Briefings: August 2006
Industry News, Reports, and Items of Interest
Latest News
July 1, 2006
By DE Editors
ABAQUS for CATIA V5 Version 2.3 Launched
Dassault Systemes (DS; Paris, France) has announced Version 2.3 of ABAQUS for CATIA V5. V2.3, says DS, takes advantage of the latest technology in ABAQUS 6.6 and CATIA V5 R16 as well as builds on the company’s SIMULIA strategy. (SIMULIA, which encompasses all DS simulation solutions, offers scalable simulation solutions and an open framework for multidisciplinary analysis within PLM.)
![]() |
ABAQUS for CATIA V5. |
The ABAQUS-CATIA integration enables advanced methods developed and validated by ABAQUS specialists to be deployed in an enterprise as “proven” analysis workflows. This enables design engineers and analysis specialists to leverage identical FEA methods and models within CATIA V5. It also, says DS, lets design teams do more simulations earlier in the product development process.
![]() |
ABAQUS for CATIA V5. |
New functions in ABAQUS for CATIA let you leverage CATIA’s weld modeling functionality. Its support of ABAQUS 6.6 is said to take advantage of full functionality of ABAQUS/ Standard solver capabilities, including contact enhancements and performance improvements. Further, the ABAQUS continuum shell technology is available to users. This enables the modeling of shell structures with continuum shell elements, which permits the use of the actual CAD geometry of the structure rather than an approximation involving midplanes and offsets. This approach is said to simplify modeling while improving the accuracy of simulations involving contact.
For more information, click here. Third Annual Extreme Redesign Global Design and 3D Printing Contest
$2,500 and $1,000 student scholarshipawards aimed at promoting interest in engineering careers.
The Dimension 3D Printing Group, a business unit of Stratasys, Inc. (Eden Praire, MN), has announced the third annual Extreme Redesign: The Ultimate 3D Printing Challenge global design and 3D printing contest for high school and college students. CAD students worldwide are invited to send in their best Extreme Redesigns for a chance at scholarships in the amounts of $2,500 or $1,000. Judging is based on design creativity, part utility, integrity, and aesthetics.
The company will award teachers of first-place student winners a notebook computer for classroom use. In addition, the teacher with the most student entries overall will receive a notebook computer for encouraging student participation in the contest. To qualify, the instructor’s name and e-mail address should be included on the contest application form.
Last year’s Extreme Redesign contest received more than 500 student entries from around the world. Winning designs included a detachable cord reel, electric toothbrush wall mount, and rotating calendar. Photos and descriptions of the 2004 and 2005 winners are available on the Extreme ReDesign web page.
To enter, students need to identify an existing product, piece of art, or architecture and redesign it, improving on the original design by adding new functionality or aesthetic qualities. Once the design is complete, students send an .STL file of their Extreme Redesign via the Dimension website along with a completed submission form and a 200-word description of the value and benefit of the redesigned part. Dimension will then send entrants a 3D print of their redesign that they can hold in their hands and evaluate. From that point, entrants have the opportunity to make design improvements to develop a second iteration for final submission.
Final entries must be postmarked by Dec. 31, 2006. Complete contest rules and submission details are available by clicking here.
Spicer Corp. (Kitchener, ONT) has announced the release of version 8 of its Imagenation digital communications solution for the distribution and output of MCAD files and office documents between technical and non-technical users. Version 8, says Spicer, features desktop interactivity improvements that enable users to scan, review, mark up, and print office documents, CAD drawings, and model formats more efficiently.
Imagenation 8’s new XP-style user interface is designed to help you customize your desktop by organizing toolbars and preferences to suit your needs. This, says the company, results in faster, more efficient desktop interactivity between documents, scanners, and browsers.
![]() |
Imagenation 8 from Spicer Corp. |
Improvements in Release 8 include a new File Send feature that lets you send rendered documents as PDFs. PDF support itself has been enhanced with the ability to save Spicer markups in PDF-format documents as PDF data. An Imagenation plug-in for Mozilla Firefox browser is now available.
Imagenation 8 offers support for several new file formats, including Autodesk Inventor10 2D & 3D; Digital Negative; JT; Microsoft Message Format (.msg); PTC Pro/Engineer V16 to Wildfire 2 assemblies; and SolidWorks 2006 2D and 3D. Additionally, it now supports several new scanners from Canon, Epson, Fujitsu, and HP.
Imagenation is available for Windows 2000, Server 2003, and XP. Imagenation’s pricing model provides options for fixed, enterprise, server, and OEM licensing.
