Latest News
March 25, 2012
By DE Editors
AutoForm Engineering has enhanced its hydroforming products. AutoForm Hydroforming contains new functionality for the rapid analysis and simulation of the entire hydroforming process.
One important new feature is the support of cutting process steps. As a result, tube length can be optimized and the forming of tube ends as well as the complete forming process can be simulated. Two cutting types are available: plane cut and laser cut for tube ends trimming and holes piercing.
The AutoForm hydro solver now supports parallel computing achieving significant speed-up levels (comparable to AutoForms incremental solver). At the same time, the number of licenses needed to perform parallel execution has been reduced, offering the user the advantage of multiprocessing at lower cost. The shared memory multiprocessing (SMP) hydro solver is available for 2, 3, 4 and 8 cores. Furthermore, improved and more robust mesh refinement algorithms increase the accuracy of the results. Stress in thickness direction is taken into account allowing for better evaluation of critical areas and more accurate results for thick tubes. Pressure dependent friction is supported, which further enhances accuracy. In addition, the hydro solver has a new simulation status dialog, which provides immediate feedback and helps to prevent misinterpretation of the result files.
For more information, visit AutoForm Engineering.
Sources: Press materials received from the company and additional information gleaned from the company’s website.
Subscribe to our FREE magazine,
FREE email newsletters or both!Latest News
About the Author

DE’s editors contribute news and new product announcements to Digital Engineering.
Press releases may be sent to them via [email protected].
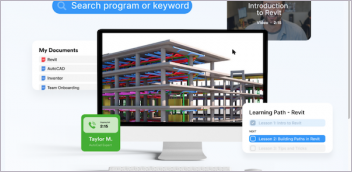

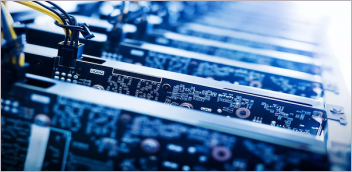
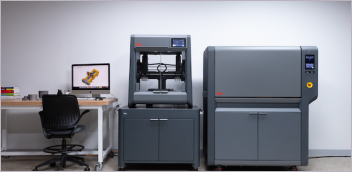