CFD: Shaping the Medical World
From ensuring clean airflows to pre-planning heart surgery, CFD software increases understanding of medical applications.
Latest News
April 1, 2013
![]() Vertical laminar flow through an operating-room airflow delivery system, as simulated with Autodesk Simulation CFD software. Image courtesy of Autodesk. |
When fluids are involved, simulating the function of many medical implants, surgical techniques, diagnostic systems and test stations can be an extreme challenge. It takes fine-tuned software to help engineers understand even the basic flow of air, blood or a liquid chemical—and for medical applications, the margins for design safety are extra-tight. What makes computational fluid dynamics (CFD) analysis such a useful tool when working in this field?
Although the competitive advantage offered with CFD analysis also keeps the fine details quiet for many medical applications, a number of analysis companies told DE why their software is particularly good at handling these complex cases.
Medical Equipment Demands Precision
Flow Science FLOW-3D CFD analysis software has found use in many medical applications, from modeling blood circulation to aiding in the placement of stents. Its capabilities in handling microfluidics can even predict transient injection forces on the components of fluids undergoing shear thinning at a needle-syringe interface. But an application that consumers might not often consider is that of designing and manufacturing the miniaturized chemical laboratory present on a diabetes test strip.
Medical CFD, the FDA and Simulating the Virtual Patient
CD-adapco’s Kristian Debus, Ph.D., says that in the medical field, many professionals are trying to get simple answers: Doctors want a yes or no. For example, in current work on aneurisms at Tufts University, a brain surgeon is studying scan data of blood vessel walls. He’s examining blood flow patterns and the wall thickness at an aneurism, to try to find correlations between the visual inspection and the computational fluid dynamics (CFD) results. So far, numerical diagnostics have not made it into real-world medical decision-making. However, CD-adapco is involved with an ASME subcommittee (ASME.org, V & V 40) for writing verification and validation guidelines for biomedical devices. The goal is to get CFD and finite element analyses (FEA) qualified to help speed up the U.S. Food & Drug Administration (FDA) approval process. When accepted, this ruling could be groundbreaking for the legal, medical and engineering realms. One important step toward this goal is the recent FDA recognition of simulation as “essential to medical device evaluation.” This opinion has just been written up by Cheryl Liu, a senior product experience technical specialist at Dassault Systemes’ SIMULIA life sciences division. (See page 32 of this issue for Liu’s article that explores this in more depth.) The article explains how the FDA’s Center for Device and Radiological Health is reaching out to both the medical and software industries, and provides a good baseline for discussion of the topic at any level of management. A second major effort is the development of the Virtual Physiological Patient, a publicly available library of computational, verified and validated submodels and data. This cross-industry collection will cover different disease states in the relevant disciplines, to aid in disease-specific device innovation. (DeviceConsortium.org) |
Roche Diabetes Care, a division of Roche Diagnostics, is involved in both R&D and manufacturing of glucose test strips, whose reagent film includes a mixture of up to 20 components that undergo mixing, pumping, coating and drying. The company employs CFD analysis for much of its material flow (rheological) development work, so Roche scientist Julien Boeuf, Ph.D., turned to FLOW-3D to help solve a phase separation issue that led to the production of inhomogeneous films.
Boeuf used the Elasto-visco-plasticity function and the Moving Object function in FLOW-3D to set up a series of mixing simulations, treating the mixture as a Newtonian fluid, a shear thinning fluid or as viscoelastic, depending on the actual chemical composition. By varying the rotation speed of a paddle centered on a cylinder of the reagent mixture, Boeuf says, “We were able to visualize the influence of rotation speed combined with fluid properties like yield stress on the flow at the cylinder walls, and then correlate this flow structure with the resulting amount of separation. This could be visualized in FLOW-3D using a Two Fluids Model.”
The models were confirmed by several experimental results, and enabled understanding which rheological properties of the chemical components are responsible for the separation.
CD-adapco has seen so much interest in medical applications using its STAR-CCM+ CFD software that this field is one of several areas the company is now supporting with industry-specific user help. If desired, you can now be assigned a designated life sciences support engineer.
“CFD is really mushrooming,” says CD-adapco’s Kristian Debus, Ph.D., life science sector manager. “In microfluidics, we have a customer who wants to look at the lab-on-a-chip model; that area really has been quite silent for many years. Another customer has been working on inhalers for years and is now doing external equipment for an ICU, where fan noise needs to be diminished.”
Other biomedical applications where STAR-CCM+ modeling is now more active than ever include devices from stents to heart pumps, powder-coating and mixing for pharmaceuticals. There are even diffusion studies for drug delivery, based on patient-specific data to determine the particle size needed. STAR-CCM+ also couples with Dassault Systemes’ SIMULIA Abaqus for fluid-structure interaction (FSI) modeling.
A big success, says Debus, is the software’s meshing tool, easily bringing in MRI/STL data and quickly creating a usable mesh. Beyond that is STAR-CCM+’s unique ability to create a mesh “overset” whereby a major mesh is fixed on most of the geometry, while a minor mesh moves along with a moving sub-part. Dubus notes the benefit: “You can do much larger motions without breaking the code.”