You can register for a free trial download of Imagenation 8 at the company’s website.
One year after the launch of the RP4Baghdad program, an initiative founded by members of the RP&M (rapid prototyping and manufacturing) industry, doctors in Iraq report that the project has supported the successful treatment of more than 45 civilians suffering from severe injuries to the head and face, according to RP4Baghdad.
In addition to aiding in these complex reconstructive surgeries, RP, which produces 3D models from computer-generated designs, is now being used to produce prosthetic limbs through the program.
![]() |
Courtesy of RP4Baghdad. |
“It may come as no surprise that health care facilities in Iraq have degraded significantly over the last several years,” Dr. Omar Al Ani, an Iraqi surgeon involved in the project was quoted as saying. “The RP4Baghdad program has given our physicians an invaluable advance in technology. The models, unlike two-dimensional x-rays, provide detailed, ]3D] replicas of the treatment area, giving both patient and physician superior pre-surgical information. This results in more effective pre-surgical planning, reduced procedure times, and more precise fitting of implants and prosthetic limbs.”
Patients identified as candidates for the RP4Baghdad program are referred to a Baghdad medical facility where craniofacial injuries are CT scanned or amputees have casts made that are, in turn, sent to the US for laser scanning. The data from the scans is then sent to one of four manufacturing facilities—three in the US and one in Belgium—where the data is converted to either a 3D computer model of the anatomy or parts for socket construction in artificial limbs. The model is then shipped back to Iraq where it used to plan and practice surgery or, in the case of sockets for prosthetic limbs, is fit to the patients. The models or parts usually arrive in Iraq within a few weeks of the CT scan.
By August 2005, more than 300 civilians were wait-listed for artificial legs in one of three medical centers in Baghdad. Doctors in Iraq believe that many more amputees are in need of prosthetic legs but have not registered for the list due to the backlog.
Fried Vancrean, president and CEO of Materialise and an originator of the program, said, “RP4Baghdad displays not only the powerful impact of additive fabrication in the field of medicine, but more importantly, an inspiring level of human concern and compassion across our industry.”
For more, click here.
UGS Embraces 3D Geometric “Shape Search”
Technology That Eliminates Duplication
Formerly sold as Geolus SHAPE, the application lets manufacturers locate 3D models of digitally defined parts from a database of more than a million parts and locate duplicate or similar geometry in seconds, eliminating manual part pre-classification. Geolus uses the geometric data associated with any of the commonly available PLM or CAD programs for its search, rather than alphanumeric characters.
The acquisition from Software Design & Management AG (sd&m; Munich, Germany), a software and consultancy firm, paves the way for UGS to build advanced geometry-based search applications that promote innovation through reuse and eliminate the time and expense associated with designing or purchasing duplicate parts.
The demonstration went like this: Spend a few minutes sketching a part in your CAD program, click the Geolus Search button in your design environment, and get a list of thumbnail images of similar parts in seconds. From there, you can specify certain parameters to get more parts.
Companies that adopt an automated part reuse strategy save on costs, say those who already use this technology, but most have not gone this route because traditional search engines use alphanumeric characters or metadata rather than part geometry as search criteria. While this can be a powerful strategy, it requires detailed parts classification. Geolus requires no such data entry, relying on the automatic generation of shape geometry.
UGS says an added benefit is the stimulation of new ideas and innovation by cutting the need for part redesign.
According to UGS, Geolus Search can be used today in virtually any PLM or CAD environment due to its support for multiple data formats such as VRML, STL and JT, UGS’ open 3D data format for visualization and collaboration. And because virtually all major CAD applications are compatible with JT, UGS plans to further leverage that support by using JT as the foundation for future Geolus Search development within the UGS product portfolio.
Update scheduled for introduction at IMTS Show in Chicago.
DP Technology (Camarillo, CA), the creator of ESPRIT CAM software system, has announced its latest release, ESPRIT 2007. The new software will be introduced officially at the IMTS 2006 machine tool show in Chicago from September 6-13, and is expected to begin shipping to customers by late summer.
ESPIRIT 2007 will include a variety of new and upgraded features including enhancements and new functionalities for milling, turning, and wire EDM programming. It will also introduce ESPRIT FX, which the company describes as a new innovation in advanced CAD-to-CAM feature exchange.
