Latest News
October 8, 2010
By DE Editors
CoreTech System has announced the latest release of its plastics design and analysis software version for injection molding simulation: Moldex3D R10.0. This release provides several new functions to assist part and mold designers to optimize their product design with fast computation and 3D simulation results.
“Moldex3D R10.0 combines an interactive platform, powerful automatic meshing, parallel computing, and fast feedback of the design for all designers and CAE specialists at every stage of the product development. It integrates your innovation, efficiency and productivity to reach your design expectation and product optimization,” says Dr. Venny Yang, president of CoreTech System, “The ability to have better simulation results and accurate predictions encourages more effective product cycle management and increases profitability at the same time.”
With the newly improved workflow on Gate, Runner and Cooling Wizards, Moldex3D R10.0 provides a platform to facilitate the pre-processing work while increases users’ productivity and efficiency at the same time. Moreover, the mesh generators are generally two to three times faster, according to the company, because they use the multi-core architecture of modern CPUs.
This version enhances supports of crystalline polymer with high cooling rate characteristics to better estimate packing, warpage, and volumetric shrinkage. Expanded viscoelasticity models improve predictions of residual stress and optical performance. At the same time, heat transfer coefficient (HTC) change at different molding stages and heater-sensor coupling are added to improve the warpage prediction with more reliable moldbase temperature distribution. As for reactive materials, reactive injection molding (RIM) modules support Scorch Index calculation to avoid premature vulcanization. The IC Packaging modules include various drag force models for wire sweep analysis. Both of them support mold thermal analysis to improve mold heater design.
Improving user experience has been the major focus of Moldex3D R10.0. The rendering efficiency for graphic performance of Moldex3D/Shell Project has been enhanced by two to three times, according to the company. The Copy Run Contents command allows users to copy partial or full run data to save disk space and copy time to build another run for simulations. Moreover, the analysis result files have been changed from ASCII to binary to reduce 40 to 50% of the project file size, according to CoreTech. Moldex3D R10.0 is also ready for private cloud computing. The remote computing enhancements enable users to submit, schedule and prioritize analysis jobs from the client computers to the remote computing farms through network, and completed jobs will be auto downloaded to the client ends.
Moldex3D R10.0 also introduces new modules, Injection Compression Molding (ICM) and Fluid-Assisted Injected Molding (FAIM), to simulate the 3D molding phenomena in these special injection molding processes.
Building on the former integration with ABAQUS, ANSYS, NASTRAN, MARC and LS-DYNA, Moldex3D R10.0 extends its integration with CODE V. CODE V can read in deformed shape and refractive distribution predictions from Moldex3D for necessary corrections.
For more information, visit CoreTech’s Moldex3D site.
Sources: Press materials received from the company and additional information gleaned from the company’s website.
Subscribe to our FREE magazine,
FREE email newsletters or both!Latest News
About the Author

DE’s editors contribute news and new product announcements to Digital Engineering.
Press releases may be sent to them via [email protected].
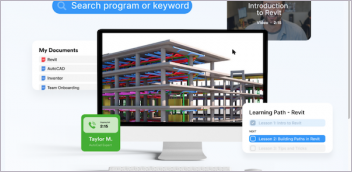

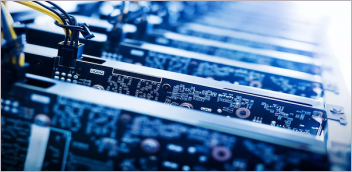
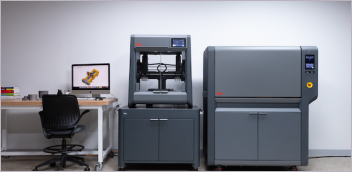