Tool for All
CFD analysis is increasingly becoming a tool for all designers. SolidWorks users can apply the insight gained from CFD analyses while working directly in their 3D CAD tools, since SolidWorks Flow Simulation is a licensed, fully embedded add-on to SolidWorks, designed for concurrent engineering. The software can handle internal and external flow of air, water and various fluids including blood, and include heat transfer effects.
Delphine Genouvrier, product manager for SolidWorks Simulation products, lists several good reasons for adding CFD analysis to the design process. “If you are designing a product that will be used in the body, it is difficult to understand how your fluid will flow,” she points out. “With CFD, product engineers can see the invisible, something that they would not be able to see with testing.”
One SolidWorks customer is working on a product for older people: an oxygen mask that is worn somewhat away from the face. The patient wants to speak clearly, but also obtain the proper percentage of oxygen in the airflow when it reaches the mouth. Genouvrier says, “They’ve been able to simulate the mixing phenomena between the oxygen from the mask and the ambient air around the face. That’s the kind of application that’s very difficult to measure in reality.” For example, SolidWorks Flow Simulation can help identify a dead zone in the flow pattern for a given geometry.
CFD simulations can also boost the performance of systems that are indirectly, yet critically important to medical care. Huntair, an Oregon company that designs and manufactures specialized heating, ventilating and air-conditioning (HVAC) systems, uses Autodesk Simulation CFD software to analyze its CLEANSUITE airflow delivery systems. Taking a cue from the classic cleanroom systems of the semiconductor and pharmaceutical industries, Huntair engineers recently delivered CLEANSUITE vertical laminar flow systems for installation in operating rooms at Parkview Hospital, Pueblo, CO.
The CLEANSUITE systems deliver a controlled stream of low-turbulence, temperature-controlled and high-efficiency particulate air (HEPA)-filtered air over an operating table. The result is less chance of patient contamination.
![]() |
![]() |
![]() |
Flow, pressure and stress results from a COMSOL multiphysics fluid-flow analysis of a peristaltic pump for non-contact fluid flow control. The COMSOL analysis was done by Veryst Engineering. Images courtesy of Veryst Engineering. |
“Autodesk CFD Simulation software helped us understand what is actually going on with airflow in the operating room vs. what should be happening theoretically,” says Kevin Schreiber, global director of healthcare for Huntair. The simulation allowed the team to optimize the design for minimized turbulence and better control of airflow direction, compared to the rooms’ previous horizontal-flow air systems.
Thicker Than Water
As computer processing power has increased, the time necessary to simulate actual human, or in situ, systems has become more manageable. Modeling blood-flow through vascular systems and airflow in pulmonary systems, both including moving boundary conditions, is now possible.
Stephen Cosgrove, CFD director at Altair Engineering, has watched the industry evolve. “What’s really opened up the in situ market has been the ability to go automatically from the data—a CAT scan or some sort of digital data—and turn it into something for simulation. The tools have become pretty automatic at giving you, say, an STL file of the vascular system of the aorta or a vein. We’ve then developed automated tools to go from that geometry to a mesh that’s good for your code for simulation.” It’s a task not handled equally by all simulation packages, he adds, but a specialty of Altair AcuSolve software.
“Generally speaking, the quality of the data you’re going to get to make a mesh is pretty poor, so you end up generating a mesh that has poor element quality,” Cosgrove explains. “Our AcuSolve code is finite element-based, but it uses a different formulation than other ]finite element analysis, or FEA] codes like Fidap and Flotran—a Galerkin Least Squares vs. a standard Galerkin. What that means for the end-user is a high level of accuracy where the accuracy is not a function of the element topology.”
He adds that blood is a non-Newtonian fluid and, generally speaking, FE formulations and their handling of gradients are more robust than finite-volume/finite difference approaches. AcuSolve has some very good non-Newtonian capabilities, he says, and supports full bi-directional coupling to SIMULIA Abaqus for FSI analyses without third-party translations.
Analyzing FSI
You may not immediately think of MSC Software as a source of medical CFD solutions, but Derek Barkey, the company’s senior manager, consulting services, points out several capabilities that support this field.
“About four years ago we took the built-in explicit code of the Dytran Eulerian fluid solver and added it to MSC Nastran,” he says. “Plus, Nastran has acquired a lot of the advanced material model capabilities from LS-Dyna, under license.” These additions, Barkey adds, allow MSC Nastran users to tackle complex fluid simulations.
Nastran also has an interface called OpenFSI, a standardized interface for CFD programs to talk to Nastran and vice versa, allowing the dynamic exchange of fluid forces and structural displacements. This function provides an interface to other CFD codes either directly or through the multiphysics co-coupling interface (MPCCI) developed by the Fraunhofer Institute—the same people who brought you the MP3 interface. Coupling an Eulerian fluid mesh with a Lagrangian structural mesh is Nastran’s key to handling FSI.
