Latest News
April 1, 2005
Implementing New Methods in Old-School Technology
By Diane Landers, Delphi Corporation
In the early 1990s, as a member of the younger generation of automotive manufacturing engineers, I found that exposure to different areas of engineering and manufacturing gave me a pretty good view of how change is received in these environments. Back then, manufacturing plants seemed to be dominated by a hands-on, hard-working, do-it-the-way-it’s-been-done-forever mentality. Most younger engineers were trained and molded by these seasoned attitudes.
One of my first projects involved developing and implementing processes to help Delphi Steering’s very large, global supply chain work more efficiently. We needed to process design changes faster. So, a team of us developed a method for creating 3D associative process models to derive drawing information for manufacturing directly from these models. Successful implementation of this method would facilitate automatic propagation of CAD changes into process sheets and eliminate error and redundant modeling among process designers. Our team proved we had developed a method that worked and solved these problems, but we never realized a bigger challenge still lay ahead: implementation. How would we get manufacturing engineers to embrace this new process, which meant changing the way they did things?
![]() |
Diane Landers, Delphi Corp. |
I’ll never forget it. My boss and I went to one of our plants to present this new method. Just about every engineer in the plant was at that meeting. We presented an overview of our new method, and I could see disbelief written on each face. One older gentleman stood up and said, “I will never get anything done if I have to wait on the 3D CAD guy to get my work done! I can pay my design house to do it and they can have it back to me in a few days. This will never work!” Others agreed.
I fired up and ran the demo. People kept interrupting me with comments about learning curves, overloading their designer, and the like. Finally, I got to the part where I made a change to a casting part—similar to the parts they made at their plant. I changed the size of a boss on the casting and then opened the process sheet. These two files were associatively linked. I challenged the group: “I’ll make the production change to all 18 in-process models and drawings before you can get to the phone and call your favorite design house.” They snickered like I was nuts.
I clicked away and did it. No one said a word as their preconceptions were blown out of the water. The biggest winner: THEM. They didn’t have to spend any money to buy something new—just learn a new method of doing things.
Seeing is believing. We led with honey, not vinegar, and we showed them how our change would make life better, even for the old schoolers. Since then, we’ve done the same convincing in 13 other plants and divisions. Last year, more than 3,000 production parts used our design methodology and saved our company a lot of time and money.
You can have a great idea about how something should work when implemented, but you have to disprove the disbelief by thoroughly testing and retesting in a pilot production environment if it’s ever going to be accepted. Do that and you’ll keep your credibility, otherwise, you might as well be saying you can fly to the moon on a broom.
Diane Landers is an IT systems analyst specializing in CAD/CAM Technology Development for Delphi Corp., a world leader in mobile electronics, and transportation components and systems technology. She has more than 14 years experience in the automotive industry and holds four patents, with 11 pending. To contact Miss Landers about this commentary, send an e-mail to [email protected].
Subscribe to our FREE magazine,
FREE email newsletters or both!Latest News
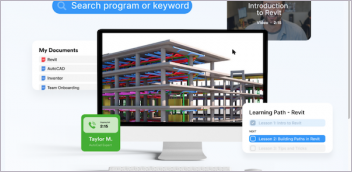

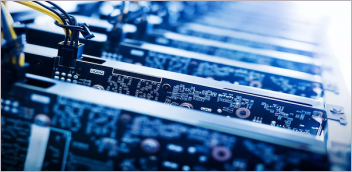
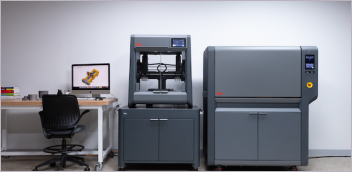