Latest News
September 1, 2005
By DE Editors
According to Delcam (Windsor, ONT), PowerMILL 6 has set a new standard for CAM, including new functionality for 2-, 3-, and 5-axis machining, plus a number of significant changes to the user interface to improve ease of use. Toolmakers and manufacturers using other complex machining operations for things like aerospace structures, blades, engine ports, and composite components should all benefit.
|
PowerMILL 6 includes a new plunge finishing option for five-axis machining of engine ports |
A new 2D Machining Wizard has been added to provide an easier and quicker way to generate 2D toolpaths covering all stages for working with both 2D wireframe geometry and imported 3D CAD models. The Wizard covers all the steps needed to create the machining model from the profile. Items like slots, pockets, and bosses can be created with or without a draft, and either based on specified data or with reference to previously defined features. Once the model is complete, the full range of roughing and finishing options can be selected.
Other features of the new version include functionality to create either custom drilling methods or use supplied templates; automatic feed rate slowing when approaching the bottom of a hole; improvement of machining of flat areas to keep total number of machining operations to a minimum and give a smoother surface finish; new plunge milling strategies where each plunge is calculated from a stock model that is updated after every cutting operation; and a new area clearance sorting option to keep the number of air moves to a minimum.
Also new is the default thickness command. It can be applied to features such as clamps or fixtures that must be avoided, or to thin walls where extra material must be left on to avoid bending the section during rough machining. For all machining operations, the stock model can now be shaded as well as displayed in a wireframe mode to make it easier to visualize the amount of material that still needs to be removed when undertaking a series of operations.
Many new options have been added to the program’s 5-axis capabilities. Support has been introduced for tapered tools; swarf toolpaths can now be created from wireframe profiles as well as from surfaces; automatic collision avoidance has been added to change the tool axis when collisions might occur; and a special technique for 5-axis plunge finishing can be used to mill along a surface rather than across it.
For more information, visit delcam.com.
Subscribe to our FREE magazine,
FREE email newsletters or both!Latest News
About the Author

DE’s editors contribute news and new product announcements to Digital Engineering.
Press releases may be sent to them via [email protected].
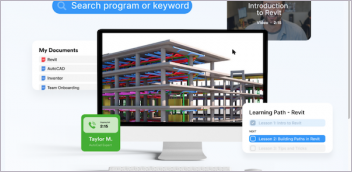

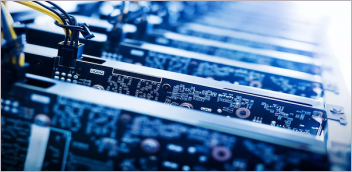
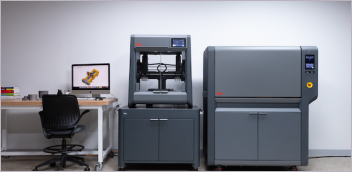