Connecting Service to Design
Digital twin technology provides a bridge from design to service engineers in the field.

PTC allows customers several ways to take advantage of augmented reality, including connecting to manufacturing data. Image courtesy of PTC.
Latest News
November 10, 2020
Terex Corporation manufactures lifting and material handling equipment for a global customer base in utility construction and industrial services. Each customer requires some level of product customization, which means Terex has to directly engage the customer during design review. For years this has been done with 2D CAD drawings shared as PDFs. As a user of 3D CAD internally, Terex found the process was becoming increasingly cumbersome.
“We want customers to have better interaction with the model” before the product is built, says Kyle Wiesner, Terex engineering manager. But most of them don’t have SolidWorks, the 3D CAD software Terex uses. “We spend a lot of time and money traveling onsite or waiting for back-and-forth communications on a 2D PDF via email or FTP,” he adds.
After reviewing options for improving its customer collaboration, Terex decided to focus on enabling customers to review and directly comment on 3D models without having to update their internal design tools. Terex selected Vertex, a cloud-based collaboration suite that uses the digital twin concept to create a zero-install software environment for manufacturers and customers to collaborate on design or service issues. Vertex supports all major 3D CAD formats, and provides direct import and customizable application programming interfaces to link to CAD and product lifecycle management (PLM) systems.
“Interactive 3D models give us and our customers a way to better communicate rather than needing to rely on a 2D drawing,” says Ryan Kloos, a sales application supervisor at Terex.
“Seeing the location of different components in proximity is very hard for the untrained eye to do on a 2D PDF,” Wiesner adds. “The ease with which we can now share 3D models minimizes complexity by giving the customer a more thorough opportunity to review designs.”
The Vertex Software collaborative platform is one example of the new wave of using the digital twin in customer relations, for initial design collaboration and for ongoing service.
Service and Design Integration
As part of the larger evolution to Industry 4.0, manufacturers and their software vendors are evaluating ways to connect design with service operations. There are multiple goals, including providing feedback to design for future iterations or immediate updates to existing products, allowing field service access to the current and accurate state of the product, and monitoring part and product performance in real time.
The value of closely integrating design technology with service operations is not about being trendy with 3D technology, says Josefina Sonnerup, an industry solution manager for intelligent equipment at Dassault Systèmes. It is a cost issue.
“If you have to fix something in the field that happens over and over, maybe it is a design issue,” she says. “It is important to see issues as early as possible. Scalability of testing in the virtual work during the engineering phase really integrates service operations into design. The virtual world improves the real world. Our customers already have 3D and PLM. It makes sense to extend that model into the field.”
Customers need the virtual twin as much as the manufacturer, she adds. “It makes it easy to just point and say, ‘I want this part’ and have the data.” Such use of digital continuity allows “serialized information in the field and part data in the office.”
Initial Vision
Using the digital twin to drive service processes was always part of the initial vision for the technology, says Dr. Michael Grieves, the researcher who first coined the term “digital twin.” In the early days of his research for automotive companies, and now as chief scientist for advanced manufacturing at Florida Institute of Technology, Grieves says too many manufacturers have backward thinking about how a digital twin is developed and how it should be used.
From the very beginning, “we were looking at usage in service, using both a physical version and a virtual one,” Grieves explains.
The change requires “moving from functional-centric to product-centric engineering,” he says, and populating the product digitally in the model first. “It is clear—at least, it is clear to me—the digital twin precedes the physical,” instead of creating a digital twin after the fact. “It was always intended that the digital twin would be in the entire product lifecycle.”
The CAD model is only one aspect of what makes a digital twin, Grieves says. “Behavioral simulations are more important than geometry. Just because you have a pretty picture doesn’t mean you have a digital twin.”
CAD-neutral PLM vendor Aras echoes the sentiment that the CAD model is only one aspect of a digital twin for service operations.
“Our customers are starting to capture configuration at the completion of manufacturing,” says Jason Kasper, an Aras product marketing manager. One major manufacturer of alternative power generation equipment equips turbines with sensors, which send data back to the manufacturer as well as the customer. The data is used in service operations and to help the manufacturer plan the next product iteration.
Leonardo Helicopter uses Aras to capture part configuration data for each helicopter they ship, tying all data to each tail number. Syracuse Research Corporation (SRC) created a Return Material Authorization form in Aras. The form automatically serializes equipment. When a part or a complete product comes in for upgrade, SRC does a visual inspection and adds the data to the virtual twin.
Kasper says another Aras customer connects a visual interface of a robotic arm that “connects the original digital thread to the component level” of the robot. “They can diagnose and create a service bulletin from the manufacturing data, telling the customer how to fix the problem.”
Then, the manufacturer’s quality control department can see where all the affected digital twins are, across all customer accounts—and generate a recall report or provide data for an engineering change request. “It connects the workflow and the related performance of the digital twin,” Kasper adds.
Orchestrating Engineering and Operations
Siemens has included service lifecycle management in its industrial software portfolio for many years. “Our strength has always been product configuration, understanding how an asset or a plant is configured,” says Yishai Barak, director of service lifecycle management, at Siemens Digital Industries Software. “But this is not the same as service operations. Without consideration of the physical asset in the digital model, you don’t have the full story.”
