Commentary: July 2005
Adjusting to Today's Multi-CAD, Multi-Analysis World
Latest News
June 1, 2005
By Bob Williams, ALGOR, Inc.
There’s an increasing need among design and engineering companies to create and share designs that are drawn, reviewed, and revised in multiple CAD packages. Plus, these companies must study designs using any number of analysis and simulation packages. Just like the engineers we service, software providers are adjusting to this multi-CAD, multi-analysis environment by offering solutions that best integrate a wide range of tools with a customer’s existing design process.
Historically, design, analysis, and simulation software providers based their solutions on proprietary file formats, which lock in users, but make it difficult to work with other CAD and CAE packages. In addition, some FEA companies offer feature-limited tools embedded within specific CAD packages, requiring separate tool purchases.Now the trend is to use industry-standard plug-in architecture and open file formats to simplify sharing design data between applications. Leading software providers understand the benefit of letting engineers use whatever products they need.
|
Bob Williams, ALGOR, Inc. |
To support the analysis needs of today’s engineers, it is important to offer a full-featured, single user interface FEA tool that works seamlessly with all popular CAD packages and all types of analysis. ALGOR chose this route based on requests from users who work with multiple design tools. Our complete product line now supports direct CAD/CAE data exchange of parts and assemblies from Alibre Design, Autodesk Inventor, CADKEY, IronCAD, KeyCreator, Mechanical Desktop, Pro/Engineer, Rhinoceros, Solid Edge, and SolidWorks. Additionally, through an industry-standard plug-in architecture, our InCAD technology provides full associativity with most of these CAD packages—allowing engineers to make iterative design changes without needing to redefine FEA loads, constraints, and other data.
Users benefit from this approach because they learn and work within the same user interface regardless of their CAD package or analysis needs. This allows engineers working in multi-CAD environments to use just one interface. As analysis needs expand, users can choose advanced tools such as CFD and mechanical event simulation (MES) for combined motion and stress analysis; all in the same user interface that works associatively with MCAD.
Engineers choose to use multiple analysis tools or vendors to improve flexibility and productivity, obtain best-of-class technology or value, and create more sophisticated simulations. To realize these benefits, engineers must be able to exchange FEA model and result data with other analysis packages.
One way this is being achieved is by supporting popular FEA file formats. For instance, some FEA providers now offer support for NASTRAN input and output files. This allows companies using NASTRAN or NASTRAN-compatible products to benefit from the value-added capabilities of other analysis packages. In our case, users can work with the native NASTRAN input deck and result files directly within FEMPRO, our single user interface for finite element modeling, results evaluation, and presentation. This allows NASTRAN users to access our capabilities for full CAD/CAE associativity with popular CAD solid modelers; automatic, hex-dominant, hybrid solid meshing; and complementary analysis tools such as CFD and MES.
By integrating the analysis capabilities of multiple software providers, engineers can choose from a variety of FEA processors including specialized analysis tools such as acoustics, fatigue, and electromagnetics, all within the same user interface. This gives engineers the flexibility to choose whatever analysis type or combination of analysis types they need to get their products to market. Plus, it provides access to extensive results evaluation and presentation capabilities.
The use of industry-standard plug-in architecture and open file formats makes it possible to more easily move geometric and FEA data between packages. For engineers, the end result is increased flexibility and productivity—even within the multi-CAD and multi-analysis environments often involved in today’s design process.
Bob Williams is product manager of ALGOR, Inc. To contact him about this article, send an e-mail c/o DE‘s Editors.
Subscribe to our FREE magazine,
FREE email newsletters or both!Latest News
About the Author

DE’s editors contribute news and new product announcements to Digital Engineering.
Press releases may be sent to them via [email protected].
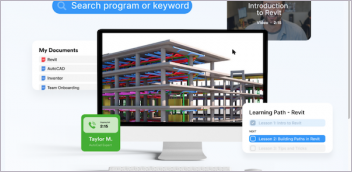

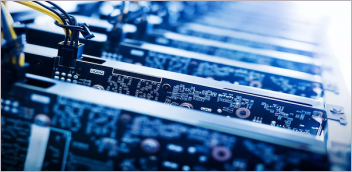
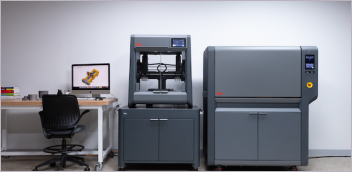