Latest News
March 1, 2005
By Dale Berry, Abaqus, Inc.
Advances in processor speed, new algorithms, and software tools forfinite element analysis (FEA) make it easier for analysts and designersto collaborate more often during the design cycle. Still, difficultproblems remain at the forefront of engineering practice. In thechallenging field of fracture and failure analysis, a group of industryleaders is adding its collective expertise to ABAQUS, Inc. to solvesome of these problems.
Members of the group include NASA, ExxonMobil, Intel, Cooper Tires,Boeing, Purdue University, MIT, the French aerospace company SnecmaMoteurs, and global energy and transport giant Alstom. Theseorganizations are guiding the development of new software for fractureand failure analysis. The scope of the effort reflects the extent towhich concern about the operational safety of structural componentscrosses industries.
Traditionally, simulating fracture and failure has been computationallyexpensive and impractical to perform on complete system models. It istypically done as part of product validation outside of the designcycle . Usually, the analysis focuses on a specific area of concern,such as the strength of a load-bearing riveted joint.
One new tool for modeling the performance of riveted or welded jointsis the compliant fastener. By defining a connection as compliant ratherthan rigid, analysts can model the performance of the joint closer tohow it actually behaves in the real world. In an automotive crashsimulation, for example, a rivet defined as a compliant fastener isable to shear or break. With joints modeled so much more realistically,the analysis can more readily identify design problems that compromiseproduct function.
Another development is the introduction of cohesive elements andvirtual crack closure technique (VCCT) analysis in commerciallyavailable software. Cohesive elements and VCCT make it possible tomodel detailed deformation and damage to adhesive layers between bondedparts. Much of the impetus for this technology comes from the aerospaceindustry, which is aggressively exploring the use of composites as alightweight replacement for metal components. Instead of joining partswith rivets, aerospace companies are now moving toward using bondedcomposites to create a well-integrated vehicle structure.
The move to composites is a big issue in fracture and failure analysis.For metallic structures, the failure mode is often plasticity, wherebythe material yields. A lot is already known about metal failure, andnonlinear plasticity modeling is common during the design cycle today.But the main failure mechanism of a composite structure isn’tplasticity, it’s fracture.
Fracture mechanics is basically the science of hunting down andevaluating cracks. Before the debut of cohesive elements and built-inVCCT, analysts who observed a crack in a model had to do a lot of extramanual work to determine whether the crack would grow. They had toevaluate the energy of the crack separately, update the model forpropagation, and perform the analysis again.
What’s different now is that these new technologies have the ability tomodel fracture, so they show crack growth and debonding in real timeduring analysis. The FEA software itself can efficiently evaluatewhether the crack is going to grow or not, which reduces analysis timefrom weeks to days.
The vanguard of fracture analysis is already thinking ahead, with thegoal of embedding the capability for modeling failure and fracturethroughout the analysis model, not just at specific points. Duringsimulation, wherever a failure occurs or a crack starts to grow, theanalysis toolkit would guide the user to areas of concern.
Ultimately, when full-system fracture and failure analysis moves intothe design cycle, late-stage retrofits should become of thing of thepast. You won’t have to wait until product validation to know yourdesign will work.
Dale Berry is the manager for engineering applications in the ProductManagement group for ABAQUS, Inc., where he has worked for more than 16years. He earned a Ph.D. in aeronautical engineering from PurdueUniversity. Send your thoughts about this commentary to[email protected].
Subscribe to our FREE magazine,
FREE email newsletters or both!Latest News
About the Author

DE’s editors contribute news and new product announcements to Digital Engineering.
Press releases may be sent to them via [email protected].
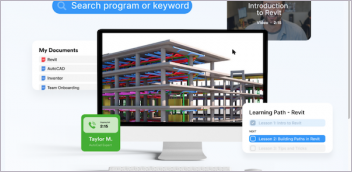

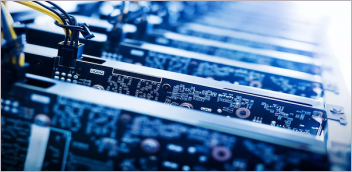
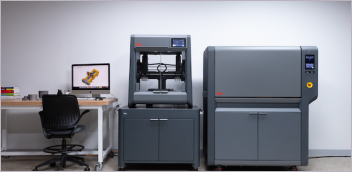