Siemens then retired a few software products from their order book and set about to create a service operations platform that combined partnerships with homegrown software “to cover the breadth of the service lifecycle,” Barak says. “We needed to have engineering and operations as one orchestrated organization.”
Echoing Joy’s Law—no matter where you work, most of the smartest people work somewhere else—Barak adds, “whatever resources we have in R&D will never be enough, not all the wisdom is in house.”
Siemens now offers a digital thread for service lifecycle management connecting to a comprehensive digital twin “to provide design insights and data to the field,” says Barak. Siemens made an equity investment in Australian software developer PHM Technologies for their MADe software—Maintenance Awareness and Design. Barak says MADe improves design by linking field data to the design model.
Barak notes there are three separate Bills of Material (BOMs) in use: the engineering BOM, the manufacturing BOM and the service BOM. The engineering BOM can show the engine as a single unit. But the service BOM must focus on parts. “We keep everything at the granular level [for the service BOM], keeping all possible configurations of the asset,” says Barak.
The data can be used to generate both as-built and as-maintained models, keep track of product use history, the serial numbers of replaced parts and more. “The information a tech needs in the field always corresponds to the up-to-date configuration.”
Today’s software opportunities for design-to-service are the “realization of digital thread ideas from a few years back,” notes Barak. “This evolves over time, a digital thread that is based on the single source of truth that allows different disciplines to avoid being in silos and to collaborate and have bi-directional benefits.”
Creating Heterogeneous Feedback Loops
When Autodesk launched Fusion as a portfolio of design and manufacturing applications, the company sought to create a next-generation platform providing built-in feedback loops that are not dependent completely on Autodesk applications.
“Our customers deal with heterogeneous environments,” says Srinath Jonnalagadda, Autodesk vice president of design and manufacturing strategy. “They have complex systems and a very involved IT infrastructure. Based on industry best practices we believe there will never be one system that conquers everything.”
Vendors like Microsoft and Slack offer flow productivity apps, which take data from one or several apps and use it elsewhere, with little or no code. “This is an important thing” for manufacturing, Jonnalagadda says. “Coexistence and use of the data backbone, for connections that enhance the engineering experience.”
Connecting design with service operations is part of the expanded vision for Autodesk. Chemicals giant BASF uses Autodesk Fusion for plant maintenance and Inventor for plant design. Jonnalagadda explains the process using the hypothetical example of a failed bolt.
“The bolt is made in Germany. A guy with a tablet can view the Inventor data,” take that data and visualize in Microsoft HoloLens, and see how the data compares to the original data. “Data is hopping from place to place.”
“This is not traditional interoperability,” Jonnalagadda says. “For Autodesk, interoperability [in Fusion] is about using data in its current format, using it as is. This is not about IoT; it is about data and insights; using data to augment and enhance. Our customers want the data from the field for design choices, maintenance choices and operational choices.”
Connecting for Product Insight
Engineers “know everything about the CAD model, but know little about the physical model when it is in production,” says Paul Sagar, VP of CAD Product Management at PTC. “There is no data on how it performs, on what works and what doesn’t.”
For years, PTC has been assembling and building technology to connect the two sides and unite design and field service. One new product to come from this initiative is Creo Product Insight, which offers the ability to place sensors on the CAD model to act as the virtual equivalent of a physical sensor in the actual product. The sensors in the CAD model are then given a digital connection to their physical counterparts.
“Connecting physical and digital instruments is the start of the digital twin,” Sagar notes. “This helps engineers bring insights into performance, behavior and product use. It can guide engineers on future iterations.”
Sagar sees four important uses for Creo Product Insight. First, product validation can now use real-world data. Second, smart product design is improved by the ability to optimize sensor location as part of the design process. Third, iterative product design is improved by the use of real-world and real-time operations data. Fourth, the connectivity enables what PTC calls Creo-as-a-Service for autonomous, continuous testing.
“For example, if a product in the field shows a spike in a sensor reading, an engineer can create a workflow and run a simulation,” Sagar says. Using the data connection helps determine the next course of action.
PTC started showing off the use of augmented reality (AR) for field service several years ago, and continues to “close the loop” between the digital twin and the product. Sagar tells of a PTC customer who builds wind generation turbines. Each unit is a custom configuration.
By using the IoT-type connection between each field instance and the digital twin, the customer created a service guide that uses AR to provide detailed instructions that overlay on the CAD image.
“All the right data is in hand for a repeatable business practice,” Sagar explains. “This approach is becoming more popular due to the aging workforce” when less experienced employees are taking over responsibilities without years of product and service knowledge. “The work becomes more repeatable using AR as an assistant.”
More Aras Coverage
More Dassault Systemes Coverage
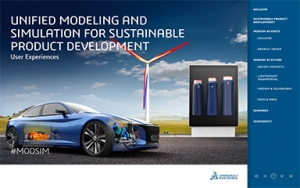
More PTC Coverage
More Siemens Digital Industries Software Coverage
Subscribe to our FREE magazine,
FREE email newsletters or both!Latest News
About the Author

Randall S. Newton is principal analyst at Consilia Vektor, covering engineering technology. He has been part of the computer graphics industry in a variety of roles since 1985.
Follow DE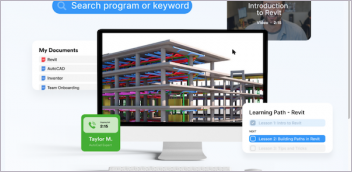

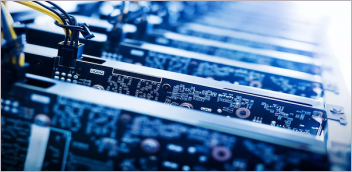
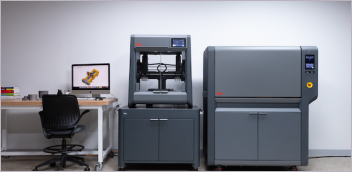