Automated Design Variations Increase Productivity and Lead to Better Product Understanding
Latest News
March 5, 2015
Dear Desktop Engineering Reader:
While not a true double bind, engineers often feel the stress of analyzing and optimizing seemingly contradictory requirements. A classic example is the competing requirements to design an extremely durable part that’s ultra lightweight. The traditional approach to this problem is to run one FEA (finite element analysis) simulation after another, starting each new iteration from scratch with minor modifications of certain parameters. You then collect and sift through piles of results to find a solution that most closely satisfies the requirements. The words “tedious” and “time-consuming” cannot be underused when describing this process.
If you ever approached or still are executing optimizations using a process like that, you’ve probably muttered to yourself at one point something about how computers should be good at this kind of stuff. Well, they can be with the right software, and that’s what the “Automated Design Variations Increase Productivity and Lead to Better Product Understanding” Web resource is all about.
The gist of what’s going on with this resource is that ANSYS Workbench provides an efficient way to run multiple simulations of design variations that won’t cause your eyes to glaze over. Essentially, you set up your model and instruct ANSYS Workbench to execute simulations across a range of input parameters that you define. You can, for example, use – and vary – mesh sizes and boundary conditions as input parameters.
But the key here is that ANSYS Workbench can be bi-directional with major CAD solutions like Inventor, NX and SolidWorks. What that means for you is that you can use your model’s geometric parameters as design variables. This, in turn, provides a means to parameterize your model. You can set up a series of parameters to account for your design variables and then let the analysis software run calculations on all of them automatically. After running all the simulations, you receive a performance indicator that you review and, ultimately, choose the best solution.
The “Automated Design Variations Increase Productivity and Lead to Better Product Understanding” Web resource shows you this in granular detail. The heart of the page is a six-minute (registration free) video demonstration that takes you step-by-step through the process to set up and execute multiple simulations of design variations. It also shows you the results you’d review. Watch it in full-screen mode to see every detail.
For a more in-depth demonstration of this capability, you can register for an on-demand webinar called “Understand and Improve Your Design Faster with Structural Mechanics.” Also available is a technical article that provides another view into this process and a complimentary copy of ANSYS Advantage, the company’s technical journal.
The ability to run multiple simulations of design variations efficiently and without the tedium of once-standard processes could really change the way you synthesize and optimize not only ostensibly contradictory requirements but also more straightforward designs. The “Automated Design Variations Increase Productivity and Lead to Better Product Understanding” Web resource provides ANSYS users a clear, easy-to-grasp tutorial on how they can leverage this capability. For interested engineers, this resource demonstrates just what your computer can do when probably empowered. Hit today’s Check it Out link and see for yourself. Good stuff.
Thanks, Pal. – Lockwood
Anthony J. Lockwood
Editor at Large, Desktop Engineering
Subscribe to our FREE magazine,
FREE email newsletters or both!Latest News
About the Author

Anthony J. Lockwood is Digital Engineering’s founding editor. He is now retired. Contact him via [email protected].
Follow DE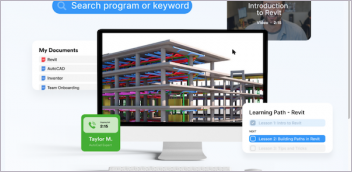

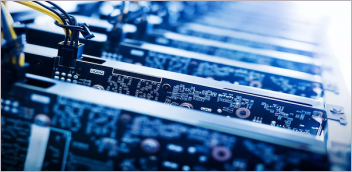
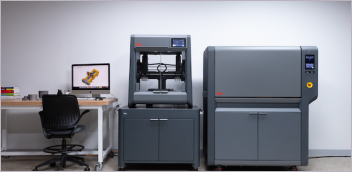