Configure Your Workstation for CAD, Step by Step

The Dell Precision Tower 3420 and 3620 are configurable for CAD and ISV certified. Image courtesy of Dell.
Engineering Resource Center News
Engineering Resource Center Resources


Latest News
February 2, 2018
Like placing one foot in front of the other, the continuous advancements in hardware and software are what move engineering productivity forward. Lose the balance between them when configuring your workstation for CAD, and you’ll be tripped up by overspending on hardware or underperforming on critical software tasks.
Configuring a workstation for CAD today is different than just a few years ago because CAD software has changed to keep pace with design engineers’ evolving workflow. For example, being able to run simulations or perform rendering without leaving the CAD program is now a standard feature. Complexity has gone from 2D to 3D to modeling systems of systems. CAM and design for 3D printing functionality is also baked into most popular CAD platforms.
The typical CAD user’s computing workflow extends beyond a single CAD application. Many design engineers are proficient in multiple CAD programs, viewers and translators to ease collaboration. Some also take advantage of stand-alone simulation and visualization tools geared toward design engineers, such as COMSOL Apps or the new ANSYS Discovery Live. Topology optimization and generative design tools are also becoming increasingly common in design engineers’ workflow. And, of course, there are the office applications, such as email, Excel and web browsers, all of which must be considered when determining the best workstation configuration for the best productivity.
Thankfully, workstation hardware continues to advance on a number of fronts, exceeding the needs of CAD users in many cases. It's gone from fast solid-state drives that have increased in storage while dropping in price, to new CPUs and GPUs, to monitors with high enough resolutions to make your eyes forget you’ve been cleaning up part geometries for 10 hours. And, because technological and workflow disruptions seem to be happening at an increasingly faster pace, CAD users need to decide what will be the best computing configuration two years from now, when next-generation technologies like augmented or virtual reality may be added to their responsibilities.
Whether you need help determining the right components, or help justifying why an engineering workstation needs to be configured differently than the PCs used in the accounting department, the steps below will guide you through the process.
Step 1: What is Your Workflow?
Step 4 & 5: Memory & Peripherals
Step 1: What is Your Workflow?
Begin by taking an inventory of the software you use and how often you use it. Check the recommended system requirements of each, not the minimum requirements. The minimum requirements are just that: the bare minimum needed for the software to function. Professional design engineers need their software to perform at the speed of thought. The recommended requirements will get you in the ballpark.
Hardware requirements can vary based on software application, usage and dataset sizes. To help you get detailed information on how your Dell workstation is performing and determine true requirements, use the Dell Precision Optimizer (DPO) tool Analysis reports.

When looking for hardware that meets those recommended requirements, focus your attention on software certification. Independent software vendor (ISV) certification of hardware is more than just a rubber stamp of approval that the software will work well.
“Thousands of hours are invested in certification to provide a stable and reliable platform for engineering applications,” says Dell’s Scott Hamilton. “Hardware and software vendors work closely to identify and fix problems before the user sees them, which makes the user experience much better and dramatically reduces downtime. ISV certification is important to dramatically reduce problems.”
Those problems could range from annoying quirks that combine to cripple productivity, to full crashes that can result in lost data.
“CAD software certification is one of many key reasons why enterprises rely on professional GPUs,” says NVIDIA’s Andrew Rink. “Manufacturing companies generally prefer to avoid the productivity losses resulting from graphics related CAD software performance issues or crashes that impact critical product design work by valuable employees.”
With all of the workstation improvements made in recent years, chances are exceedingly good that the recommended requirements of the software you use won’t be out of the range of modern, professional mobile workstations. The pros of going mobile are obvious: you can work on the road, in the upstairs conference room or at clients’ sites. The traditional cons continue to be minimized, but take battery life, screen size, upgradability, cost and performance into account.
Step 2: Pick Your Processors
Depending on your software requirements in step 1, it’s unlikely you need the latest central processing unit (CPU) or the most powerful graphics processing unit (GPU) for a typical CAD workflow. Opting for the previous generations of CPUs and GPUs can save some money that might be better invested in more RAM or storage. However, if your workload includes simulation or photorealistic rendering—or if it will in the near future—let that guide your processor choices.
“If all you’re doing is CAD, then a high clock speed, 4-core CPU is ideal,” says Hamilton. “If you’re doing simulation, go for more cores and possibly a dual-socket workstation. If you’re doing both CAD and simulation, then go for a configuration that has a high turbo boost and many cores.”
On the GPU side, most CAD software vendors recommend a discrete graphics card. Choosing among entry-level, mid-range and high-end graphics cards depends on the work you’re doing now and expect to be doing in the future, as well as the resolution you require.

