
Byrun is equipped with electro-pneumatic hybrid legs and upper body for fully mobile walking and running. Image courtesy of Maplesoft.
Latest News
June 1, 2015

In movies, robots can walk, talk and even pretend to be human. Their real-life counterparts are considerably more limited. But this gap is closing, and Engineered Arts, a UK robotics company, is seeking to bring reality closer to fiction.
Engineered Arts’ current flagship product is RoboThespian, the robotic actor. A full-sized humanoid with a biologically inspired design, RoboThespian is used by research and education centers the world over, to inform, entertain and investigate new developments in robotics. Institutions in over 20 countries, including NASA Kennedy Space Center (USA), Gazientep Planetarium (Turkey), Questacon Science Center (Australia) and numerous universities worldwide are using RoboThespian every day.
Maplesoft technology was used in the design and modeling of balancing and talking RoboThespian robots. MapleSim, the system-level modeling and simulation platform from Maplesoft, helped design the biologically analogous humanoid robot leg integrating a novel actuator, studying its static and dynamic stability, and building the designed leg to determine strategies for its control. However, RoboThespian, for all his conversational appeal, is largely static. His legs are powered, but he can merely squat and stand in place, never moving from a fixed location.
A New Type of Robot
Enter Byrun, the latest Engineered Arts endeavor. Using MapleSim, Byrun’s designers and engineers have developed a biologically analogous leg design that will give Byrun the ability to walk, run, jump and hop. Byrun will be a new kind of full-scale dynamic humanoid that will take social robotics to the next level. With a faster, stronger, more dexterous upper body, a virtually infinite array of facial features (courtesy of his projective head display), and the same speaking and singing abilities as his predecessor, RoboThespian, Byrun has the potential to revolutionize human-robot interaction.
“In Byrun, we want to integrate more human-like dynamics into the mechanical design. Using a human-inspired approach at a hardware level makes walking, running and jumping possible without rigid, robotic-looking motion,” says Guillaume Hirohide Sasagawa, engineer at Engineered Arts. MapleSim assisted in Byrun’s design by allowing engineers to simulate complex, nonlinear, compliant components such as his pneumatic muscles and parallel springs. These are used for safety compliance, shock absorption, energy efficiency and human-like smooth motion curves.
Engineered Arts specializes in unconventional actuation solutions, chosen to best suit the application. Motors are fast and precise, but inefficient and rigid. Pneumatic actuators, on the other hand, are powerful and energy efficient, but difficult to control. The conventional approach in robotics is to use a single actuator for a single joint – Byrun will use a parallel electro-pneumatic design, where multiple actuators control single joint actions. This approach utilizes the best facets of both types of actuation, while compensating for their drawbacks. Conversely, some actuators will generate coupled motion across several axes, to imitate (for example) the organic design of the human shoulder. This makes for more natural-looking motion, but can be potentially difficult to control. Here, once more, Maplesoft provides advanced solvers that can tackle the difficult multi-variant control equations used to develop Byrun’s motion algorithms.
Software-based Prototyping
By creating virtual prototypes of each design phase in MapleSim, Byrun’s engineers can investigate the feasibility of mechanical solutions without needing to create a laborious series of prototypes. “The software helps us to create the design parameters in a very fast virtual environment,” says Sasagawa. “We are no longer required to rebuild the robot for every design iteration, which saves us significant time and cost, and allows us to explore more radical options. As well, complex kinematics can be easily simplified with the use of Maple – this is a powerful tool as the resources required for the project are considerably reduced.” Byrun’s hardware requires modeling mechanical, electrical, thermal and pneumatic elements – with the help of the simulation tool MapleSim, the component requirements can be largely anticipated in advance.

The team at Engineered Arts has also found MapleSim useful for its ability to simplify complex calculations. “MapleSim’s ability to automatically generate complex mathematical models, such as the leg dynamics, is outstanding. Different parameters can be altered at different stages to reduce the complexity of calculations,” Sasagawa says. “In the case of Byrun, we were able to dramatically simplify the leg dynamics, making the computations much faster. This is extremely powerful and has real impact on our project timelines and deliverables.”
In addition to designing Byrun’s electro-pneumatic hybrid legs and upper body for fully mobile walking and running, the engineers at Engineered Arts are also developing a robotic hand with the same principles, creating a compact, highly efficient compliant manipulator. They have designed an elbow joint with unconventional kinematic characteristic in humanoid robotics with electro-pneumatic parallel actuation, and are currently making a full torso-shoulder-arm model in MapleSim. This model will be used for solving forward kinematics, inverse kinematics, end-effecter dynamics and compliance.
Robots like Byrun are setting a new standard for both humanoid and more general robotic design. “To be worth its cost, this robot must perform something never seen before. If it can do just 10% of John Travolta’s walk, Margot Fonteyn’s dance and Julia Roberts’ smile, we have a winner,” says William Jackson, director of Engineered Arts. “Achieving these goals is a daunting task. We are creating not just an exciting piece of hardware, but one that will make a great development platform for others to build on. When Byrun takes his next step, so shall we.” Maplesoft Engineering Solutions will continue to be part of every step taken by this revolutionary team of robotic engineers.
More Info
Subscribe to our FREE magazine,
FREE email newsletters or both!Latest News
About the Author

DE’s editors contribute news and new product announcements to Digital Engineering.
Press releases may be sent to them via [email protected].
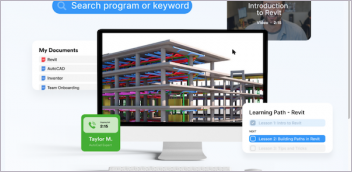

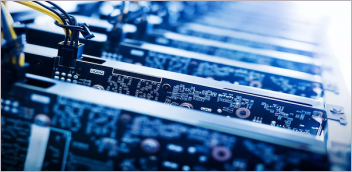
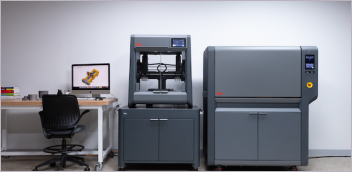