![]() |
ESPIRIT 2007. |
ESPRIT FX technology goes beyond transferring just the part geometry, says DP Technology, by providing portions of the original CAD Feature Tree directly inside the ESPRIT user interface, thereby including the complete original design intent with all features, tolerances, material properties, surface finishes, administrative data, etc. Using the FX technology, the CAD features and their associated properties are mapped into machinable features. These manufacturing features and their properties are then fed into the ESPRIT KnowledgeBase, aiding the user in selecting how to machine the part based upon existing best practices.
In addition to ESPRIT 2007, DP Technology has said it will also be demonstrating its newest addition to the ESPRIT CAM software family, ESPRIT Mold, an automated 3-axis and 5-axis CAM system (click here for more ESPRIT Mold).
For more information on ESPRIT 2007, click here.
Axonai.com Web Portal Simplifies Bidding
Parts bidding barriers between buyers and suppliers eased and simplified.
Axonai Inc. (West Lafayette, IN), an online collaborative network specializing in connecting buyers and suppliers, has launched an Internet portal that, it claims, makes the parts bidding process more efficient and affordable.
According to Axonai, the process takes a pay-as-you-go approach, unlike many online models that are membership-based. Axonai’s process detects eligible suppliers based on information they’ve uploaded to the site’s directory and matches them to buyers. This, says the company, weeds out inappropriate bids and shortens the bidding process by an average of 12 days.
Once a design engineer uploads a CAD model depicting an item the buyer wishes to have produced, Axonai’s Buyer Sourcing Assistant helps the buyer determine the most appropriate manufacturing process for that particular part. It then distributes RFQs to previously qualified suppliers.
Once buyers submit their RFQ, they can receive and review the responses online. They can also access such information as the supplier’s profile and rating as well as comments about the supplier in reference to other jobs.
At the opposite end of the supply chain, suppliers use Axonai’s online service to specify their capabilities and the kinds of manufacturing jobs they would like to receive. When an RFQ comes their way, they can review, at no cost, the part’s dimensions, tolerances, materials, and specifications (including delivery deadlines). They also are able to view how many RFQs the buyer has posted previously as well as the buyer’s ratings from previous jobs. Once the supplier is satisfied that it has met eligibility requirements, the supplier can pay a fee to view the buyer’s contact information in anticipation of bidding on the job.
The Axonai system also includes enhanced project management features for buyers and suppliers to work together during the design, production, and inspection phases. For more information, click here.
“Geolus Search is a revolutionary technology,” said Chuck Grindstaff, executive vice president of PLM Products for UGS, in a statement to the press. “Its multi-format compatibility and support for the JT data standard are also consistent with UGS’ Open by Design business model that creates value for the entire PLM industry.”
In other news, UGS says Parasolid version 18.0 is available and that this version comes with new capabilities that enhance the level of user control over 3D model construction, editing, and interrogation, as well as numerous improvements in application support functions. This latest release also consolidates support for advanced Microsoft technologies, including Visual Studio 2005 and .NET.
Parasolid V18.0 includes extensions that enhance ease-of-use in key operations. Some of these are finer user control in local editing with extensions to thickening, tapering, and embossing; enhanced blending and filleting in tightly-curved regions through automated re-ordering and repair; graphical enhancements; and extended application support with improvements in data tracking, rollback efficiency, and partition management.
UGS also announced Parasolid Bodyshop Version 9.0, a Parasolid-based toolkit that repairs, optimizes, and validates data imported into Parasolid.
Click here for more information on the product and services announced by UGS.
—Jonathan Gourlay
SolidWorks Corp. (Santa Monica, CA) released COSMOS 2007 analysis software in conjunction with its release of the 2007 version of its SolidWorks 2007 MCAD design software. COSMOS 2007 offers more than 60 new features that, says SolidWorks, gives designers “the tools to find and correct problems before ]the problems] cost time and money.”
The COSMOS product suite is made up of COSMOSWorks for FEA (finite element analysis), COSMOSMotion for mechanical analysis, and COSMOSFloWorks for fluid analysis. Each module has been extensively upgraded. Among the new features in the COSMOS 2007 suite are virtual sensors that provide quick feedback on a design’s performance. Virtual sensors provide data on specific locations on a 3D model and, in essence, these software-driven devices mimic how a physical sensor works on a prototype.
COSMOS 2007 also offers functionality that automates various time-consuming processes that can damp a designer’s zeal for analysis. For example, a new cyclic symmetry functionality is reported to greatly reduce the time required for analyzing a circular design, as might occur with a turbine blade. COSMOS 2007 now also offers a one-step process to simulate commonly used design elements such as bearings.
