Latest News
September 1, 2015
By Dr. Royston Jones, vice president of European Operations and chief technology officer, Altair ProductDesign
Simulation-driven design—the philosophy of using simulation tools upfront in the design process to find the ideal design solution fast—is something we talk a lot about at Altair. It’s something the Altair ProductDesign team puts into practice every day with clients across industry verticals. In many ways though, this philosophy is something of an ideal. Even in the modern, multi-disciplinary design environments of today’s vehicle and aircraft manufacturers, simulation is not seen as a critical path within the conceptual design stages of programs. The reality is that for many companies, design remains king and simulation is there to provide validation only.
I am fortunate that my role at Altair means that I meet design and engineering teams from across Europe’s major manufacturers and experience a wide cross-section of attitudes and approaches to the use of simulation today. In recent years, I have witnessed a change in attitudes toward computer-aided engineering (CAE). There is more willingness to explore the potential and use of CAE technology. There is an enthusiasm to apply it more freely. Companies are continuing to take steps toward the simulation-driven design ideal. For me, this is due to a handful of factors.
Barriers to Upfront Simulation
First, something that’s always held CAE and simulation back as an integral part of design processes is the speed in which an analyst can provide results back to program teams. Speed was less of a problem when an analyst just needed to validate performance. However, when you move to a situation where simulation teams are tasked with providing design direction within the early exploration phases of conceptual design, speed becomes paramount. This barrier is being eroded away on an almost daily basis with the advent of ever more powerful and cheaper access to high-performance computing (HPC) resources.
Second, for simulation to play an upfront role, the results have to be accurate. Without accuracy, CAE loses its credibility and with that goes any ability for it to influence design. But modern simulation technologies have addressed this barrier too. Witnessing the accurate simulation of carbon fiber structures deforming on an individual ply level during a crash event or seeing a simulation of an injury to muscle tissue is something we could have only dreamed of just a few years ago; and things will only get better as time goes on.
Lastly, the intelligence of modern-day simulation tools is helping to drive adoption within the early design process. The necessity for many manufacturers to save weight, material and cost to produce products has resulted in an increased adoption of design optimization techniques. Software can provide vital design insights on where material is needed and where it can be removed without negatively impacting performance. These tools offer designers new ways to rapidly explore design concepts for specific methods of manufacture to bring material-efficient, high-performance products to market.
For me, one of the best examples of the advantages of moving simulation techniques upfront in the design process has been the advent of additive manufacturing (AM). In the AM world, the analyst becomes key, producing early concepts for designers to explore and develop; safe in the knowledge that the organic (or bionic) structural design is mass efficient, meets or exceeds the performance requirements and can be manufactured. A simulation-driven design approach in combination with AM offers unprecedented levels of weight and materials savings—demonstrating why simulation is such a compelling technology when used in the early design phase.
Cultural Shift Needed
But even with all this progress, simulation-driven design is not yet the standard way of designing products. Perhaps the final thing holding back its trajectory is the culture ingrained in well-established design processes. Processes that have worked time and time again to produce successful products are not easily changed.
Much of my work involves challenging traditional design practices and showing how a simulation-driven approach, by example, can positively impact competitiveness and profitability. In my view, the key to truly innovative products lies in the closer integration of simulation with design. I’m encouraged to see that barriers have fallen and examples of successful applications of simulation-driven design have increased. We’re getting closer to the simulation-driven design ideal. Long may that continue.
Dr. Royston Jones is executive vice president of European Operations and global chief technology officer for Altair ProductDesign. Comments can be sent to DE-Editorsmailto:[email protected].
Subscribe to our FREE magazine,
FREE email newsletters or both!Latest News
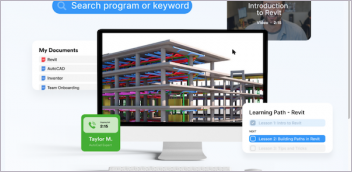

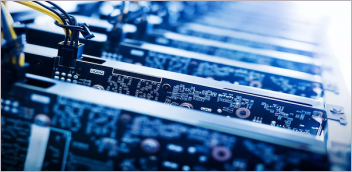
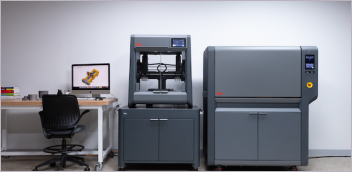