Medical Device Product Development on the Fast Track
Latest News
October 31, 2013
![]() |
Bumming around after college, I needed cash for pizza and other necessities so I latched onto a job as some sort of attendant at a facility for deaf and profoundly physically challenged kids. Best job I ever had, except the ultra-meager wages just barely kept me from making my home in my Chevy Nova. Plus, a place like that will rip your heart out.
Anyway, whether it was head trauma, nerve damage from some awful disease, or a birth defect, most of the deaf kids I worked with were not candidates for traditional hearing aids. Nonetheless, some of them were rigged up with abutments—gizmos implanted in near their ears—that enabled them to aurally sense something, not much, but something that unfolded a new world of possibilities for them. The modern age of bone conduction hearing solutions had yet to arrive, but, in retrospect, I probably witnessed the dawn of an end to the silence.
I thought of that wonderful place reading today’s Check it Out contribution, “Medical Device Product Development on the Fast Track: Sophono’s Alpha Hearing.” This customer story from the people at Tormach may be very short, but it’s long on showing you the possibilities of what you can do with the right tools and a little gumption to give something a go.
The piece’s protagonist is a guy named Todd Wyant. He’s a manufacturing engineer at a start-up medical device outfit in Boulder called Sophono. Sophono develops the Alpha System, which is an implantable, abutment-free bone conduction hearing device. Abutment-free is the thing here, and the Alpha System is said the be the first such device in the world. Tormach’s PCNC 770 CNC (computer numerical control) mill is being used to help Sophono further develop the Alpha System as well as other product lines.
How this got started was that Sophono was looking for a mini mill, but they were all too much at upwards of $50,000. It’s not that big of a shop. But the boss learned about the PCNC 770—from reading Desktop Engineering no doubt—and brought one in house to give it a shot.
Now, Wyant sounds like one of those guys born with a screwdriver in his hand. He’s been taking things apart and building models since he was a nipper. IBM trained him to be a machinist. Which is all a roundabout way of saying that Wyant had his doubts when the PCNC 770 showed up after they’d been looking at those pricey units. After all, the PCNC 770 starts at $6,850.
But Wyant tried it and was converted. He now uses the PCNC 770 for all sorts of jobs. He uses it to prototype iterations of the next generation Alpha System, including the dummy devices that get sent to clinicians for review and evaluation. He makes jigs and fixtures for the production and assembly people, as well as manufacturing support for different product lines. He even has done some low-volume production.
“Medical Device Product Development on the Fast Track: Sophono’s Alpha Hearing” goes into more details on all this. Wyant is extensively quoted, and there are more details on the Alpha System. The point is, however, that the PCNC 770 opened up a world of possibilities for Wyant and Sophono. This short piece does a fine job explaining what the system means for Sophono and, by extension, what a PCNC 770 can mean for small shops, R&D, engineering labs, and entrepreneurs that give it a try. Hit the link and check it out for yourself.
Thanks, Pal. – Lockwood
Anthony J. Lockwood
Editor at Large, Desktop Engineering
Subscribe to our FREE magazine,
FREE email newsletters or both!Latest News
About the Author

Anthony J. Lockwood is Digital Engineering’s founding editor. He is now retired. Contact him via [email protected].
Follow DE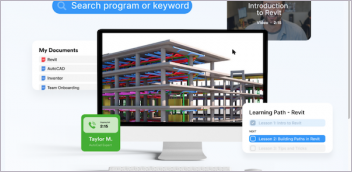

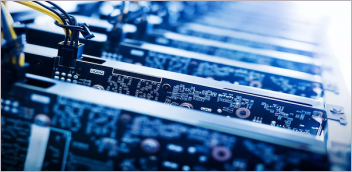
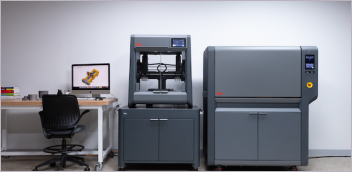