Latest News
May 1, 2013
By David Vaughn
CAE fashions come and go. If you read or listen to software marketing these days, it would seem that multiphysics (MP) simulation is all the rage. Similarly, the word multidisciplinary is making a big comeback as a buzzword in the CAE business.
In fact, the coupling of various physics models—whether it was fluid flow, heat transfer, particle flow, sprays, chemical reactions or even structural stress and deflections—is not new.
It’s Not About Multiple Physics or Disciplines
We talk with our customers a lot about their “grand challenges.” What is it that keeps them up at night thinking, “if I could just _________, that would be a real game changer in my business”? Regardless of which industry they come from, their answers are often quite similar: The majority of these discussions relate to evaluating the performance of an entire system.
For example, a jet engine manufacturer might talk about being able to evaluate the performance of an engine, or the performance of certain components during engine operation. Of course, this could be done with flight testing, but that would require manufacturing a prototype engine in addition to everything else that goes along with testing. The cost and time scales of flight testing do not permit it to affect engine design; rather, it is usually the last phase of engine development that merely validates the safety and performance of the near-final engine design.
But now imagine those engineers have access to a full set of flight test-like data for every design candidate, and this data could be had for a small fraction of the time and cost of a flight test program. This would transform the way business is done in that industry, and have a significant impact on the bottom line.
The obvious solution is simulation. Certainly, CAE analysis is prevalent in traditional engine design, but the grand challenge is putting everything together, simulating the whole system with all its moving parts and complicated physics.
Indeed, this would require CAE software that incorporates multiple physics models and provides data to multiple disciplines, but it is a matter of perspective. You see, the engineering management doesn’t say, “we need to simulate multiple physics,” nor do they say, “we need to analyze several disciplines.” Their goal is to have a virtual flight test program. And in terms of simulation, this equates to a simulation of the full engine system.
Simulating Systems
You might think of simulating systems this way: It’s seeing the “big picture” using simulation. This big-picture approach can be seen in our products, such as electro-chemistry (for battery simulation), electro-magnification, aero-vibro-acoustics, icing, casting, chemistry, combustion, discrete element modeling and many more. Each of these capabilities and features are implemented with the vision of simulating full systems, rather than merely coupling physics models to analyze individual components.
An important point in this concept is using the appropriate fidelity for each model within the simulation. It’s like the old saying, “when you go through life as a hammer, everything looks like a nail.” In terms of this discussion, if you approach it from a finite element analysis (FEA) perspective, for example, you might tend toward modeling the entire system using FEA methods (I could have just as easily said computational fluid dynamics, 1-D, etc.). But the efficient simulation of a complex system must incorporate models at different levels of fidelity in addition to multiple physics/disciplines.
Words can be tricky. Their meaning often depends entirely on one’s perspective. But whether you call it simulating systems, multidisciplinary, MP, tightly coupled, loosely coupled, co-simulation, etc., the key is combining technology innovation with customer partnerships to solve real-world engineering problems through simulation.
David Vaughn is Vice President, Worldwide Marketing for CD-adapco. Before joining CD-adapco, his roles included engineer, consultant, software developer, and product manager at many companies, including Lockheed Martin, Gulfstream Aerospace, Bombardier Aerospace, Airbus, Cessna, AAI, Synaps Inc., and Engineous Software.
Subscribe to our FREE magazine,
FREE email newsletters or both!Latest News
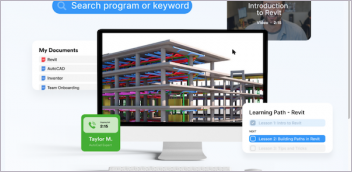

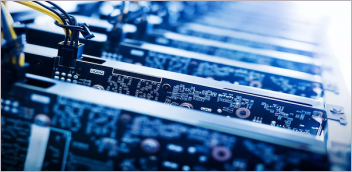
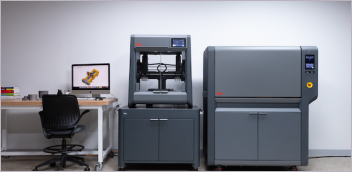