CFD on the Menu for Cafeteria Re-opening Plan
Working with Dassault, GEA leverages simulation and digital twin technology to understand aerosol spread as it works to safely re-open its employee cafeteria.

SIMULIA applications powered by the 3DEXPERIENCE platform helped GEA examine aerosol spread in its cafeteria. Image Courtesy of GEA.
Latest News
October 26, 2020
As companies across the globe struggle to safely reopen workspaces in the wake of the on-going pandemic, simulation is playing a critical role.
At GEA, a technology supplier in the food processing space, simulation software and digital twin technology are at the forefront of the company’s reopening efforts, specifically as a way to bring its Oelde, Germany, cafeteria back online. The cafeteria, a favorite gathering spot for the firm’s 1,900 employees, has been closed since March, and management was hungry to explore airflow patterns as a way to understand how the virus could spread through the air as well as contaminate surfaces like plates, trays, and tables.
“The cafeteria is an important meeting point for our employees, customers, and business partners and plays a huge role in the social side of work,” says Erich Nitzsche, vice president engineering standards & services, at GEA. “We had to ask ourselves under which conditions we could open them up again without putting employee health at risk. The missing piece of the puzzle was being able to simulate the environmental conditions. The challenge was to combine human factors, physics, and technical framework into one model that provides answers.”
To do that, GEA turned to Dassault Systèmes and SIMULIA applications powered by the 3DEXPERIENCE platform. The partners built a 3D virtual twin of the cafeteria with parameters, including employees infected with the virus coughing and sneezing, to simulate particle flow behavior throughout the space. GEA wanted to understand how the virus could spread as well as to see where there might be areas of high virus concentration.
The team used Dassault’s high accuracy CFD Solver PowerFLOW, based on the Lattice-Boltzmann Method—a tool that is highly scalable and well suited for simulating transient efforts for aerodynamics/aeroacoustics and thermal applications, according to Christian Barthel, SIMULIA expert at Dassault Systèmes. A full digital twin of the cafeteria was created, including detailed 3D geometry and boundary conditions like mass flows.
Based on simulation results, GEA can now initiate specific measures like reworking the cafeteria’s entrance and exit, adapting the seating arrangements, as well as introducing additional safety measures in the kitchen area. “The results not only help us to identify risk areas and develop suitable solutions, but we can also use them in our communication with employees,” says Peter Brüggenkötter, head of HSE Management at GEA. “Increasing employee awareness is particularly valuable at a time when everyone is reaching capacity with the pandemic situation. We want to motivate our employees while helping them to respect and maintain our defined safety measures.”
GEA plans to leverage the simulation data to make the changes that will allow it to open the cafeteria shortly. Dassault officials said they are seeing an uptick in interest for this type of use case for simulation for safe re-opening hospitals, shopping malls, churches, and sports facilities, among other large venue institutions. “They have one thing in common—the need for reliable analysis in order to increase the safety of people to secure their business,” says Dassault’s Barthel.
To learn about how GEA leveraged simulation and digital twin technology as part of its COVID-19 planning, watch this video.
More Dassault Systemes Coverage
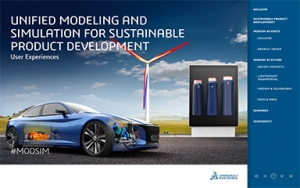
Subscribe to our FREE magazine,
FREE email newsletters or both!Latest News
About the Author

Beth Stackpole is a contributing editor to Digital Engineering. Send e-mail about this article to [email protected].
Follow DE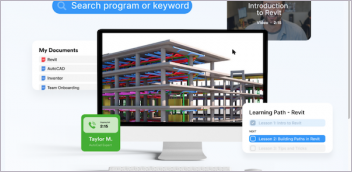

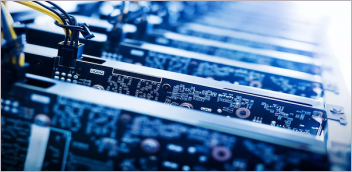
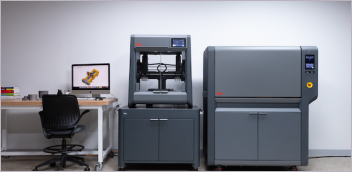