New functionality in the COSMOSWorks FEA application includes adaptive meshing for assemblies and weldment/beam analysis. Adaptive meshing lets you analyze assemblies as they will work together in the finished product, rather than as individual components. This new functionality, claims SolidWorks, minimizes the need for refining meshes manually.
Analysis conversion and detection features in the weldment analysis functionality are said to sharply reduce meshing and analysis time. For example, in the weldment analysis environment, a single click—rather than endless line drawing and joint specifying to connect beams and trusses—will convert your structural members into a beam or truss automatically.
The COSMOSMotion upgrade, says the company, focuses heavily on ease of use and interoperability with other COSMOS and SolidWorks software. Its full integration with SolidWorks design software means that you can perform motion analysis directly in SolidWorks, eliminating intermediary set-up steps. COSMOSMotion’s integration with COSMOSWorks Designer lets you design, simulate, and analyze a mechanical assembly in a single, seamless operation.
COSMOSFloWorks fluid dynamics analysis software now features thin-wall analysis technology, which is said to be the first of its kind. The thin-wall technology lets you analyze the flows around and through thin structures by automatically capturing and resolving their geometry.
COSMOSFloWorks supports 64-bit processing, which enables users to solve problems of up to six million cells.
For complete details on COSMOS 2007, to register for an online interactive tour, or to view past online seminars, click here.
The high-performance PXI controller is designed for multitasking environments and multithreaded applications.
National Instruments (Austin, TX) says the PXI-8105, its new dual-core PXI embedded controller, is the industry’s first. It features the 2.0GHz Intel Core Duo processor T2500 for multitasking environments and multithreaded applications. The dual-core PXI controller improves the performance of multithreaded applications up to 100 percent versus single-core PXI controllers with the same processor clock rate.
![]() |
The PXI-8105 from national Instruments. |
With two computing engines in one processor, the dual-core processor can execute two computing tasks simultaneously. This benefits multitasking environments, such as Windows XP, that run multiple applications at one time. In addition, the dual-core processor can simultaneously execute two threads, or tasks, within multithreaded applications, such as National Instruments LabVIEW software.
In NI LabVIEW, engineers can develop multithreaded applications by simply using parallel data flow; e.g., drawing a loop around each segment of the graphical code they wish to execute in a separate thread. The dual-core processor is also suitable for multi-channel, multi-rate data-logging applications using LabVIEW and NI’s DIAdem software or Microsoft Excel because the data acquisition and data storage to the hard drive can run in parallel for optimal performance.
The NI PXI-8105 controller comes with Windows XP Professional preinstalled, saving engineers valuable time in software installation and configuration. It integrates with all National Instruments software, including the NI LabVIEW graphical development environment, NI TestStand test management software, NI LabWindows/CVI for ANSI C development, and NI SignalExpress interactive measurement software. Additionally, it integrates with other common development environments for automated test applications, such as C, C++, Visual Basic, and Microsoft Visual Studio .NET.
Pricing for the NI PXI-8105 starts at $4,499. For further details on the PXI-8105, click here.
Application-specific tool targets the design of electric motors.
MotorSolve, the newest addition to the Infolytica (Montreal, QUE)software family, will offer an FEA-based design environment to focus exclusively on electric motors. According to the company, this will be the first application-specific software its has offered.
Infolytica develops CAE software for magnetic, electric, and thermal analyses. Engineers use the software to design and analyze applications such as electromechanical devices, non-destructive testing (NDT), induction heating, power electronics, sensors, and industrial transformers.
The MotorSolve application is set to be released shortly. For more information, click here.
Subscribe to our FREE magazine,
FREE email newsletters or both!Latest News
About the Author

DE’s editors contribute news and new product announcements to Digital Engineering.
Press releases may be sent to them via [email protected].
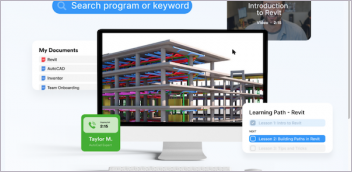

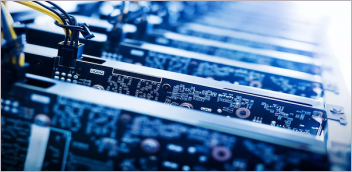
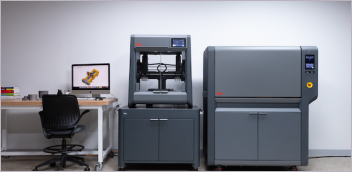