Latest News
September 1, 2005
By DE Editors
Predict Heat Treating Results and Merge Simulations
Scientific Forming Technologies Corp. says its new DEFORM-HT heat-treating simulation software provides quantitative information on critical process and part-specific variables that has been unobtainable before, even with shop trials. DEFORM-HT is also said to be the first heat-treating simulation package that can fully integrate its results with related predictions for upstream/downstream operations, such as material production, forming, and machining.
![]() |
DEFORM-HT performs its virtual heat treating in 2D or 3D. It illustrates and quantifies the effects of process variation through sensitivity analyses, reducing the time and cost for troubleshooting as well as heat-treat process development. DEFORM-HT can model a variety of heat-treating processes, including normalizing, austenizing, carburizing, solution treating, quenching, tempering, aging, and stress relieving. It can predict phase transformation, phase volume fraction, distribution of hardness, case depth after carburizing, and grain size. DEFORM-HT also models a variety of metals, including carbon steels, aluminum, titanium, and nickel-based alloys. Material models include elasto-plastic, thermal elasto-plastic, and creep.
DEFORM-HT runs on Windows XP/2000 or Unix. It can be licensed as an add-on module for other of the company’s DEFORM System integrated manufacturing applications.
For complete details, fo to the company’s website.
Mazak and Gibbs Collaborate on Future CNC Solutions
Gibbs and Associates and Mazak-USA have entered into a strategic collaborative partnership agreement to optimize support for Mazak’s multitask CNC machine tools, such as the Integrex, Integrex E-Series, Multiplex, Quick Turn Nexus, and Super Quick Turn (SQT) model. A nondisclosure agreement allows the two companies to exchange information about and collaborate on their next generation solutions.
“Multitask machine tools represent one of the fastest growing segments of machine tools,” says Robb Weinstein, Gibbs and Associates’ senior vice-president of sales and strategic planning. “As a matter of fact, Mazak customers already make up a significant percentage of GibbsCAM MTM users. Working with Mazak, GibbsCAM will provide a powerful NC programming solution able to support the wide variety of capabilities and configurations Mazak offers.”
According to Mazak, its multitask machine tools help users reduce part costs; increase throughput; equalize shipment and cash flow; increased part accuracy; reduce setup times; save time; and increase profitability.
Mathsoft has integrated Mathcad with the National Instruments LabVIEW graphical development environment to provide advanced joint calculation and measurement solutions. The integration creates an end-to-end design, measurement, analysis, and reporting environment to help engineers execute their product development work.
Engineers can use Mathcad to trigger data capture and measurement in LabVIEW, which can then automatically export values back to Mathcad for further calculation or reporting. This makes it easy to test lab data against mathematical models and share LabVIEW results with Mathcad.
NI LabVIEW is a graphical development environment for creating flexible and scalable test, control, and design applications. It lets engineers interface with real-world signals, analyze data, and share results and applications. Mathcad is a design environment that enables engineers to simultaneously explore, calculate, and document all of their mathematical formulas and calculations.
Agilent Technologies Inc. has acquired privately held Eagleware Corp., which does business as Eagleware-Elanix. An agreement that stated Agilent would acquire substantially all of the assets and business of Eagleware-Elanix was announced in July, and the deal was completed in August. No amount for the transaction is being released.
Cimatron Webinar Coaches Moldmakers to Learn to Love creating Electrodes
An online seminar sponsored by Cimatron Technologies aimed at toolmakers covers methods to increase a designer’s proficiency in electrode creation while simplifying the process and easing the pain associated with it. The free online seminar outlines the company’s Stand-Alone Electrode solution. It supports toolmakers through the entire process of designing, documenting, and manufacturing electrodes used in electrical discharge machining (EDM).
![]() |
Todd Spencer, the design manager for Polymer Technologies, which uses metal insert and two-shot molding to supply automotive switches, relays, and electro-mechanical parts to OEMs and Tier 1 suppliers, leads the discussion. “Electrode creation is an integral part of the tool-making process,” says Spencer. “It can be painful, but with the right process and technology it can be manageable and efficient. If you can streamline this process, it can have a direct impact on your bottom line.”
