Latest News
November 1, 2004
By Louise Elliott
That’s a big change from a decade ago, when CAD growth seemed potentially unlimited,the CAE market was generally placed at around $400 million, and the acronym PLMdidn’t exist.
Behind this CAE growth, says Daratech Managing Editor and Analyst Tim Hickey,lie three major factors: the competitive and economic pressures on companies tospeed up the design process and get new products to market with fewer physicalprototypes; software with new, easier to use interfaces; and the ability to runcompute-intensive studies much faster on powerful desktop computer platforms.
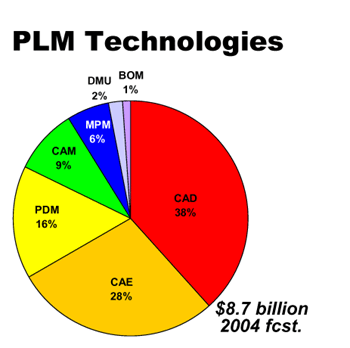
The technologies included in Daratech’s studies are structural finite elementanalysis (FEA), computational fluid dynamics (CFD), motion simulation, crash,and process integration and design optimization (PIDO).
| |
The most important long-term result of widespread deployment of CAE may wellbe a change from considering physical test results always to be the test resultsof record—although in safety-critical product development, such as aeronautics,aerospace, and automotive, some physical testing will always be necessary—andtoward reliance on proven CAE technology.
Selling Industry on the Benefits of CAE
Some factors work against that scenario, however. Charles Foundyller, CEO andfounder of Daratech, pointed out in his conference presentation that CAE is notyet integrated into the mainstream of product-creation processes. Corporate cultureand education, together with the complexity of CAE, have mitigated the widespreadadoption of its technologies. And, CAE has had few champions in the boardroom.Adds Foundyller, “Today’s PLM tools inhibit compatibility and interoperability,preventing CAE automation.”
Until recently, developers of CAE software have had a poor track record of beingable to convince companies of the benefits of CAE as well, says Hickey. “The softwaresuppliers have traditionally failed to make the business case to industry as awhole, but that is changing,” he says. “The recent recession and difficult manufacturingclimate have forced companies to make cost-cutting a priority, and they are scrutinizingtheir processes to uncover ways to save money. The early product development stagesoffer a lot of opportunity”
He points out that a few years ago, more cars were recalled in the United Statesthan were actually sold, cutting profits and confidence. “In the automotive industry,companies recognize that analysis offers a reliable and cost-effective alternativeto building and breaking a lot of prototypes. No one is suggesting we’ll get toa point where they can analyze straight through to production. But if CAE helpsthem build a more reliable product and cut the number of prototypes, it createstangible product and business benefits now, and averts disaster down the roadby mitigating warranty expenses.”
“At every conference, we see some attendees who are new to the world of CAE,“says Monica Schnitger, Daratech’s senior VP of Market Analysis. “Their companieswant to improve product quality, improve design cycle time, study more designoptions before finalizing on a design…. (And) once they see what these tools cando, companies get the picture.”
Real-Life Experience
Presenters at the DPS Conference, most representing major automotive, aerospace,and industrial equipment companies, spoke of their experience with CAE and itseffects on product development.
Dr. Paul Bevilaqua of Lockheed Martin’s Advanced Development Projects, betterknown as Skunk Works, spoke about how the company leveraged CAE in developingthe vertical lift thrust system in the Joint Strike Fighter (JSF). He said thatthe golden rule at Skunk Works is: “Get to a prototype fast.”
With that rule in mind, Bevilaqua’s team started to design the JSF’s lift fanpropulsion system—one of the key differentiators of the winning Lockheed Martindesign—using CAE tools. CFD played a large part in showing the team that its fanjet design protected the aircraft’s engine from very hot exhaust created whengetting the full 40,000 lbs. of vertical lift from just four nozzles. The designwas not only good enough to win the huge government contract, but it also wonthe 2001 Collier Trophy “for the greatest achievement in aeronautics or astronauticsin America, demonstrated during the preceding year for the F-35 lift fan propulsionsystem.”
CFD again came to the forefront of CAE technologies in the presentation madeby Jean Mallebay-Vacquer, the director of DaimlerChrysler’s Environmental Laboratories,when he spoke about designing an automotive cooling system to minimize any illeffects on the environment.
Mark Kuhn, director of Design Engineering for worldwide automotive consultantsRicardo Inc., described an integrated analysis program based on thermal and structuralanalysis that enables design release two months sooner than in the past. “Runningsimplified structural and thermal analyses very early in the design cycle reducesthe program duration, and lets designers move on to progressively more detailedanalysis,” Kuhn said.
Thomas Chimner of Eaton Corp. agreed with Kuhn, and said that of all availabletechnologies, up-front CAE has the biggest impact on design. The availabilityof greatly increased computer power together with new, easier-to-use softwarehas combined in a world with fewer analysts to create a situation where designersuse FEA for quick assessment of design changes. “The old system followed a pathfrom design to FEA to building prototypes to testing them,” Chimner said. “Nowdesign and CAE occur at the same time to produce a shorter development cycle andreduced physical testing.”
What Comes Next?
Other presenters at the conference underscored Foundyller’s point about currentPLM tools being unable to handle CAE. For example, Subhasish Roychoudhury, managerof CAE Systems IT for Ford Motor Company, pointed out that better management ofCAE data will be essential for analyst efficiency and effectiveness in decision-making.
PDM systems, the heart of PLM offerings today, were not designed to handle thehuge volume of pure numerical data generated by CAE tools, and new solutions thatcan integrate with other tools in the PLM kit are needed. But even without suchtools, the competitive advantages of CAE technologies are becoming apparent inlarge companies that focus on systems rather than components.
Louise Elliott is a contributing editor to Desktop Engineering. Contact her aboutthis article via Desktop Engineering Editorial Feedback.
Daratech, Inc.
Cambridge, MA
daratech.com
Subscribe to our FREE magazine,
FREE email newsletters or both!Latest News
About the Author

DE’s editors contribute news and new product announcements to Digital Engineering.
Press releases may be sent to them via [email protected].
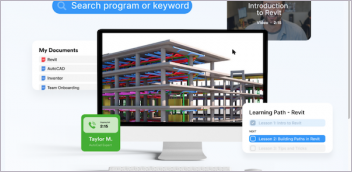

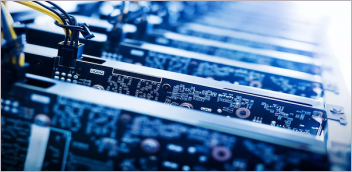
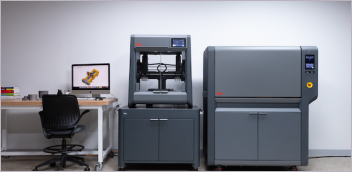