
Land Rover BAR CEO Martin Whitmarsh. Image courtesy of Harry KH/ Land Rover BAR.
Latest News
March 17, 2016
The team’s goal is to bring the America’s Cup back to England. The America’s Cup race began in Britain in 1851, but the nation renown for its prowess at sea has yet to win the prestigious trophy, said Whitmarsh.
Whitmarsh: Some engineering challenges to making a 72-ft. boat hydrofoil. Catamaran is “flying” #sgc16 pic.twitter.com/1eQ3to7MOT
— Desktop Engineering (@DEeditor) March 7, 2016

America’s Cup fans will know that the race changed when technologically advanced double-hull catamaran designs replaced the single-hull yachts used until 2007. The modern racing yachts appear to “fly” above the water perched on foils. Using a 50-ft. wing-like rigid sail, aerodynamic design and human expertise, they can travel three times faster than wind speeds — up to 50 knots (57.5 mph), according to Whitmarsh.
Design and simulation are critical to creating a winning boat. America’s Cup rules prohibit the final craft from being used in the preliminaries leading up to the final race in Bermuda in June next year. Until then, teams rely on slightly smaller vessels, which are also used as test platforms, to develop the final design. Some of the technology Land Rover BAR is using to design its final yacht includes CD-adapco’s STAR-CCM+, Dassault Systemes SOLIDWORKS, Siemens PLM Software’s NX and LMS Imagine.Lab Amesim, ESTECO’s collaborative engineering software and Renishaw for 3D printing.
Change for the Better
Like the America’s Cup contenders, speed is all important to competitive bicycle racers and athletes who compete in IRONMAN competitions. Reducing drag is the name of the game for Kevin Atkins, aerodynamicist at Cervélo Cycles, which designs high-performance, road-only bicycle frames and components. (Learn more about the effects of drag on bike aerodynamics here.)
“We want nothing more than our customers and our riders to be as fast as they can be, and to do that we have to make sure that the aerodynamics are at the level we are satisfied with,” said Atkins in his STAR Global Conference 2016 presentation.

To that end, Atkins initiated a review of how Cervélo designed its products in 2013. He placed a focus on automation, accuracy and efficiency, beginning with an update to the latest software. At that time, when STAR-CCM+ version 10 was available the company was still using STAR-CCM+ version 7 because they were comfortable with it.
“Preprocessing took about four hours for 20 million cells, which is not very good, and that was primarily in meshing,” Atkins said. “Then 20 hours of solve time and approximately two hours in post-processing. So that was taking — considering we had to do multiple yaw angles — about three days for a full detail simulation.”
Atkins worked with Oxford University’s Dr. Neil Ashton to make the process more efficient and more accurate. Cervélo updated to the latest version of CD-adapco, used batch scripting to mesh, process and solve at the same time on their cluster, and removed himself from the process as much as possible — all of which saved five hours per run.
“That’s all great, but there was still a lot of time being wasted on the solver,” Atkins said.
Atkins and Ashton decided to take a step back to start from scratch on how they solved for turbulence. They eventually verified that a two-tier approach, using DDES (delayed detached eddy simulation) and RANS (Reynolds-averaged Navier–Stokes) models was the best solution.
“We switched to a coupled solver, which was a bit surprising,” Atkins said. “It promoted stability greatly, improved our robustness a few times over and gave us much faster simulation while giving us very good correlation with our results.”
How much faster? The changes brought Cervélo’s simulation runtime from 20 hours to two. “Now we have a new challenge,” Atkins said. “The designers can’t keep up with the CFD (computational fluid dynamics).”
Not content to rest on that success, Atkins is now investigating the new local surface remeshing feature in CD-adapco STAR-CCM+ v11.02, as well as planning to simulate the rider’s moving legs using overset mesh and use Optimate+, which he was able to evaluate recently.
“Using the SHERPA algorithm (in Optimiate+) we looked at an aerodynamic handlebar,” he said. “We were able to look at a large amount of variables in a short amount of time since we didn’t need the designers to generate many different models.”
Atkins said the Optimiate+ evaluation provided impressive results, but they are just the tip of the iceberg. Being able to do more iterations will allow Cervélo to fine tune their designs for a sport where every advantage is critical.
“If you are like we were in the past and really adamant about keeping the status quo, challenge that,” he said. “You can save a lot of time and make some considerable progress in your simulation, and in your design and in your results.”
You can see one of Cervélo’s bikes, the P5, in the video below.
STAR-CCM+ Roadmap
The Land Rover BAR and Cervelo Cycles presentations were just two of more than 140 given at the STAR Global Conference 2016. In addition, a live demonstration of the new features in STAR-CCM+ v11.02 was presented by CD-adapco’s Matt Godo and David Mann. Key new features in v11.02 include local surface remeshing, native cylindrical primitive particle types in DEM, co-extrusion in computational rheology, hinged multi-body motion and fluid-structure interactions of rotating bodies.
CD-adapco also provided a sneak peek at things to come in STAR-CCM+.
“We want to continue delivering mainstream features and enhancements to the ground transportation and aerospace industries, which are our larger sectors, but we’re putting a significant effort in development to improve the capabilities of STAR-CCM+ in the fields of the marine sector, the oli& gas, the energy and power generation, as well as chemical process and electronics,” said Jean-Claude Ercolanelli, senior vice president, Product Management at CD-adapco. “This is really important to us.”
Long-term strategy directions for STAR-CCM+ v12 include integrating global parameters even more to improve multi-disciplinary design exploration, expanding the scope of the multi-physics available to solve by making them more seamlessly coupled and transparent to users. For example, in-cylinder engine (ICE) capabilities are being migrated into STAR-CCM+ and are on track to be fully available in 2017.
[gallery ids=”/article/wp-content/uploads/2016/03/IMG_5588.jpg|,/article/wp-content/uploads/2016/03/IMG_5590.jpg|,/article/wp-content/uploads/2016/03/IMG_5589.jpg|”]
For this year, Ercolanelli said v11.04 will be released by the end of June and v11.06 will be available in October, which is the usual rollout schedule for X.04 and X.06 STAR-CCM+ releases. The releases are based on three pillars:
- Technology to broaden the scope of the applications you can solve with STAR-CCM+ and improve the current applications
- Experience, which is all about saving your time with more streamlined workflows.
- Productivity, especially to better utilize hardware resources and run more jobs in the same amount of time.
Some specific highlights of upcoming STAR-CCM+ releases this year include the ability to customize and differentiate simulation trees, which are getting longer and more difficult to navigate; a theory guide added to the documentation; and local surface wrapping.
“Our objective is to make you more effective in discovering more designs faster,” Ercolanelli said.
For more details on STAR-CCM+ v11.02, visit CD-adapco’s blog.
Subscribe to our FREE magazine,
FREE email newsletters or both!Latest News
About the Author

Jamie Gooch is the former editorial director of Digital Engineering.
Follow DE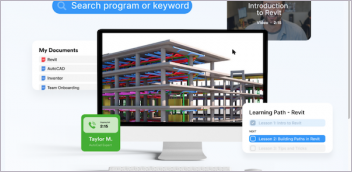

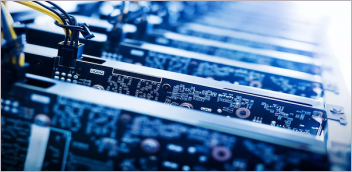
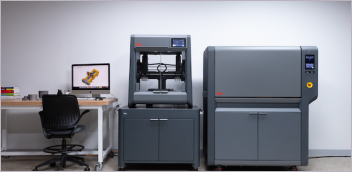