Choosing the Best AM Materials
Are you puzzled by the possibilities? Read on.
Latest News
June 1, 2013
![]() Surgical clamp “jaw” made using metal laser-sintering of 17-4 precipitation hardening stainless steel. The attachment point was machined for a precise fit. Image courtesy of FineLine Prototyping. |
You may be facing a similar, though amplified dilemma if you’re considering an additive manufacturing (AM) solution to part production. What factors are important to understand and consider when choosing the best material? DE asked a number of AM system manufacturers, material developers and service bureaus for their advice to prospective customers.
Material Properties, System Variables
Randy Stevens, operations manager at In’Tech Industries, says that because there are hundreds of AM materials from which to choose, asking three key questions can simplify the process:
- What’s the application?
- What are the features?
- How big is it?
A part that will be exposed to the environment (water, chemicals), for example, requires different material properties than a marketing model, which may differ from a part that will be hidden. Similarly, the need to see through a part will eliminate dozens of opaque possibilities.
With its experience operating multiple 3D Systems and Stratasys (Fused Deposition Modeling ]FDM] and Polyjet) systems, Stevens’ service bureau can guide you through creating that clear plastic part via three different approaches.
“3D Systems’ Accura ClearVue is the ultimate in clarity for optically clear parts, while Accura 60 has a blue tint, but a higher Shore D hardness and builds fast,” he offers. “And Objet VeroClear has a higher hardness and elongation at break.”
The company’s website features helpful charts, including a comparison of dozens of such material properties.
In the thermoplastic arena, Stratasys FDM systems offer 10 versions of functional materials, with varying properties of strength, biocompatibility, flame/smoke/toxicity (FST) certification and more. In addition, Stratasys Polyjet systems support material properties ranging from rubber to rigid and transparent to opaque. With Polyjet Connex technology, multiple materials can even be printed simultaneously in the same part.
Given the more than 100 possibilities, it’s no wonder that Fred Fischer, Stratasys director of materials and applications product management, suggests users first take a higher-level viewpoint of their project.
“We sometimes ask users whether they are taking a top-down or bottom-up approach,” says Fischer. “Users can prioritize the application requirements that are critical, ‘would like to have’ or irrelevant, and match them up to standard materials properties to find the combination that solves their needs. Or you can say, ‘OK, I’m going to use this material in my final product—now tell me which material best mimics it.’ That becomes more important on the Polyjet side of the business, where it’s either a plastic trying to mimic a metal or a resin trying to mimic a plastic.”
Prior to the company’s 2012 acquisition of Objet Geometries, Fischer authored a white paper on thermoplastics that points out key characteristics of FDM material types (see the Stratasys website).
More resources for evaluating multiple AM technologies and possible materials come from service bureau FineLine Prototyping on its technology-comparator and material webpages. Although the company does not offer part-production on all of the 11 listed plastics-based systems, the information is a good starting point for newcomers.
For customers with unusual applications, Rob Connelly, president of FineLine Prototyping, describes several ways his company’s services stand out in the material world. He says, “Our SLArmor is kind of a bridging step between a plastic part and a metal part. You want to get close to the properties of metal, but you don’t want to pay the full price of it. We make the part out of a ceramic-filled SL (stereolithography) material, very stiff and strong, then plate it with a structural thickness of nickel plating.”
Connelly also describes an exclusive modified SL material/process called MicroFluidic Fabrication that his company developed to replace parts typically fabricated on glass with an expensive photolithography process. MicroFluidic Fabrication produces complex wafers with a clear shiny top and bottom for proof-of-concept parts, for such medical applications as lab-on-a-chip.
If you get the chance to speak with Solid Concepts marketing director Scott McGowan, you’ll gain a wealth of information across the spectrum of six major AM technologies, all available at his company’s service bureau facilities. He’ll give you tips about the pros and cons of ultraviolet (UV)-curable plastics vs. thermoplastics, explain the nuances of thermal behavior between polyetheretherketone (PEEK) and polyetherketoneketone (PEKK) materials, and tell you which support materials are easier to remove than others. You’ll also find the Solid Concepts material webpage brings together information that would take you hours to find from separate sources.
