
Latest News
March 28, 2017
As autonomous vehicles get closer to reality, there’s no doubt that the ongoing complexity raises a host of new challenges when it comes to vehicle design and testing.
To ease some of that burden, four companies with expertise in the field of Advanced Driver Assistance Systems (ADAS), sensor fusion, hardware in the loop (HiL) technologies, and simulation and data management are coming together to provide a one-stop solution for fully autonomous vehicle testing. The ADAS IIT (Innovation in Test) collaboration plans to combine their competencies to create a highly scalable, future-proof ADAS test solution based on the National Instruments hardware and software platform and designed to accelerate the delivery of safer autonomous vehicles, according to officials.
The ADAS IIT group comprises Konrad Technologies GmbH, which offers turnkey solutions in electronics manufacturing, high-frequency technology and optics; SET GmbH, a provider of HiL systems; S.E.A. Datentechnik GmbH, an expert in RF and V2X communications protocols; and measX GmbH & Co. KG for data management and test systems design. By combining these key capabilities with NI’s open platform and ecosystem, players in the autonomous vehicle space will have the right set of tools to speed up research and development of new offerings, officials said.
“As real test drives are highly time-consuming, require a lot of test driver resources, and cannot be repeated to 100 percent, virtual test drives are inevitable to test today’s sensors and sensor fusion electronic control units (ECU) for the future autonomous driving,” noted Frank Heidemann, managing director of SET GmbH, in a press release. “Therefore, we bring in our domain expertise regarding highly complex, innovative ADAS HIL test solutions and are thrilled to be part of this leading cooperation.”
For its part, NI says its hardware and software platforms are flexible and adaptable, thus can readily accommodate new technologies like radar, cameras and LIDAR, essentially future proofing existing test architecture and implementations, notes Douglas Farrell, in NI’s Data Acquisition and Control team. Moreover, from a technology standpoint, the breadth of I/O available in the NI platform makes it well suited to these rapidly evolving applications.
“Everything from automotive networks and power measurements for electric vehicles to RF communication for V2X and radar applications is natively supported,” Farrell explains. “More importantly, it is tightly synchronized, which is required for the advanced sensor fusion testing demanded by next generation vehicles.”
Prior to the consortium, building out a turn-key test system that encompassed cameras, radar, LIDAR and V2X meant working with a number of different vendors and doing hands-on integration on your own, he added. The ADAS IIT alliance eliminates the need to do that level of integration and ensures future maintenance and upgrades will be much easier. “Most automotive companies prefer ready to run, turn-key test systems, and obviously dealing with a single one-stop consortium is preferable to dealing with four or more different hardware and software vendors,” he adds.
This isn’t the first time NI technology has been the centerpiece for an industry collaboration. In addition to the ADAS IIT, it has similar efforts in the areas of the Industrial Internet of Things and 5G prototyping. For example, NI’s Industrial IoT lab hosts three testbeds where 18 companies and consortium collaborate to develop next generation solutions.
The ADAS IIT is expected to close in the first quarter of 2017. Upon final completion, more than 300 engineers in Europe, Asia and the United States will work on next steps towards a complete test of fully autonomous vehicles in a virtual environment, from design to development, implementation, validation to production and testing services around the globe.
Watch this video to learn more about ADAS IIT.
Subscribe to our FREE magazine,
FREE email newsletters or both!Latest News
About the Author

Beth Stackpole is a contributing editor to Digital Engineering. Send e-mail about this article to [email protected].
Follow DE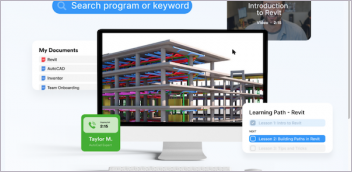

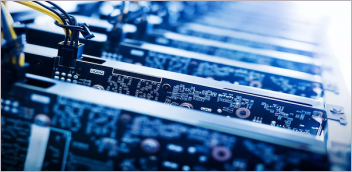
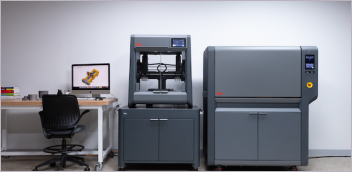