Barkey points out that the MPCCI is also supported by the company’s Marc solver for handling very non-linear problems. From his experience consulting for biomedical applications, he observes, “There’s almost nothing in the medical field that is linear. Tissues don’t behave in a linear way; just about everything has large deformations, and the Euler solver can handle extreme changes.”
Extreme is a good word to describe the challenge of moving from simple pipe models of, say, vascular systems to working with actual patient-scan data, just one of the application areas where ANSYS CFD analysis capabilities are helping real-world physicians. Thierry Marchal, ANSYS industry director for healthcare, says at first computational time was the primary issue. Now, with projects running on hundreds or thousands of parallel processors, analysts using ANSYS Fluent are able to add even patient-specific material parameters.
“The customer can say, ‘I want to run a blood flow simulation for a male patient, age 45,’” says Marchal, “then you can add this kind of specific artery-wall blood material property. First, you get more accurate results and second, you can be much more patient-specific where you test some new device on a whole run of different patients, therefore limiting the number of clinical tests that you will do in the future.”
![]() Pulmonary artery blood-flow simulation done in ANSYS Fluent CFD analysis software to evaluate surgical options. The goal is to increase blood flow to lungs in children born with only one functioning ventricle. Velocity pathlines simulate the injection of contrast medium in the superior vena cava to allow assessment of blood distribution from the upper body into pulmonary arteries. Image courtesy of ANSYS. |
ANSYS Fluent software is also playing a key role in predictive heart surgery, where researchers create virtual reconstructions of different surgical options, combining fluid dynamics results with a simplified model of the rest of the vascular and pulmonary systems. Simulations can actually predict blood flow distribution across the arteries and energy losses at the possible surgical connections. This multi-domain approach allows charting blood flow over time—information that could not be determined by a 3D model alone.
Sometimes surgical procedures require blood flow to be temporarily controlled in a system outside the body, as circulated through a peristaltic pump. This type of unit provides flow control by moving fluid in a tube without contacting the fluid itself. One example is an elastomeric tube squeezed from the outside, with rotating rollers pushing the contents through the tubing, either partially or fully pinching.
Nagi Elabbasi, a consultant at Veryst Engineering, used COMSOL Multiphysics to investigate the effect of pump design variations such as tube occlusion, tube diameter and roller speed, on the flow rate, flow fluctuations and stress state in a peristaltic tube. The problem seemed deceptively simple, but when Elabbasi researched previous efforts, he found little in the literature.
“This fluid-structure interaction was particularly hard,” Elabbasi notes, “because you’re really squeezing on the tube to practically close it. The more you squeeze, the more demanding it becomes on the solver because the fluid mesh must be moving correctly, not crashing. You start getting backflows, and whenever you start having flows in different directions, it becomes more difficult to converge. But COMSOL Multiphysics was really good at that.”
COMSOL Multiphysics seamlessly integrates fluids and structures, with the same interface and capabilities, says Elabbasi, so it’s not like putting two packages together. “The post-processing shows the pressure of the solid and the velocity of the fluid as if it’s one unified physics, and the moving mesh is also taken care of seamlessly. It’s a huge time-saver.” He says his company is also working to relate the flow parameters and stresses on the tube with predictions for wear and lifespan.
Simulation for Patient Predictions
Shing Pan, Altair Engineering’s senior director of product marketing, solver and optimization products, says there used to be more emphasis on modeling medical devices. Today’s focus is more on predictive and preventive medicine. Physicians may not be limited by the data they can gather; rather, they will be able to make predictions based on simulation. The software trend, then, is to sell a shrink-wrapped product for a customized solution—for cardiologists to use, for example.
One more point in favor of CFD simulation: SolidWorks’ Genouvrier says her group has been told, “There literally isn’t enough blood available for experiments during the product development process.”
Contributing Editor Pamela Waterman, DE’s simulation expert, is an electrical engineer and freelance technical writer based in Arizona. You can send her e-mail to [email protected].
More Info
Subscribe to our FREE magazine,
FREE email newsletters or both!Latest News
About the Author

Pamela Waterman worked as Digital Engineering’s contributing editor for two decades. Contact her via .(JavaScript must be enabled to view this email address).
Follow DE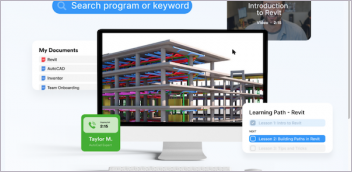

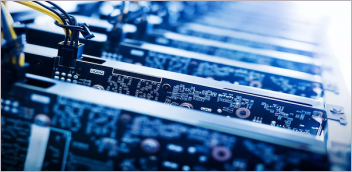
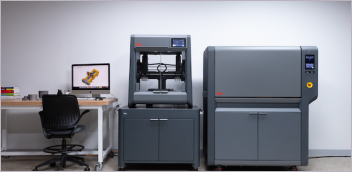