Moving into Metals
Say you know a given part needs to be metal. Greg Morris, founder of Morris Technologies (now part of GE Aviation), notes, “With metals, as a very broadbrush statement, the material properties will be close to wrought properties. That is relatively significant, because the properties are generally much better than cast properties, thus giving engineers and designers more freedom to use the process.” The company runs both EOS and Arcam metal systems.
Morris adds, “Whereas in polymers it is easy to post-finish parts, in metals it isn’t as easy—and there are a variety of technologies and methods to improve the surface finish of metal parts. Those techniques should be taken into consideration, even in the design. Also, one needs to take into consideration post-thermal processing steps, which usually involve stress relieving, HIP (hot isostatic pressing), solution heat treating, etc.” He notes the last point differs from working with polymers.
FineLine Prototyping operates two Concept Laser Mlab systems that use a very small-spot laser to create MicroFine metal parts with fine features and high tolerances; the process works with two grades of stainless steel. Another multiple-technology service bureau, Forecast3D, gives a nice breakdown of material properties about the stainless steels and cobalt chrome it runs in its EOS direct metal laser sintering (DMLS) systems.
Just to mention some material providers, 3T RPD introduced AlSi10Mg, an aluminum alloy, in 2011, adding to its portfolio of Ti SS, Maraging Steel, CoCr and Nickel Alloy; LPW Technology sells metal powders for SLM and Arcam EBM systems.
Parameters, Post-processing & Payment
It’s sometimes hard to separate the material from the system and its operational parameters. Generally speaking, the slower the “print speed” of a material, the longer the build time and the more expensive the part. In’Tech’s Stevens notes that materials, build time and any desired post-processing all affect the cost of a part.
Neil Lehman, vice president at Advanced Laser Materials, gives a basic list of material properties that, while specifically for sintered polymers, could be important to understand for building any additive manufacturing (AM) part:
|
“All AM materials have different print speeds,” he adds. “Working with a service bureau is a good way to find out how to best achieve your desired results.”
EOS, maker of DMLS and polymer-sintering systems, started opening up some of its system operating parameters to allow users to define exposure and start values. More recently, the company expanded its Part Property Management function, offering both standard and custom parameter sets that help users balance such aspects as build speed and surface quality. System manufacturer SLM also offers application-optimized build processes.
Parts made with an AM process often need traditional post-processing steps. Mike Littrell, president at C.ideas service bureau, says, “All rigid thermoplastic AM materials can be sanded, tumbled, primed, metalized, etc., (plus) annealing can be used to increase the temperature capabilities of some. For projects that require parts that need to be under pressure, SLS versions are typically easier to seal then FDM’d pieces.” The company has been educating clients on AM procedures since 1998, so you have much to learn from their experience.
Carl Dekker, president of Met-L-Flo and a longtime expert in the AM field, also emphasizes finishes as a critical part of choosing materials. He notes that people often don’t include those steps in their budgets. Dekker’s company offers five finish levels, from basic, mold-ready and premium to photometric (Class A, in automotive terms) and custom, and he can tell you which materials are a little easier to finish and which are more of a challenge.
Unconventional (and Conventional) Approaches
Plastics and metals from system vendors aren’t the only games in town. Mcor Technologies wants you to consider using your own plain paper, with the company’s Selective Deposition Lamination (SDL) process, as an AM material choice for low-cost, full-color concept modeling in the early stages of a design. Mcor President Conor MacCormack says, “SDL parts can be used effectively for sand casting, investment casting and living hinges.” Service bureau BL3Dimension recently set up the first U.S.-based Mcor IRIS system ready for customer projects.