That’s what Cimatron’s Stand-Alone Electrode solution aims to do. The new configuration, based on the company’s Quick Electrode application, includes everything necessary to manage the EDM electrode process from design to manufacture, while eliminating the need to use other software. EDM electrodes are often used when milling is not possible or in order to achieve better surface quality. Electrode design, documentation, and machining require a large, varied set of CAD and CAM tools. The beauty of Cimatron’s solution is that it enables the process while reducing the time-consuming repetitive tasks through automation and customized tools.
Currently available with Cimatron E 6.0, the Stand-Alone Electrode solution provides all the necessary tools for defining the EDM burning area, extracting the electrode shape, automatic documentation, and machining; all specifically optimized for electrodes. Nonessential CAD/CAM features are excluded, so while perhaps not learning to love electrodes, designers will certainly learn to approach the task of designing them with much greater ease and peace of mind.
![]() |
Stating at the geometry creation of the electrode, the design template can receive any burning area shape and automatically create the complete electrode geometry. Other customized tools are used to create smooth extensions from the burning areas to the top of the electrode, and for optimized blank and holder usage. The system also provides dedicated drawing templates and rules, which allow users to create complete drawings with a single click of a button. Rich NC template capabilities are available with automatic selection of machining strategy according to the shape of the electrode. Cimatron’s integrated solution saves time by ensuring that data created when designing the electrodes can be used later when programming the machining step.
“The Stand-Alone Electrode solution was developed in response to our many customers who approached us about developing a more cost-effective bundle,” says Zvika Naggan, president and CEO of Cimatron, “... without other nonessential CAD/CAM functionality.”
The Electrode Solution is available in two configurations: Electrode Solution, which covers the complete process of designing and documenting electrodes; and Electrode Pro Solution, which adds 2- and 3-axis milling and simulation for electrodes.
For more information, go the Cimatron Technologies website. Check out the seminar session via the playback online by clicking here.
SPECapc Releases Benchmark for Maya 6.5, Announces Future Releases
A new benchmark for systems running Alias Maya 6.5 modeling, animation, and rendering software has been released and is now available for download from SPEC/GPC.
The Application Performance Characterization (SPECapc) project group demonstrated the Maya 6.5 benchmark at SIGGRAPH 2005. The group also announced plans and gave partial demos of upcoming benchmarks for Pro/Engineer Wildfire 2.0, Solid Edge V17, and UGS NX3. Those three updated MCAD benchmarks are expected to be released by the end of the year.
![]() |
SPECapc for Maya 6.5 is an updated benchmark that reflects the changes Alias made to improve OpenGL performance by switching from glArrayElement to glDrawElements. The SPECapc group did additional tuning to streamline the benchmark’s graphics path. The greater efficiency makes the benchmark less CPU-bound, and will accentuate the differences among system configurations.
“With the cooperation of ISVs, we are working to stay up-to-date with the latest application releases and dig deeper into new functionality,” says Dan Bennett, SPECapc chair. “Benchmark testing always requires some trade-offs, but we’ve taken great strides to make SPECapc test results reflect user experiences.”
SPECapc’s current suite includes application benchmarks for 3ds max 7, Maya 6, Pro/E 2001, Solid Edge V14, and SolidWorks 2005. The SPECapc group continues to seek additional benchmarks for leading software programs in CAD/CAM/CAE, visualization, and digital content creation (DCC).
SPECapc is a project group of the Graphics Performance Characterization (GPC) Group, which is part of the Standard Performance Evaluation Corp. (SPEC). For more details, click here.
Subscribe to our FREE magazine,
FREE email newsletters or both!Latest News
About the Author

DE’s editors contribute news and new product announcements to Digital Engineering.
Press releases may be sent to them via [email protected].
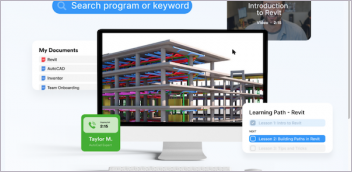

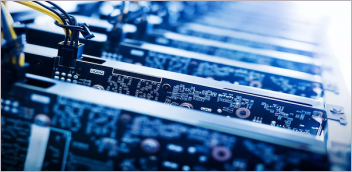
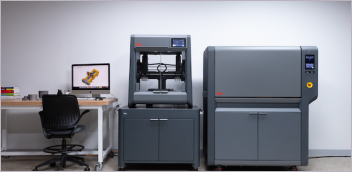