeded, even in internal corners. This allows for optimal cutting conditions to be maintained throughout the toolpath, the company says.
Vortex is available as a free upgrade to licensees of PartMaker’s Advanced Surface Machining (ASM) module that are on maintenance.
PartMaker 2014 includes improved functionality to support the automated programming of back-turning tools. These tools are used across a wide variety of small-part turning applications, particularly in Swiss machining. With their unique geometry and cutting characteristics, back-turning tools can eliminate the need for multiple tools and so can reduce cycle time and improve surface finish, the company says.
Another area that has been improved is 2D pocketing, which allows for more efficient and intelligent material removal from 2D pockets. The raster finishing strategy in PartMaker ASM has also been enhanced, resulting in less fragmented toolpaths without overlaps when machining highly complex shapes.
The lead-in and lead-out dialogs have been combined into one form where values can automatically be copied from lead-in moves to lead-out moves, or vice versa. A new option to make programming of more complex machines easier is the NC Program Viewer function. This allows improved analysis of the NC code generated by PartMaker to help achieve optimum productivity from the machine.
PartMaker’s tool database now includes explicit selections for tapered end-mills as well as neutral turning tools and back-turning tools. Additionally, the software now automatically gives users the option to choose between a flat-bottom, bull-nose or ball-nose end-mill when creating a new end-mill. The use of back-turning tools and tapered end-mills is available as a free upgrade to maintained licensees of PartMaker’s Advanced Tools option.
For more information, visit Delcam.
Sources: Press materials received from the company and additional information gleaned from the company’s website.
Subscribe to our FREE magazine,
FREE email newsletters or both!Latest News
About the Author

DE’s editors contribute news and new product announcements to Digital Engineering.
Press releases may be sent to them via [email protected].
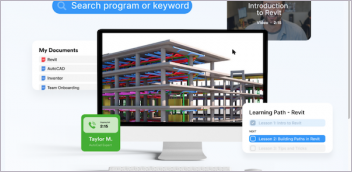

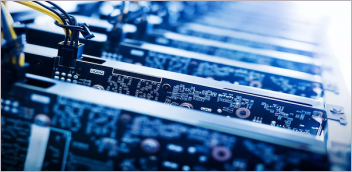
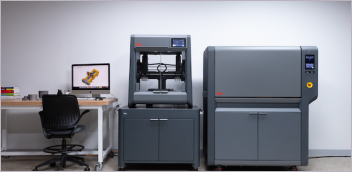