Clear AM Material Comparison | |||
Material | Accura ClearVue (3D Systems) | Accura 60 Plastic (3D Systems) | Objet VeroClear RGD810 (Stratasys) |
Tensile Strength ASTM.D638 | 46-53 MPa | 58-68 MPa | 50-65 MPa |
Tensile Modulus ASTM.D638 | 2,270-2,640 MPa | 2,690-3,100 MPA | 2,000-3,000 MPa |
Elongation at Break (%) ASTM D638 | 3-15% | 5-13% | 10-25% |
Flexural Strength ASTM D790 | 72-84 MPa | 87-101 MPA | 75-110 MPa |
Flex Modulus ASTM D790 | 1,980-2,310 MPa | 2,700-3,000 MPa | 2,200-3,200 MPa |
Impact Strength (lzod Notched) ASTM D256 | 40-58 J/m | 15-25 J/m | 20-30 J/m |
Heat Deflection ASTM D648 @66 PSI | 51’C | 53-55’C | n/a |
Heat Deflection ASTM D648 @264 PSI | 50’C | 48-50’C | n/a |
Hardness Shore D | 80 | 86 | 83-86 |
Glass Transition (Tg) DMA E | 62’C | 58’C | 52-54’C |
Water Absorption ASTM D570-98 | 0.3% | n/a | 1.1-1.5% |
Comparison chart of three clear plastic materials and their properties: two SLA resins for use on 3D Systems additive manufacturing systems and one photopolymer for use on a Stratasys Polyjet system. Chart courtesy of In’Tech Industries.
![]() Hairbrush built on the Stratasys Connex 3D printer, showing TangoBlack (flexible) material and VeroGrey (rigid) material, printed together at the same time. Image courtesy of Stratasys. |
An independent filament source is Taulman 3D, makers of white (RIT-dyeable) Taulman 618 and clear Taulman 645. People interested in making their own filament from pellets can do so by building the new open-source, award-winning Lyman Filament Extruder. (Author’s Note: See goo.gl/JZ9MK for a video about the extruder.)
Back in the traditional manufacturing world, whether you’re talking subtractive machining, injection molding or thermoforming, plastics have well-defined properties. Experts at service bureaus such as ProtoLabs point out simply that with its computer numerically controlled (CNC) equipment, “Your parts are machined from real blocks of plastic and aluminum.” ProtoLabs’ website notes the higher flexural and tensile property values displayed by machined and molded ABS test samples vs. those built in ABS material on an AM system (per independent lab testing, 2007).
System manufacturers such as Roland DGA also make valid points about situations where traditional materials can be more cost-efficient. For comparison data, see the company’s online report, “Rapid Prototyping: Hype vs. Reality” at goo.gl/opwx3.
However, AM offers ever-closer values for these properties, and achieves both geometries and material compositions that are not possible with conventional processes. As consultant Todd Grimm points out, “These advantages, for the most part, won’t be realized until there are fundamental changes in the way material properties are specified and in the predictive sciences.”
The past year has seen a tenfold increase in market interest in AM processes, which means many more engineers not well-versed in 3D printing have come to service bureaus, needing to learn from the experts. One great venue for asking detailed questions of vendors and fellow AM users is SME RAPID 2013, June 10-13. Consider, too, joining LinkedIn’s 3D Printing Materials Society group.
Contributing Editor Pamela Waterman, DE’s simulation expert, is an electrical engineer and freelance technical writer based in Arizona. You can send her e-mail to [email protected].
More Information
Subscribe to our FREE magazine,
FREE email newsletters or both!Latest News
About the Author

Pamela Waterman worked as Digital Engineering’s contributing editor for two decades. Contact her via .(JavaScript must be enabled to view this email address).
Follow DE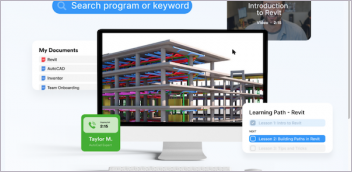

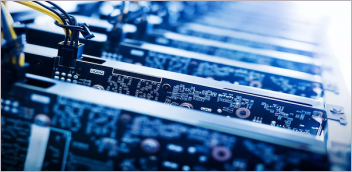
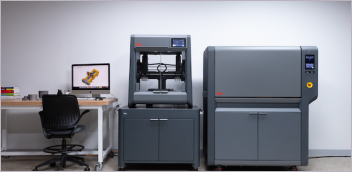