“The sweet spot for traditional 3D CAD is a mid-range graphics card like the Quadro P2000 or P4000,” says Hamilton. “For GPU rendering, a Quadro P4000 or above is recommended, and multi-GPU configuration allows for extreme performance.
NVIDIA has posted benchmarks showing Dassault Systèmes SOLIDWORKS performance using different Quadro GPUs in desktop and mobile workstations here.
GPU-hungry applications such as photorealistic rendering and even augmented and virtual reality are growing in popularity among CAD users.
“The NVIDIA Iray rendering engine is natively integrated in numerous CAD tools, such as CATIA, SOLIDWORKS and Siemens NX,” says Rink. “That’s a big proportion of the CAD tools being used, so more and more engineers are being exposed to and getting comfortable with photorealism earlier in design. As a result, they can make better informed design decisions earlier in the design process.”
Rink recommends purchasing the most advanced technology your budget can afford to make your current workflow smoother and prepare for the future. “Even if you don’t currently render photorealistic images or perform simulation to optimize your designs, with the expanded availability of easy-to-use tools for that, you very well might begin to do so in the next year or two,” he says. “And model sizes continue to grow as product complexity increases, so it’s often worth buying a higher level professional GPU than you think you need today.”
Investing in the future now opens up more options for increased productivity. For example, designers can use one display for editing a CAD model and another to interactively display a photorealistic visualization. As the designer modifies the CAD model on one display, he or she can immediately see how it will appear in real life on the other display. Such a workflow can greatly improve productivity and reduce rework, but it does require a more powerful GPU to ensure very fast rendering, especially on 4K displays.
Step 3: Speed and Storage
The Precision Workstation Storage Classification paper provides an in-depth description of the different types of SSDs and how Dell classifies them via benchmarking. It can be downloaded here.
If you haven’t upgraded to a solid-state drive (SSD) by now, you don’t know what you’re missing. Having the operating system and applications boot from an SSD is a guaranteed productivity enhancer. SSDs do cost more per gigabyte than traditional spinning hard disk drives (HDDs), so if your local storage needs are great you might want to opt for a workstation that uses both—an SSD for booting and an HDD for storage.
However, not all SSDs are created equal. For example, “PCIe drives are much faster due to enhanced bus speeds capable of utilizing full performance of modern SSD technology,” says Hamilton. “The SATA interface is limited to 6.0 GB/s,” which can create a bottleneck.
“SSDs may have descriptive information in their product sheets, but it has become increasingly difficult to correlate SSD interface, flash memory type, and flash controller model to application performance,” according to the white paper “Precision Workstation Storage Classification,” which provides an overview of how Dell classifies storage devices for Dell Precision workstations. “SSDs provide significant advantages over hard disk drives, but without measuring drive model performance in some systematic way, it can be difficult to differentiate SSD models based on their ‘back-of-box’ specifications.”
According to Hamilton, users often underbuy when it comes to storage. “CAD and simulation files are fairly large, and take a long time to read and write,” he says. “What we’ve found in testing is that when you put in a faster storage system like an SSD, you get much better CPU utilization. If you can get that data faster, you get the processor going faster and see overall better performance.”
Step 4: Don’t Forget the Memory
One thing that hasn’t changed is that RAM delivers a great performance bang for your buck. For example, 8GB of RAM is recommended for SOLIDWORKS 2018, 16GB for Siemens NX and “20GB or more” for Autodesk Inventor. But a little extra doesn’t hurt the pocketbook much and can cure many ills.
When physical RAM runs out, Windows turns to virtual memory—a combination of RAM and a portion of your hard drive—to temporarily store files and swap back to the physical RAM when it is available. This swapping slows down CAD operations, so it’s best avoided by having the appropriate amount of RAM for your engineering work, plus some extra for everything else.
Running into RAM shortages is especially common as systems get older and software memory requirements increase. “If you want to upgrade later, then buy the highest density DIMMs (dual in-line memory modules) now and leave some slots open for future expansion,” Hamilton says.
If your workflow includes simulation, Hamilton recommends 4GB to 8GB of RAM for each processor core. “Error correcting code (ECC) RAM is good for simulation and analysis, but not really that important for CAD,” he says. ECC RAM is designed to detect and correct data corruption.
Step 5: Configure Your Experience
Two of the most important, but also most often overlooked workstation configuration considerations are the monitor and mouse. They are the fundamental means of interacting with your workstation, day in, day out. System requirements aren’t much of a concern when choosing mice, even those with programmable functions specifically built for different CAD applications. Monitors, on the other hand, can drive GPU considerations.
“The amount of GPU memory used by 3D CAD applications when viewing on 4K displays compared to using an HD monitor increases substantially, so users should be aware that they may need a GPU with a larger frame buffer, depending on the complexity of their models,” says Rink.
If your visual workflow goes beyond the monitor to include virtual reality, then you need “seven times more graphics performance than PC gaming” for an immersive VR experience, Rink says. “I recommend any product designer or engineer planning to bring immersive VR into their workflow ensure their workstation is configured with a Quadro VR Ready GPU, so that they’re guaranteed to have a smooth VR experience.”
Subscribe to our FREE magazine,
FREE email newsletters or both!Latest News
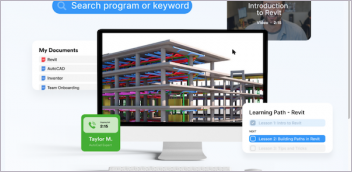

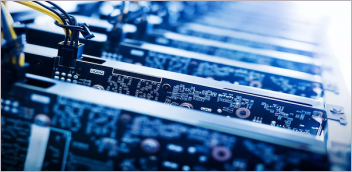
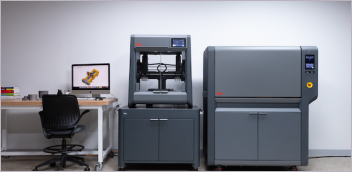